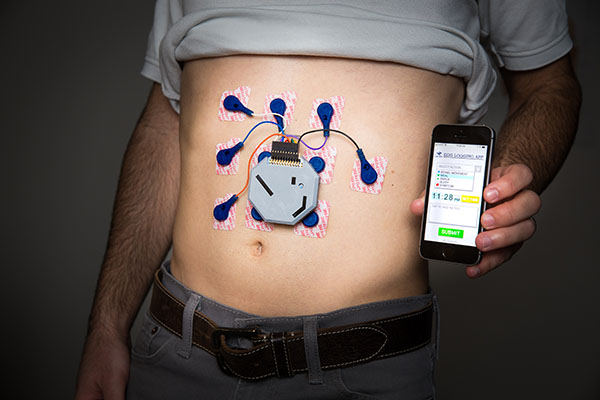
Mellissa McIntyre and Andressa Bonafe discuss medical research in 3D printing and advances in medical innovations.
Clustering is the phenomenon in which firms from the same industry concentrate geographically. The interconnected businesses that compose a cluster enjoy a series of benefits usually reserved for large companies, known as economies of scale. Clusters combine a concentration of expertise and skilled workers, easy access to suppliers, and privileged channels of information, which ultimately decrease costs per unit of output.
Understanding the logic behind clusters can encourage the growth of any business. The resources available are much higher when working in a business cluster of your specialization. This can increase the productivity of a company and foster the scalability of operations. A cluster inspires and facilitates innovation through the proximity of like-minded businesses.
Hollywood, Wall Street, and Silicon Valley are typical examples of US clusters. However, recent years have seen the consolidation of new vibrant clusters, particularly in medical innovation. Universities are key actors both in allowing for clusters to emerge and in guaranteeing their continued success. This article illustrates how university 3D printing research has contributed to medical device clusters across the country, creating a favorable environment for innovative companies. These companies can further enhance their chances of success by taking advantage of federal and state R&D tax credits.
The Research & Development Tax Credit
Enacted in 1981, the federal Research and Development (R&D) Tax Credit allows a credit of up to 13 percent of eligible spending for new and improved products and processes. Qualified research must meet the following four criteria:
-
New or improved products, processes, or software
-
Technological in nature
-
Elimination of uncertainty
-
Process of experimentation
Eligible costs include employee wages, cost of supplies, cost of testing, contract research expenses, and costs associated with developing a patent. On December 18, 2015 President Obama signed the bill making the R&D Tax Credit permanent. Beginning in 2016, the R&D credit can be used to offset Alternative Minimum Tax and startup businesses can utilize the credit against $250,000 per year in payroll taxes.
University 3D Printing Research and Medical Innovation
The U.S. Cluster Mapping Project identifies leading medical device clusters in the country by presenting the states that employ the highest number of people in this particular industry.
The following sections argue that university 3D printing research in these locations help medical device companies decrease costs and increase productivity while also serving as a source of expertise and a basis for innovation.
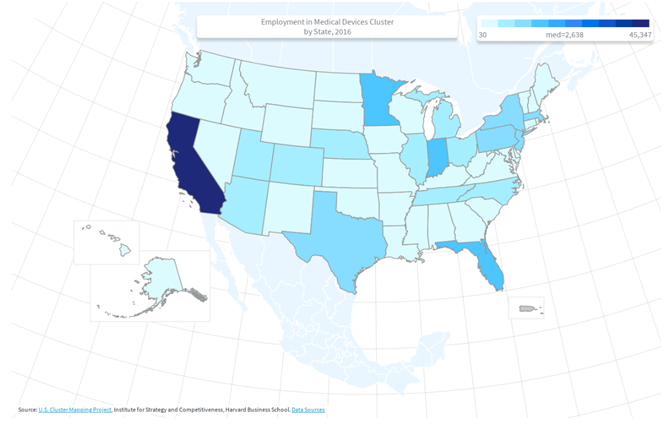
I. California: At Stanford University, a researcher developed custom cardiac devices using 3D printing. The research team is exploring methods to survey electricity in the heart and using 3D printing tools to design cardiac mapping catheters, with the intention of customizing the devices to the patient and thus reduce risk of errors in the electrical activity reading.
At the University of California at Berkeley, a team of researchers developed a wearable device to monitor stomach activity for 24 hours (see image at top of article). The noninvasive device is a 3D printed box with 10 small electrodes for monitoring the stomach activity of patients outside the clinical setting. More recently at UC Berkeley, researchers teamed up with Carbon and colleagues at other universities to develop a 3D printed “drug sponge” to help reduce side effects in chemotherapy.
II. Indiana: At Notre Dame University, an engineering student, Michael Skinner, and his team, were able to gift a set of 3D printed hands to an eleven-year-old girl who was born without them. This was possible because of access to 3D printers and an online community known as e-NABLE. The community is a global collaboration of students and engineers for open-source, 3D-printable designs for prosthetics. The team was able to customize the design to present to the girl using the facilities available at Notre Dame.
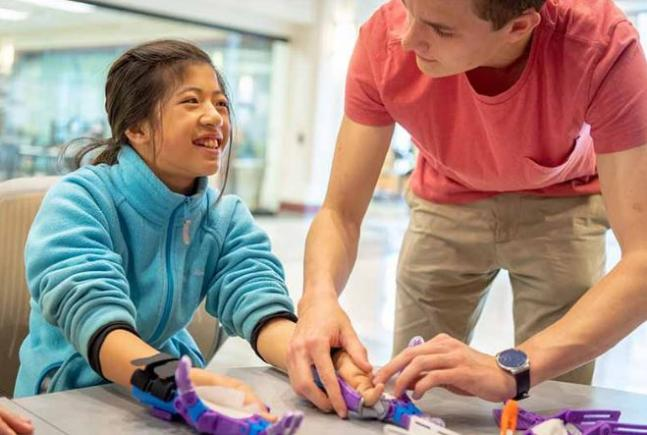
III. Florida: The University of Miami College of Engineering is home to one of Johnson & Johnson’s facilities, the 3D Printing Center of Excellence Collaborative Laboratory. The facility is stocked with a variety of 3D printers and other fabrication equipment with full-time engineers or scientists available to students and faculty for use in prototyping and materials development in medical applications.
IV. Minnesota: The University of Minnesota developed a method for printing electronics directly on a human hand. This technology could be used to print temporary sensors to detect chemical or biological agents in the field. Researchers also printed biological cells directly on the skin wound of a mouse, a breakthrough that lends insight into wound healing strategies and techniques using a bioprinter. The McAlpine Research Group at UMN also successfully 3D printed optoelectronic devices using polymer photodetectors on hemispherical surfaces designed for visually impaired patients.
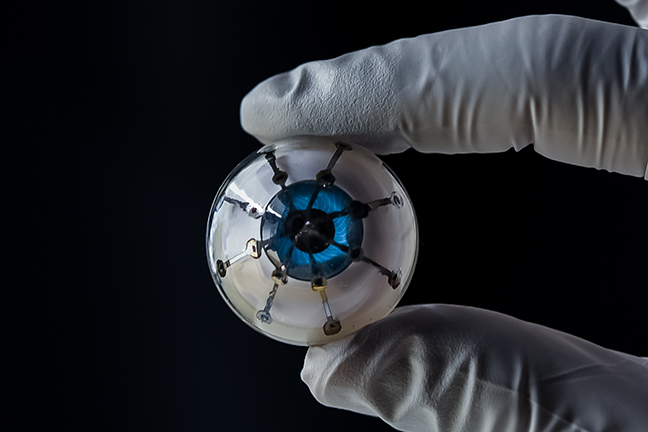
V. New York: At Columbia University Medical Center, doctors created a 3D printed knee meniscus that allows doctors to completely replace the torn tissue with a biodegradable scaffold infused with connective growth factor.
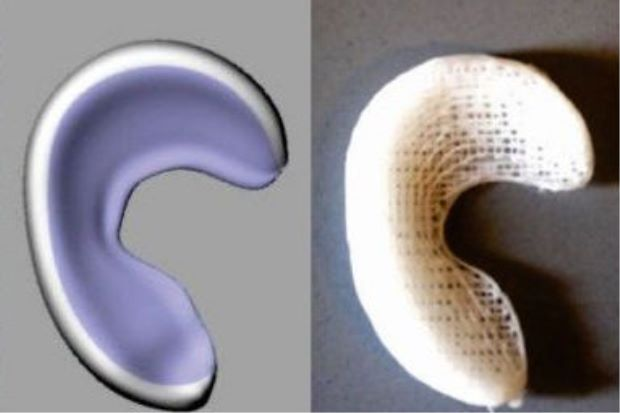
In 2017, researchers at Cornell University used 3D printing to model an artificial small intestine that mimics the gut surface topography and the fluid flow required for the epithelial cells in the gut to grow and function. It also realistically models peristaltic flow which was a common downfall of previous models. The Model can be used to more closely study the function of a human small intestine for research and diagnosis.
VI. Pennsylvania: At the University of Pittsburgh, a bioengineering PhD candidate is working to develop a 3D printed phantom head to mimic the natural structure of a human head. The realistic model could be used to test electromagnetic applications, particularly MRI devices. At Temple University, a professor created 3D printed bandages made from soy. This is a prototype for electrospun healing device that uses soy protein and water to print the bandage directly onto the patient’s skin.
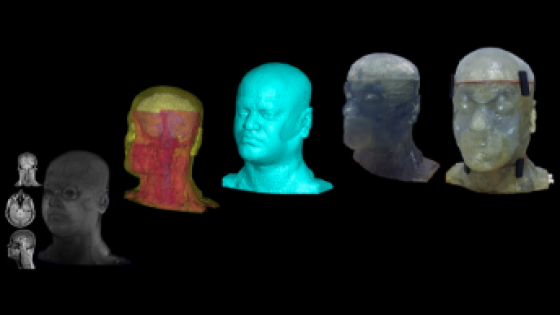
VII. Texas: Rice University students developed 3D printed training models in order to facilitate training in diagnosis and treatment of cervical cancer. The 3D printed model will be used in healthcare education to combat the deficit in adequate detection and treatment of cervical cancer in developing countries. It is useful in modeling different procedures such as colposcopy, cervical biopsy, cryotherapy, and loop electrosurgical excision procedure.
Another team of students from Rice University used additive manufacturing to model a realistic heart to research and facilitate the development of the next generation of pace makers. Instead of the traditional pulse generator located in the patient’s chest, the students use a network of chips which communicate with a base station under the skin to regenerate the heart when a problem is sensed.
VIII. Massachusetts: In 2018, researchers at the Massachusetts Institute of Technology and Draper 3D printed a microfluidic device to aid in personalized cancer treatment. This emphasizes the importance of patient-specific care using 3D printed medical devices. The device simulates the treatment of cancer on a biopsied cancer tissue. This can help researchers determine the how individuals may respond to a particular treatment prior to the administration of any treatments. This technique can reduce risk of medication failure by a significant amount with more personalized and inexpensive healthcare.
Another group of researchers at MIT, Draper, and Brigham and Women’s Hospital developed a 3D printed ingestible capsule which can be controlled wirelessly to detect infections, allergies and other conditions affecting the human body with a minimally invasive procedure. There also exists the potential for the device to deliver medications for a more targeted healthcare approach.
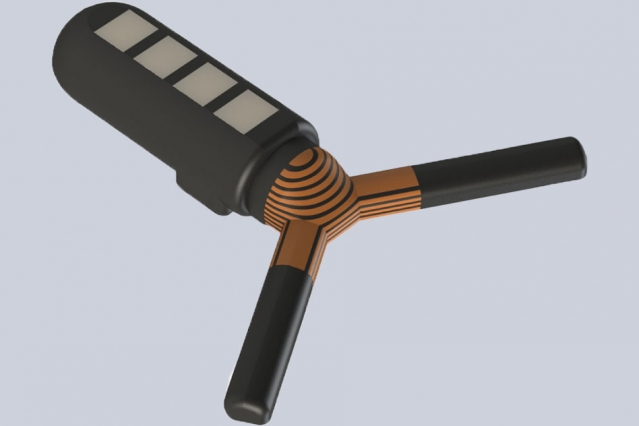
Harvard University engineers developed a fully functional organ-on-a-chip which is a microfluidic device used for cell culture to simulate the activity of a particular organ. In this case, researchers developed the 3D printed heart-on-a-chip with integrated sensing which can be fully customized with quick turnaround for the purpose of collecting reliable data for studies.
Also, in addressing patient specificity, researchers at Northeastern University developed a 3D printing technology which uses magnetic fields to work with composite materials into patient specific products. The technology can be used to revolutionize biomedical equipment to customize treatment for everyone including premature babies and implant procedures.
IX. New Jersey: A PhD student at Stevens Institute of Technology leveraged 3D printing manufacturing to produce scaffolds for spinal implantation at 8 cents each.
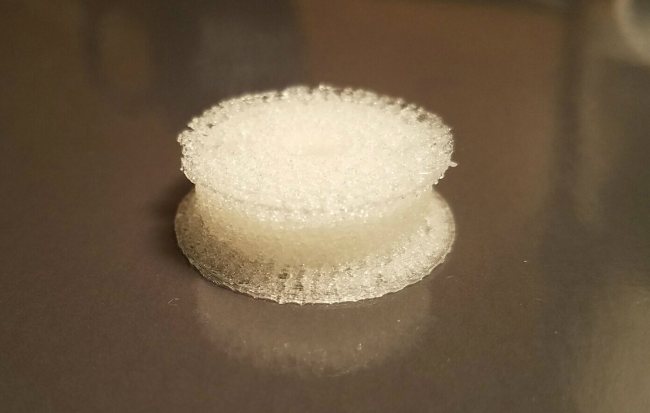
Researchers at Rutgers University used 3D printing to produce a smart gel that can walk under water, grab and maneuver objects. The gel could potentially be used in diagnosis, detection, and delivery of drugs.
Conclusion
3D printing research in some of U.S. leading universities has spurred growth in medical device clusters. Innovative companies that benefit from the economies of scale generated by these clusters should also take advantage of R&D tax credits available to support the creation of new and improved products and processes.
FELIXprinters has released a new bioprinter, the FELIX BIOprinter, which is quite a change for the long-time 3D printer manufacturer.