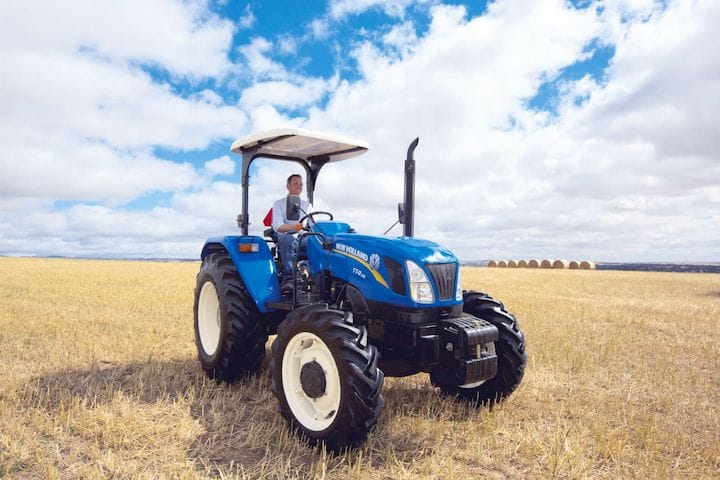
One application primed for disruption by 3D printing technology is the production of spare parts.
After all, why house a warehouse full of odd components for just the right moment when you or a customer will need one?
This is especially true for large, unique systems and equipment, where mass production of individual specialty pieces is that much rarer. London and Amsterdam-based CNH Industrial has picked up on this insight and has begun fabricating spare parts for its industrial equipment.
A subsidiary of the Agnelli family-owned Exor investment company, CNH is one of the world’s largest capital goods businesses, making a wide variety of equipment for a range of industries, including: agriculture, construction, industry, marine and civil society.
It has 63,000 employees spanning 66 facilities around the globe and rakes in $27 billion with its brands that include CASE construction equipment, Iveco bus and New Holland agricultural machinery.
The company has 3D printed four different spare parts to be used on its buses and agricultural equipment. These parts have been printed in plastic, but CNH plans to continue testing the possibility of 3D printing metal components for use in the near future.
The ultimate goal for the business is to additively manufacture “a full range of parts and promptly respond to all types of needs at every stage of the product’s lifecycle.”
CNH sees the benefits of 3D printing spare parts in the need to quickly fabricate small numbers of parts locally and on-demand. This, in turn, results in better stock management and availability, with parts made in just 24 to 36 hours.
Read more at ENGINEERING.com
Healthcare 3D printing attempts to solve two problems that plague providing care: customization and cost.