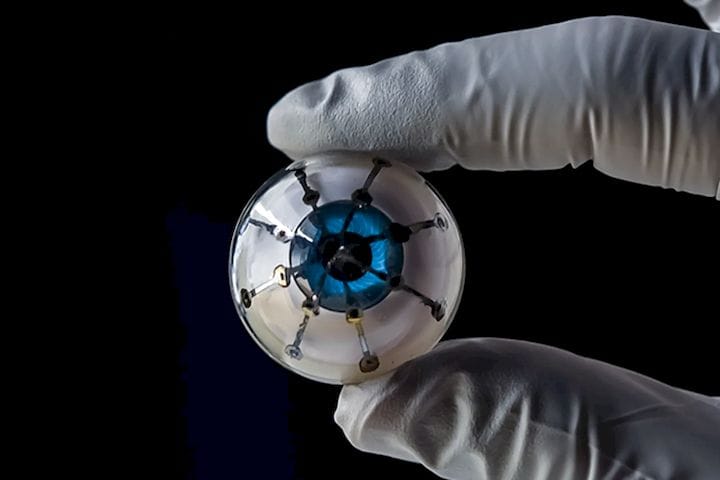
In 2015, market research firm Gartner projected that medical 3D printing would become the pioneering field that would drive additive manufacturing (AM) into the mainstream in two to five years.
Four years have passed, so we’ve decided to examine the industry to determine if Gartner’s predictions have come true.
In this article, we’ll explore a handful of medical 3D printing stories from the past year to gain perspective on the level of adoption at which the technology stands.
3D-Printed Implants
In August 2018, Osseus Fusion Systems received its fourth FDA 510(k) clearance. This time it was for its Aries family of 3D-printed lumbar interbody fusion devices. The Dallas-based company’s devices are printed using Osseus’s proprietary 3D-printing platform, PL3XUZ.
With porosity at 80 percent, according to the company, these 3D-printed parts are some of the most porous spinal implants available. A proprietary mesh lattice design enables the implants to reduce stiffness while increasing bone cell growth, one of the key drivers of adoption of 3D printing in the creation of implants and radiological visibility.
The first Aries-L lateral interbody parts were implanted into a patient for the first time in January 2019. It is important to note that the implants were patient-specific, one of the most important promises of 3D-printed medical devices geared at improving treatment outcomes.
“Through 3D printing, we are able to manufacture spinal implants that are customized to the patient,” said Dr. Sam Joseph, Jr., who was involved in the procedure and aided in the development of the Aries series. “Meaning the size of their disc, the size of their vertebra, how high the vertebra may be, as well as the curvature they may have in their back we are trying to create. With this cutting-edge technology, we can offer our patients implants such as the Aries L Interbody Fusion Device that can be created at a certain height and a certain length, as well as a certain angle, which offers our patients better, customized care, which results in better outcomes for the patients.”
While 3D-printed spinal, craniomaxillofacial and knee implants are increasing in number, 3D-printed orthopedic devices may be the most prevalent, led in part by GE Additive subsidiary Arcam. So far, over 100,000 hip cups have been produced since 2007 using Arcam’s electron beam melting (EBM) technology. LimaCorporate, an Italian orthopedics company and Arcam customer, has been a pioneer in the space. It performed the world’s first 3D-printed hip implant, made using EBM.
LimaCorporate recently partnered with New York City’s Hospital for Special Surgery to establish the first AM facility for custom implants in a hospital environment. Whereas implants are typically 3D printed offsite with specialists like LimaCorporate, the new facility will make it possible to produce the devices closer to the point of care, reducing wait times and shipping. Expected to open in 2020, the new site will be operated by the Italian firm and serve hospitals across the U.S. with custom implants while also developing new medical products.
Bioprinting
The holy grail of bioprinting is the ability to 3D print patient-specific transplant organs, thus eliminating the need for waiting lists and donors and, more importantly, the fear of organ rejection. We are still likely years away (five to 10 years, according to Gartner in 2017) from achieving that reality, but the base technology is still advancing.
For instance, it is now becoming commonplace to 3D print layers of simple tissues. Multiple companies having developed products associated with research applications. This includes Poietis, which has created a laser-based method for 3D printing biological matter, such as skin cells. The company has established several partnerships related to 3D printing liver tissue for pharmaceutical testing and cartilage. In early 2018, Poietis became the first to release a commercial 3D-printed skin product, which led to partnering with BASF and L’Oreal.
Another leader in the space is CELLINK, which has quickly expanded since it was founded several years ago. The company now features six bioprinters on the market, four based on extrusion technologies, and 30 to 35 bioinks. Initially, the majority of customers have been pharmaceutical researchers looking to test drugs on human tissue.
Already this year, we’ve seen the introduction of the first consumer product relying on bioprinting. At CES, Johnson & Johnson (which is deeply immersed in the medical 3D-printing space) showcased the Neutrogena MaskiD, a 3D-printed facemask produced based on 3D images of a customer’s face. Using a selfie taken with a smartphone 3D camera, the Neutrogena Skin 360 system determines the placement of necessary ingredients for dermatological treatment based on a person’s face. A custom-fit hydrogel mask is 3D printed from cellulose made using locust beans and red seaweed, along with Neutrogena skincare ingredients, and delivered to the customer.
There is still much work to be done to perfect the bioprinting of vascular structures necessary to bring blood and nutrients to bioprinted tissues, thus opening up the possibility of fabricating patient-specific organs for transplant.
Read more at ENGINEERING.com
Healthcare 3D printing attempts to solve two problems that plague providing care: customization and cost.