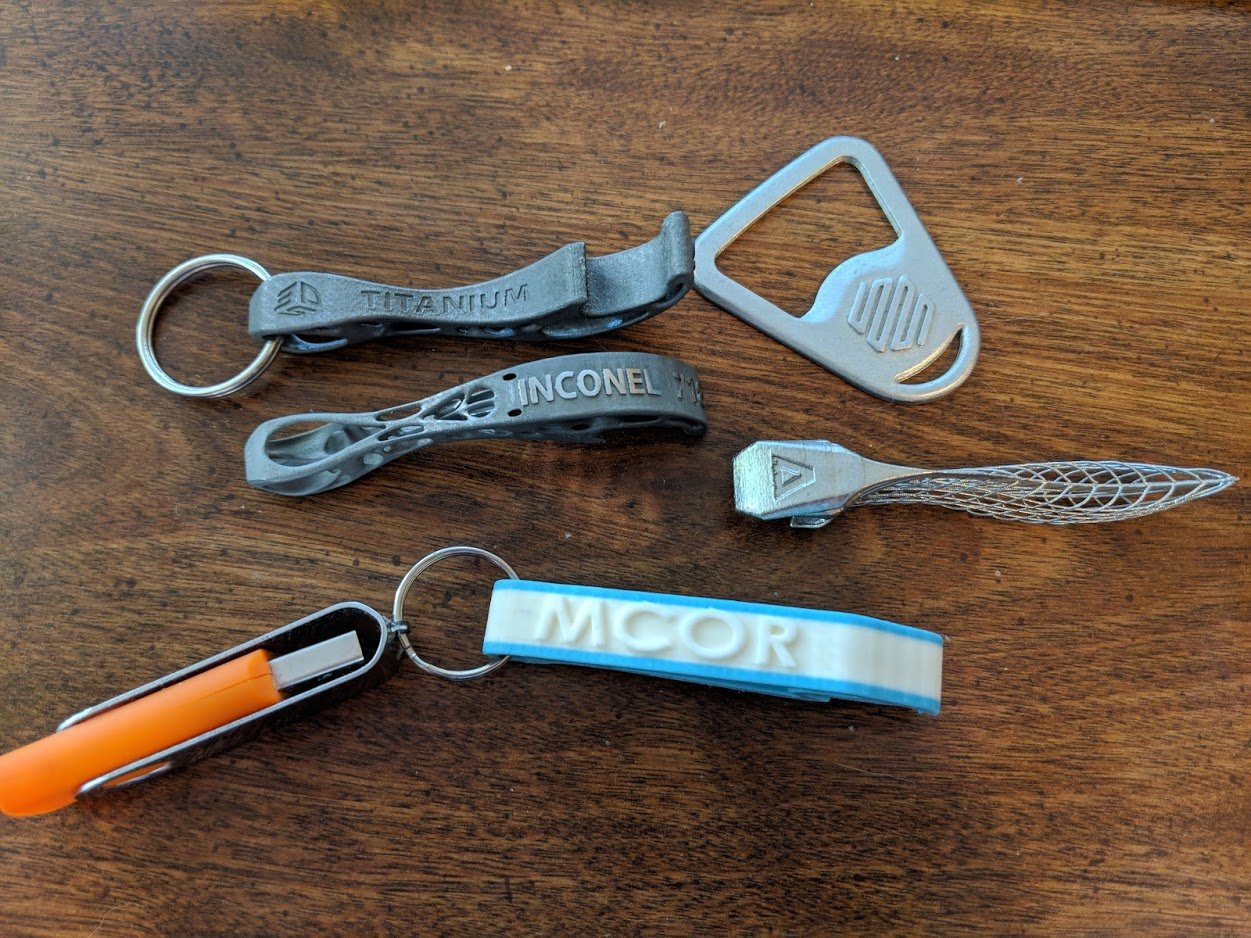
I recently realized nearly every bottle opener in my house is 3D printed.
They’re mostly metal – from the likes of Markforged, 3D Systems (in both titanium and Inconel), and Velo3D – but one is made of paper (from Mcor). They all work, and they’re all used in regular rotation on bottle-opening occasions in my home. Do I really need a topology optimized bottle opener made of Inconel? No, not really; so why does it matter that I have one?
3D printing is still a young technology, and it’s proving itself – slowly.
Adoption remains overall relatively low. While sales and installations are rising at a fast pace, part of the dynamism seen in those numbers comes simply from their small base. Doubling sounds great, but moving from one to two is doubling just as technically as moving from 500 to 1,000 is; which one is actually more impressive? In their own way, each is very impressive, as growing quickly from a small base usually means there’s something supporting that base. Adding significantly to an already-large number means there’s something substantial supporting it already and a rising investment in seeing that ‘something’ continue to grow.
We talk a lot about what it takes for production applications to more fully embrace 3D printing:
-
Standards
-
Repeatability
-
Process and material qualifications
-
Cost equivalence or reduction
-
Relevant industry certifications
These things don’t just happen from nowhere. There has to be some proof of concept first.
3D printing has its roots in prototyping, so proofs of concept are certainly no stranger for this industry. How do you prove something works? By showing it working.
These bottle openers might seem like kitschy knick-knacks or oh-look-another-gimmicky-giveaway or this-big-thing-will-help-me-find-that-USB-stick-later and to some extent they are. And that’s okay. It gets them into hands, and that gets them into use. Did I start using the Mcor bottle opener out of curiosity? Absolutely. Does it still work a few years after receiving it? Every time.
Do they all work? Perhaps unsurprisingly, a PLA bottle opener shaped like a slice of pizza with an embedded penny for the actual heavy lifting on the opening job didn’t survive too long – maybe two or three uses. That’s my only failure from my admittedly tiny sampling.
The materials and geometries of each bottle opener I have are different, offering unique user experiences and highlighting different aspects of design capabilities for the technologies represented. The sturdy solidness of the Markforged piece is a nice contrast to the intricate, seemingly-delicate lattice structuring of the surprisingly strong Velo build, and each serves as an underline to each company’s claims about its offerings.
One of the best aspects about these small builds, though, is the ease with which they convey their messaging. They’re small, and certainly a dozen or more could have been made at a time depending on the exact geometries and build envelopes in question. But then they went home with journalists and other visitors to the trade shows / facilities where they were given out. It’s one thing to handle a part in a booth; it was carefully selected to be a display piece and gets bundled back up to return to the home office following each show. The hands-on time for media and visitors is invaluable, as we have the opportunity to touch what we may only have read about or seen photos of outside of that encounter. These bottle openers, though, leave this controlled environment and go into our offices, into our homes.
Nothing says real-world condition testing quite like having a few bottle openers out and ready for casual use at a backyard barbecue. They’re dropped, they’re used back to back to back, they’re perhaps forgotten outside for a time in the elements; in short, they’re out in the world doing exactly what any bottle opener does.
Having real-world hands-on usage is an excellent way to highlight actual capabilities. It’s why I wear my 3D printed insoles and 3D printed shoes every chance I get; after a while, that they’re 3D printed matters only because I can offer full reviews, whereas the rest of the time they’re simply functional items doing what their creators say they can do.
Sending small, functional builds into the world is a smart move from these companies, as actual users and media have the ability to check things out in their own time and in their own environments.
[All images: Fabbaloo]
Healthcare 3D printing attempts to solve two problems that plague providing care: customization and cost.