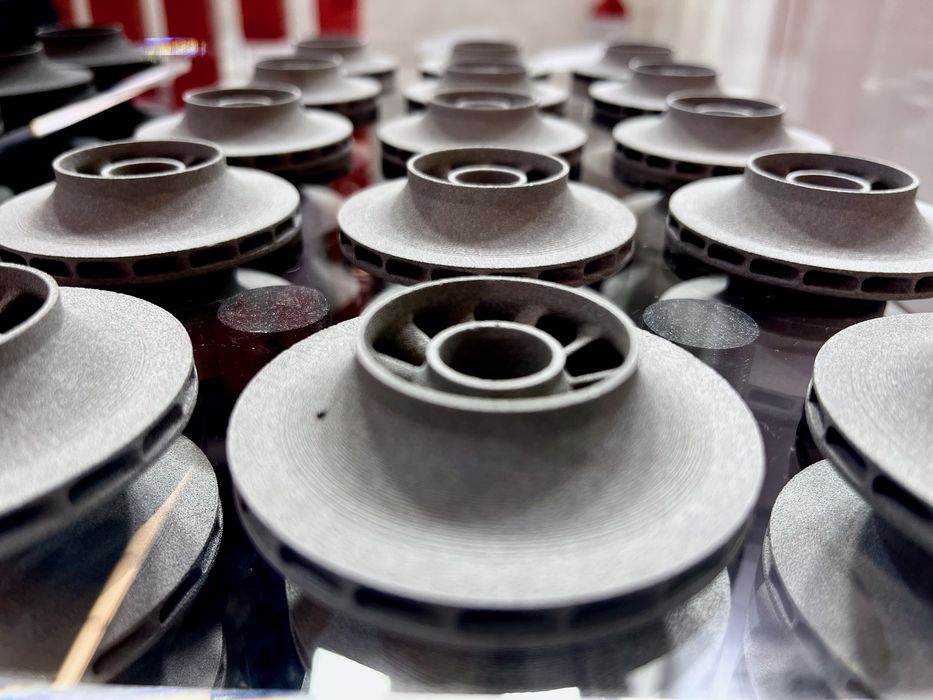
A research paper on a future zero-emission steel future has implications for additive manufacturing.
The paper, entitled, “Limited quantity and quality of steel supply in a zero-emission future”, investigates the production and use of steel material in a future where we’ve mostly switched to zero emission activities.
Zero emissions are a target today, but if we are to survive they will at some point become real. If so, that would include the production of steel, an extremely common building material for structures, vehicles and other items.
According to an Australian report (PDF), a tonne of steel produced will generate 1.83 tonnes of CO2, which is significant. When you scale this up to the total amount of steel production in the world, you find that this represents between six to nine percent of ALL global CO2 emissions. The production also consumes around six percent of total global energy.
The reason for this CO2 intensity is that steel is produced in blast furnaces that typically use fossil fuels for heat, and carbon from fossil sources as a reduction agent.
Those are enormous numbers, and they obviously have to be reduced as soon as possible.
One of the key pillars of a zero emission steel production world would be the ability to recycle old steel for new uses. This would avoid the incredibly large amount of CO2 emitted by today’s typical steel production processes.
The researchers found that most steel scrap is recycled into construction materials, rather than re-used in automobiles, for example. They explain:
“Using Japan as a case study, our analysis shows that most steel scrap is currently downcycled into construction materials, thereby limiting scrap-based steel to only 20% of the total steel used for automobiles, compared to 60% for buildings. Under a strict carbon budget, such downcycling practices could limit the production of steel used for automobiles to ~40% of current levels by 2050, even if production technology progresses according to the roadmap.”
Very worryingly, they also explain:
“The results indicate that steel users should not take the current level of steel supply for granted in a zero-emission future. Decarbonizing the steel sector, therefore, will depend not only on stand-alone efforts by the steel industry but on joint action with steel users to enable scrap upcycling and service provision with less steel use.”
So it would seem that steel for certain industries could become short in supply in years to come. That would raise prices on many products.
But what about additive manufacturing, where steel (particularly stainless steel) is a very commonly used metal 3D print material?
Metal 3D print powders are already quite expensive, but this research suggests that it could become even more expensive.
One thought is that it may be that industries turn to 3D printed applications more than they do today, because there is less waste. That waste, typically made by CNC milling, according to the researchers, would fall out of mainstream steel reuse as above.
By using additive techniques the amount of waste could be considerably reduced. If the price was right, then we could see a significant move towards additive manufacturing.
Another possibility is to change the recycling technology. You may recall 6K Additive’s unusual microwave-based production method for producing high quality metal powder. This approach is quite different from typical methods, and apparently is able to directly use scrap metals. This technology would seem to solve the problem posed by the researchers.
One way or another, those performing metal additive manufacturing will have to deal with significant change in the future.
Via Nature