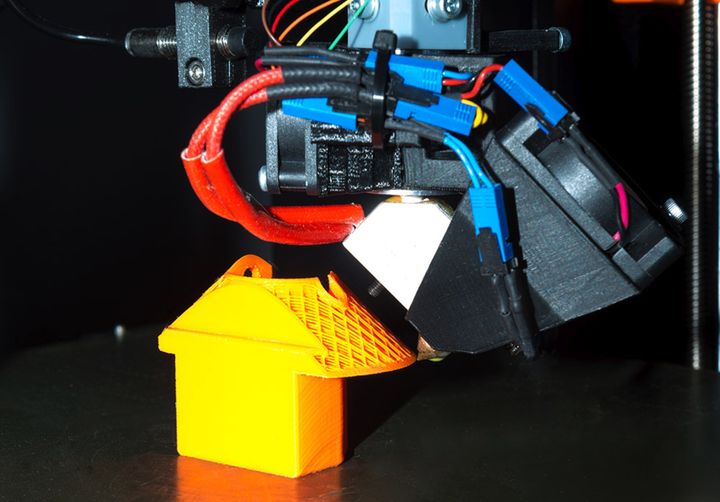
Researchers at the Zurich University of Applied Sciences (ZHAW) have developed a novel approach to 3D print extrusion that could transform many desktop 3D printers.
The researchers were concerned with the frequent need for support materials during complex 3D prints. The use of support material significantly complicates 3D printing for a number of reasons:
- Dual extruders are required, raising machine cost
- Separate and usually expensive support material is required
- Some soluble support materials require specialized storage and handling
- Support extrusion lengthens print job durations
- Support removal is a tedious, labor-intensive post-processing step
- Surfaces can be made rough by adjacent support material that’s been removed
It’s clear you really don’t want to 3D print with supports unless you absolutely have to do so. In fact, I often find myself looking very carefully at each 3D model in hopes I can avoid supports entirely. However, I’m often not successful and have to use support material. Everyone wants 3D printing without supports!
That could change with a new development. The researchers built an experimental new 3D printer extruder that has two very different characteristics:
- The hot end is angled at 45 degrees instead of being vertical
- The hot end can rotate in a circular path
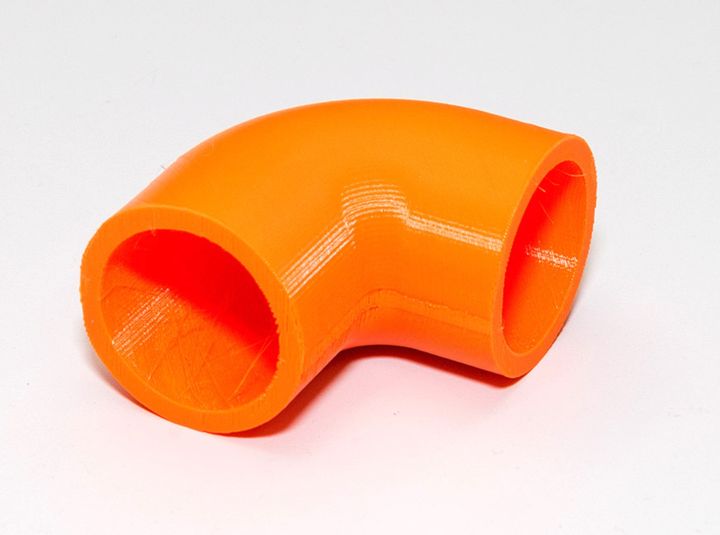
These two characteristics are very interesting. The 45 degree angle is an innovation we’ve seen on the several new belt 3D printers that have recently emerged. By combining that angle with a belt than moves laterally, belt 3D printers are able to avoid the need for significant support material, at least on one side of the print. However, experienced belt 3D printer operators would orient their parts to minimize support requirements.
That same principle seems to used in the ZHAW approach. Please watch this video to see the system in operation:
They call their system the “RotBot”, and the head of the research area, Wilfried J. Elspass, said (via Google Translate):
“Our RotBot’ 3D printer is able to print any structure without support material. This means that, firstly, we need less material, secondly, the printing times are shorter and, thirdly, post-processing — i.e. the removal of support material — is completely eliminated.”
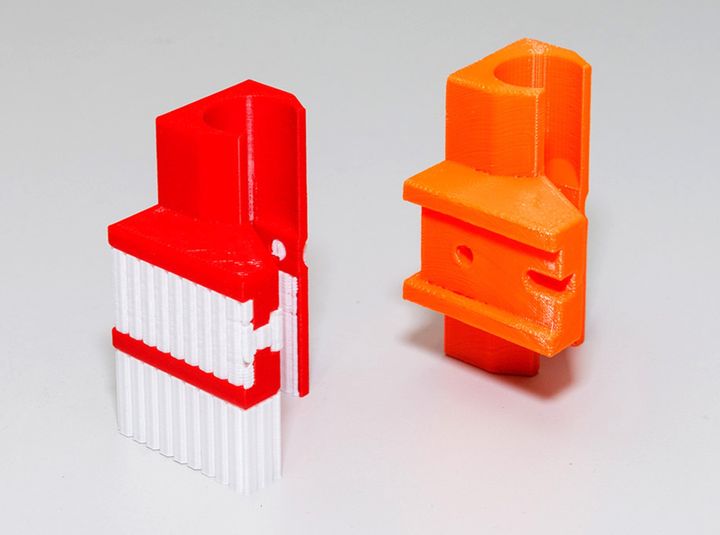
As you might imagine, the toolpath for RotBot 3D prints differs significantly from standard Cartesian 3D printers, which process 3D models layer-by-layer. It also differs from the toolpath of belt 3D printers, which use slices at 45 degree angles through a 3D model. Instead, RotBot uses cone-shaped layers.
The 3D printed objects are essentially built from the inside out!
I’m not totally convinced this completely eliminates the need for support material, as I can envision some pathological object geometries that might not fit well in the cone environment. That said, this approach would certainly eliminate a massive amount of support material.
The inspiration for the RotBot came from the researchers’ use of a six-axis 3D printer, which can also 3D print without support structures. While that approach also works, it is significantly more expensive than a conventional 3D printer due to the added hardware features and far more complex software. They sought a solution that could modify an existing Cartesian 3D printer to allow for similar processing, and it seems they’ve managed to do just that.
In their images it’s clear they’ve successfully modified a standard Prusa Research MK3S desktop 3D printer to use the RotBot system, and it works. The 3D printing technology is the same, but the motion system is quite different.
The researchers believe it would be possible to create relatively inexpensive upgrade kits for popular desktop 3D printers to transform them into RotBot mode. If they follow through with a commercialization of their new 3D printing process, we could see a significant change in the 3D printer market. A 3D printer that doesn’t require support material is quite a valuable item: just consider the number of 3D printer manufacturers that have recently added a second extruder simply to allow for support material use. These more expensive devices could face a number of new competitors using RotBot technology.
I have many questions about RotBot, and one of them relates to 3D printer settings. Typically the settings are used to specify the type of infill for a 3D print job, including the density and fill pattern. I’m wondering how this would work if you are building an object from inside-out? Do you 3D print a sparse zone and then add a perimeter at the end? What would the exterior surface quality look like? How strong would the infill be compared to a conventionally printed part? These and other questions need answers before RotBot can be commercialized.
However, if available, I’m sure I’d get one. Would you?
Via ZHAW (German) (Hat tip to Benjamin)