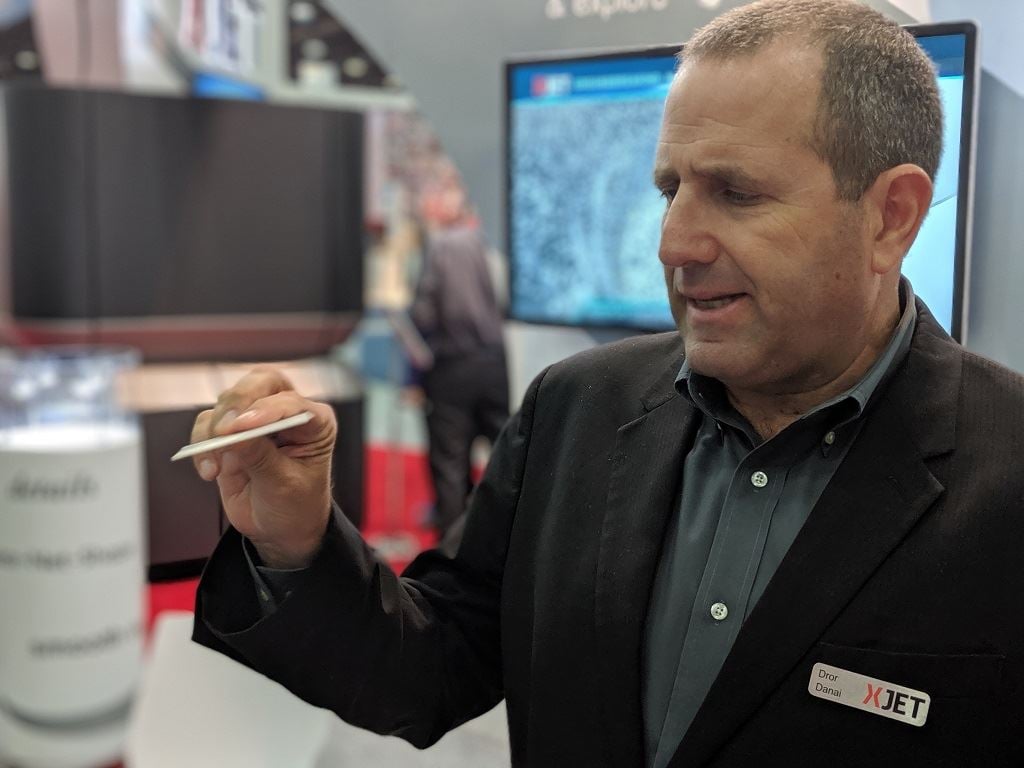
I spoke with XJET’s Dror Danai to find out why XJET technology has an advantage over other ceramic 3D printing options.
I’ve followed XJET since they first appeared on the scene more than five years ago. The company introduced a very unusual 3D printing process unlike any other: NPJ, or “NanoParticle Jetting”.
While the company first seemed to direct their technology towards metal 3D printing, it now seems their major niche is ceramic 3D printing, which has proven popular among their many customers. However, they still 3D print metal, and have even found a way to uniquely 3D print both metal and ceramic material in the same print job.
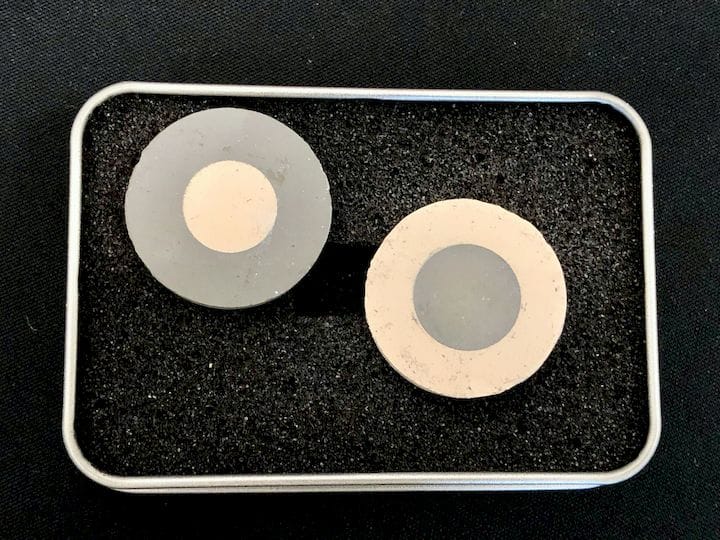
The ability to 3D print both ceramic and metal is due to the NPJ process, in which tiny droplets of liquid are infused with nanoparticles of different materials, including ceramics, metals and soluble support material. As each layer is swiftly deposited, the liquid holding the nanoparticles evaporates due to heating, leaving just the model and support materials.
Completed prints undergo a sintering process to finalize their solid structure. You can see how the NPJ process works in this video:
The process is easily understandable and definitely works, but what advantages does it have over other metal and ceramic 3D printing systems? I spoke to XJET’s Dror Danai to find out his thoughts.
Danai said:
“I want to crystallize the message of the difference between XJET and other metal technologies. We are very unique at certain things: Soluble support, we are the only one that’s powderless, the only one that has direct jetting. Others add energy to fuse particles in the powder bed.”
This is quite true: NPJ does not use powerful lasers that generate significant amounts of heat to melt metal. In the NPJ process, the major heat is applied during the sintering stage, where the part receives heat all at once in a separate device.
Danai emphasized the difference between XJET and other powder-based non-laser 3D printing systems, such as those from Desktop Metal and HP. He explained:
“Most powder systems have limitations, like layer size, particle size, etc. Ours is more like dust, not powder — you can even see through it!
This leads to a much higher volume of particles. They have 50X smaller diameter, but 50^^3 in three dimensions.”
Each droplet in the NPJ process contains a large number of extremely small ceramic or metal nanoparticles, suggesting that XJET’s process can achieve much higher resolutions and surface smoothness.
Danai explained further:
“There are benefits to users: fine details, accuracy, smoothness, and not just a little bit smoother. The second best parts are 2X worse in smoothness. Our parts, right out the furnace, have variation of only 1.6 microns on the top layers, whereas everyone else is 3.2 to 6.4, generally.”
This is where it gets interesting: if a machine can provide this level of resolution, what does that mean to a designer? How can a designer take advantage of this capability?
From what I’ve seen, XJET clients have been producing unusual industrial objects in ceramic and metal that have extremely fine details.
Danai said:
“You cannot achieve this smoothness right out of the printer with any other technology. However, you can always get it with extra post-processing work.”
This is an interesting point: a considerable portion of the cost to produce a 3D printed part is often the post-processing labor. If it were possible to reduce or eliminate some of that work, then the cost per part could drop noticeably. Danai said NPJ can save on labor and at the same time minimize the risk of damaging parts during post-processing.
Finally, there’s one more advantage over powder systems: because NPJ is liquid-based, there is no danger of airborne particles, as is the case with most powder-based 3D printing processes. In the case of high-end metal 3D printers, this is a very dangerous hazard, because some metals when airborne are actually explosive, and significant steps must be taken in machine and site design to mitigate those risks.
Via XJET