
XJET announced “SMART”, an intelligent post-processing workstation.
The company’s Nanoparticle Jetting process (NPJ) involves the use of support material when producing ceramic and metal parts. NPJ involves inkjet-like print heads that selectively drop liquid material. The liquid contains nanoparticles of the desired material, and the liquid is baked off during a post-processing step, leaving the ceramic material.
Since NPJ also uses support structures, a key step in the post-processing sequence is to remove them. XJET’s new SMART station is able to do that effectively and intelligently. XJET’s support material is water soluble.
“SMART” is actually an acronym for “Support Material Automatic Removal Technology”, and that’s precisely what it does.
The device includes a number of different programs that can automatically take a build plate through the optimal steps of support removal without the need for operator intervention aside from loading and unloading. The programs are tuned for the different materials offered for XJET NPJ equipment.

You might be wondering why XJET would announce this device, given that water soluble prints are typically pretty easy to process. Soaking in water and some elbow grease gets the job done, so why the need for a dedicated cleaning device?
It turns out the key is production. By automating the process, the need for labor is greatly decreased, as well as the turnaround time. XJET CBO Dror Danai explained:
“One of our beta customers has reported a 90 percent reduction in cleaning time and hassle using the XJet SMART station, so we’re delighted with the results! Additive manufacturing is supposed to offer true design freedom and complex geometries with zero additional cost. Our soluble support material delivers those capabilities – even for tiny cavities. Now with the SMART station our customers can benefit from simple, predictable, low-cost operation.”
Evidently XJET examined the workflows used by many of their clients and quickly noticed an inordinate amount of time being spent post-processing parts where an automated solution would be possible. That was the trigger for developing the SMART station.
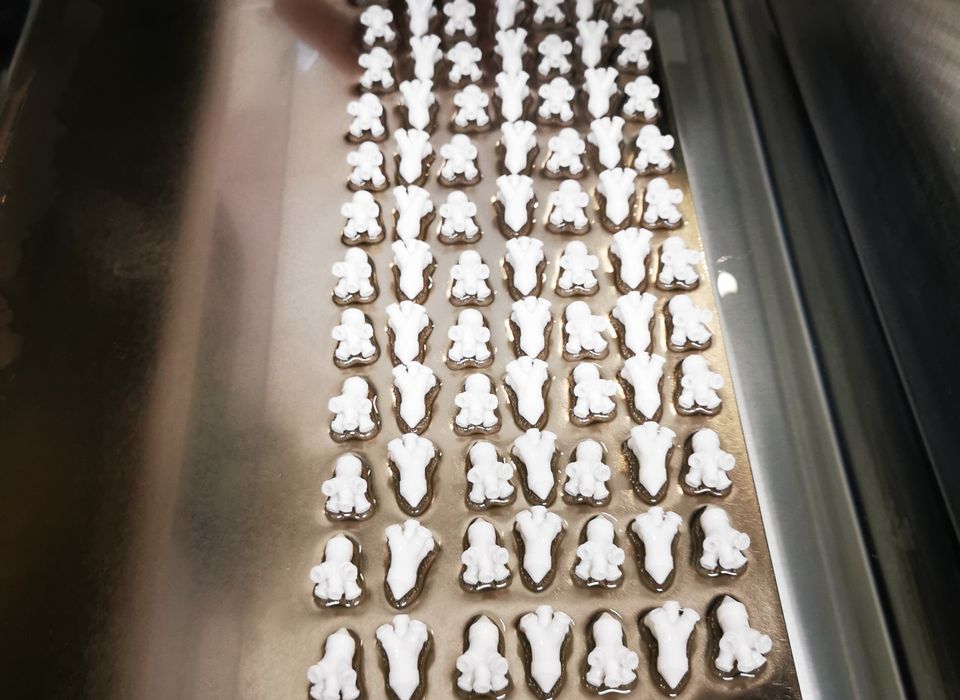
There’s another benefit XJET didn’t mention: manual labor can make mistakes, and results can be inconsistent. With a smart cleaning system, companies can be more-or-less guaranteed to produce consistently cleaned parts in predictable time periods.
That is most definitely a requirement for production use, as it might materially change the economics of using an XJET system for production.
Production systems are highly tuned to ensure the lowest possible cost to manufacture individual parts. Those costs include not only the equipment, but also the materials, facility, administrative costs, and of course, manual labor.
Labor is typically one of the major cost components, so automating it in this way could significantly change the financial equation. The SMART station might enable XJET to sell more equipment to manufacturers, and in particular, sell equipment in batches for larger scale manufacturing operations.
Producing a post-processing station of this type is certainly not as complex as the 3D printer itself, but it could have a big impact on XJET and its customers.
Via XJET