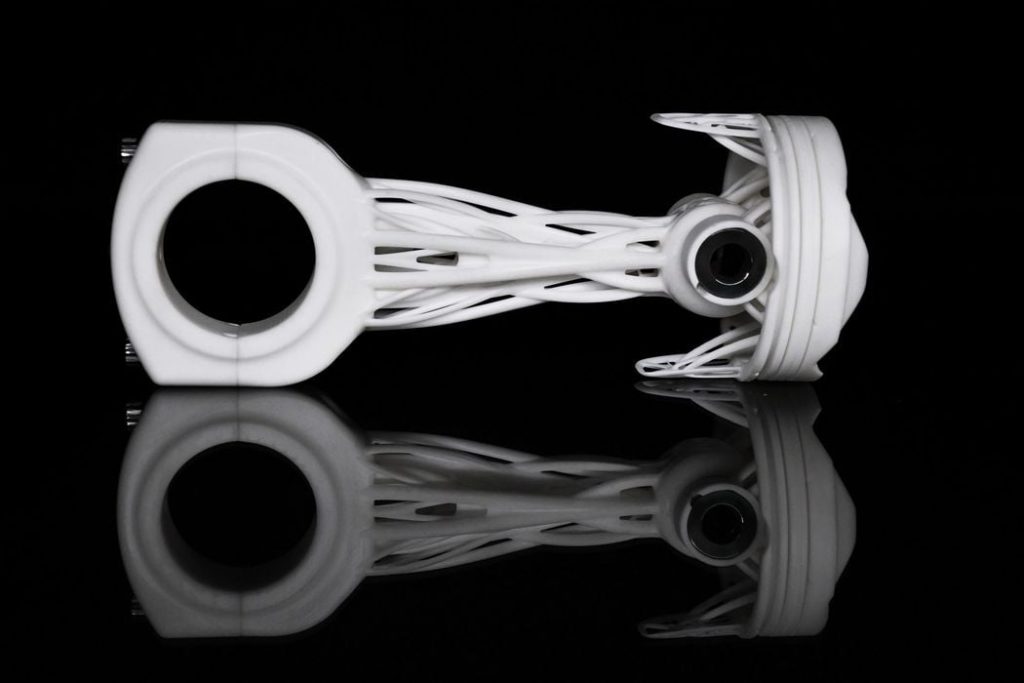
An automotive company has used XJET’s NPJ technology to produce a high performance engine piston made entirely from ceramic material.
XJET’s Carmel system has been on the market for several years, and is capable of 3D printing precision objects in ceramic materials, such as zirconia and alumina. They also produce a metal version of the Carmel that can 3D print stainless steel.
Up to now most of the ceramic applications made with XJET’s ceramic technology have been small medical and dental applications, along with mechanical components. But now they appear to have broken through a conceptual barrier with a new application: high performance engine parts. It’s one thing to 3D print a small but precise medical tool, but quite another to make a part that is at the core of a high performance engine.
Ceramic material could be ideal for this environment, which requires extreme rigidity, thermal and corrosive resistance, thermal dimensional stability and wear resistance.
That apparently was the thinking of XJET’s client, Spyros Panopoulous Automotive (SPA) of Greece. This company produces high end components for a variety of industries, including automotive, typically using advanced manufacturing techniques including additive manufacturing processes. Here’s a fuel cell part they produced, for example:
Their most recent project is the Chaos Ultracar, an experimental vehicle apparently vying to hit speeds of up to 500kph (310mph), with a 0-100kph acceleration time of only 1.55 seconds. I’d say that is pretty fast.
The key to the Chaos Ultramar’s speed is its engine, which delivers a ridiculous 3,065hp, and spins at a mind-boggling 12,200 RPM. It’s clear the inside of this engine is a very extreme environment.
The pistons in this engine must move at speeds unheard of in typical automobile engines, and thus require meeting extremely high performance standards, suggesting ceramics could be appropriate.
SPA chief Spyros Panapoulos explained:
“Ceramic offers many advantages compared to other materials. Harder and stiffer than steel, more resistant to heat and corrosion than metals or polymers and weighing significantly less than most metals and alloys. XJet’s alumina parts will withstand the high temperatures expected to develop within the combustion chamber as well as on the fast-moving parts.”
SPA apparently used a generative design approach to develop the 3D model for their “Anadiaplasi” piston. This technique involves specifying the expected forces and conditions on the part, and then lets software “generate” an optimal 3D model that uses material only to service those forces and requirements. The result is a part that requires minimal material and is as lightweight as possible.
It turns out that a majority of the remainder of the Chaos Ultracar is also 3D printed, no doubt using similar generative and other advanced design concepts.
This application demonstrates the use of 3D printed ceramic parts for extreme mechanical and thermal environments, and I suspect that XJET will reach out to many potential clients to show the successful demonstration made by SPA to persuade them to consider using ceramic in their products.