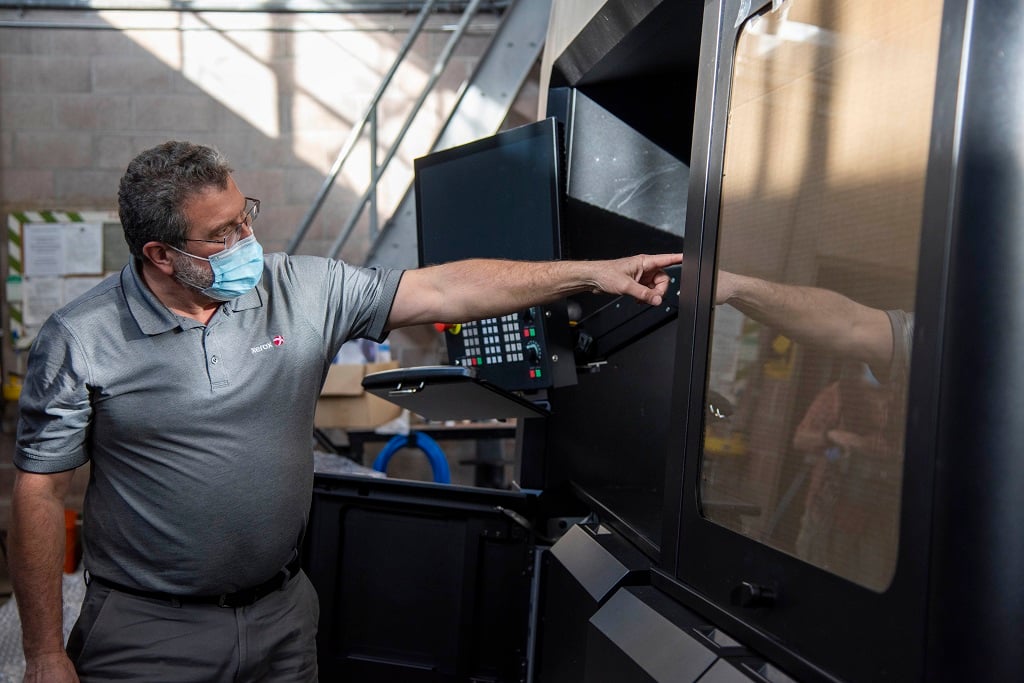
The first Xerox metal 3D printer installation is more than a customer sale: it’s the start of a collaboration with the Naval Postgraduate School.
While Xerox slyly slid information into its 2020 financial results that it had installed its first metal 3D printer, no other information seemed to be publicly available. Last week we took a look at what Xerox is doing with its metal 3D printing and business strategies.
Xerox Innovation
In its FY2020 financials, the company also noted that it would be establishing its Software, Financing, and Innovation segments as standalone businesses. On February 1, organizational changes were set into motion to further those goals, with 3D printing among the Innovation focuses.
This announcement noted:
“Naresh Shanker, senior vice president and chief technology officer, will lead the PARC Innovation business. Xerox has made progress advancing new technology in recent years with products including 3D liquid metal and industrial IoT products, cleantech technology, signing clients and generating strong commercial interest. PARC will include the scientists and engineers located in Palo Alto, Calif.; Webster, N.Y.; Cary, N.C., and Toronto to create an innovation business that drives the commercialization of Xerox’s developing disruptive technology.”
The Palo Alto Research Centre (PARC) is the Xerox home base for its metal 3D printing, so PARC Innovation will be the business to follow.
Xerox ElemX 3D Printer
Today, though, we’re seeing more details emerge specifically regarding metal 3D printing at Xerox.
The ElemX 3D printer is an intriguing piece of technology using what they call “3D liquid metal printing.” Two years ago, Xerox acquired Vader Systems, which had developed a 3D printing process using commodity welding wire. That has now evolved into the ElemX, which Xerox says “uses cost-effective aluminum wire to fabricate end-use parts that can withstand the rigors of operational demands.”
Focus is on 3D printing metal parts on-demand, shortening and tightening up supply chains. The company offers a (marketing-y, but interesting) look at the system:
Xerox x NPS
And now the first ElemX is out in the world — and we finally know where and why. Today’s press release explains:
“Xerox and the Naval Postgraduate School (NPS) announced today a strategic collaboration focused on advancing additive manufacturing research, specifically 3D printing, which has the potential to dramatically transform the way the military supplies its forward-deployed forces.
As part of a Collaborative Research and Development Agreement (CRADA), NPS was the first to receive an installation of the Xerox ElemX Liquid Metal Printer on the university campus in December. The Xerox solution will provide NPS faculty and students with hands-on exploration of new ways the technology can deliver on-demand 3D printing of metal parts and equipment.”
For its part, NPS “provides defense-focused graduate education, including classified studies and interdisciplinary research, to advance the operational effectiveness, technological leadership and warfighting advantage of the Naval service.”
Tidily, that is: the first installation and collaboration centering around the ElemX is military.
The military has long had an interest in additive manufacturing. Many branches — Army, Navy, Marines — of US armed forces have invested heavily in these technologies for R&D. Among the key benefits of 3D printing to leverage is the decentralization of production. That is: supply chain solutions. A 3D printer on a ship can quickly make qualified spare parts without having to go back to port. In-field deployments of 3D printers can gain soldiers quick access to necessary supplies. And, of course, there’s the ongoing fight to be first in developing advanced weaponry using the latest technological advances.
“The military supply chain is among the most complex in the world, and NPS understands first-hand the challenges manufacturers must address,” said Xerox CTO Shanker. “This collaboration will aid NPS in pushing adoption of 3D printing throughout the U.S. Navy, and will provide Xerox valuable information to help deliver supply chain flexibility and resiliency to future customers.”
The NPS ElemX installation will see use for faculty and students “conduct thesis research to develop new capabilities for the Navy and Marine Corps.”
NPS President retired Vice Adm. Ann Rondeau explains:
“As the Department of the Navy’s applied research university, NPS combines student operational experience with education and research to deliver innovative capabilities and develop innovative leaders with the knowhow to use them. This collaborative research effort with Xerox and the use of their 3D printing innovations is a great example of how NPS uniquely prepares our military students to examine novel approaches to create, make, prototype and manufacture capability wherever they are.
From the age of sail to the nuclear era, sailors have been fixing things at sea so they can complete the mission. This partnership is about the strategic ability of the Navy to have sailors on ships with the capability through creativity and technology to advance their operations at sea. Through collaboration, NPS and Xerox are helping build a Navy for the 21st Century.”
This collaboration is strategically clever for both Xerox and NPS. Xerox gains access to a real-world installation that can provide real-time feedback on their system’s performance. This, as Tali Rosman, Xerox Vice President and General Manager, 3D Printing, noted, will provide the company “actionable data to continuously improve the ElemX.”
And NPS will be bringing additive manufacturing a step further in national defense. Vice President of the NPS Alumni Association and Foundation retired U.S. Marine Corps Col. Todd Lyons said:
“The NPS Alumni Association and Foundation supported bringing the ElemX liquid metal printer to NPS because it will enable soldiers, sailors, airmen, and marines to solve their problems where they are, when problems occur. By providing the right digital tools and the liquid metal printer, all of a sudden we’ve helped transform not just the supply chain, but how the Department of Defense (DoD) thinks operationally about supplying war.
This is one way to bend the cost curve so that the DoD is not spending a thousand dollars for every dollar that a peer competitor spends.”