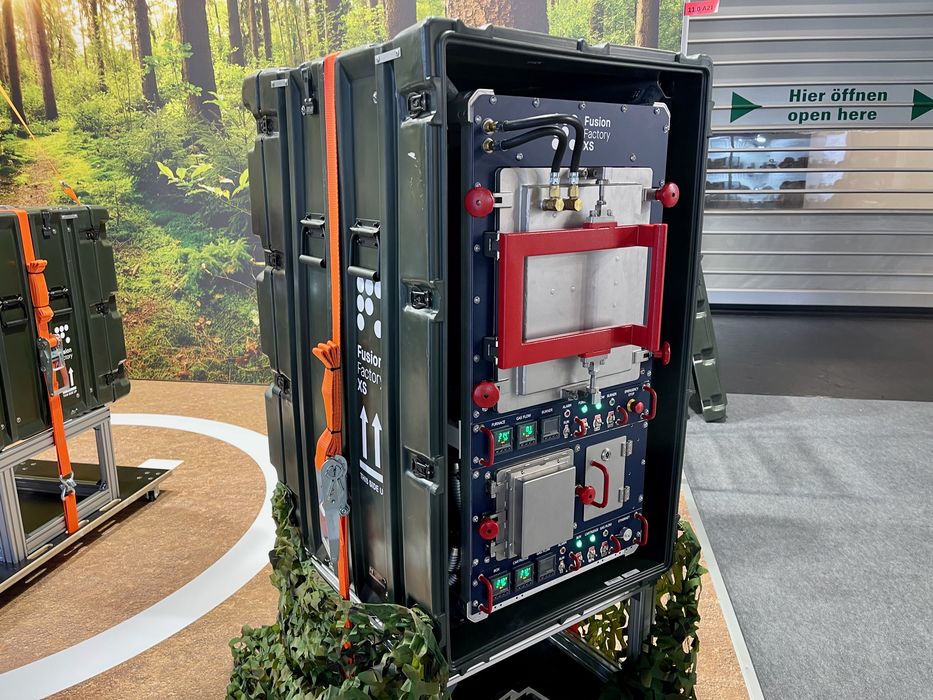
Xerion’s Fusion Factory XS is one of the most interesting professional 3D printers we’ve yet seen.
Xerion is a Berlin-based company that launched 25 years ago producing electric furnaces for industry. Much later they branched into the additive manufacturing world, and today offer several different devices. Their equipment uses FFF processes to produce metal or ceramic objects, and they are able to handle the entire workflow.
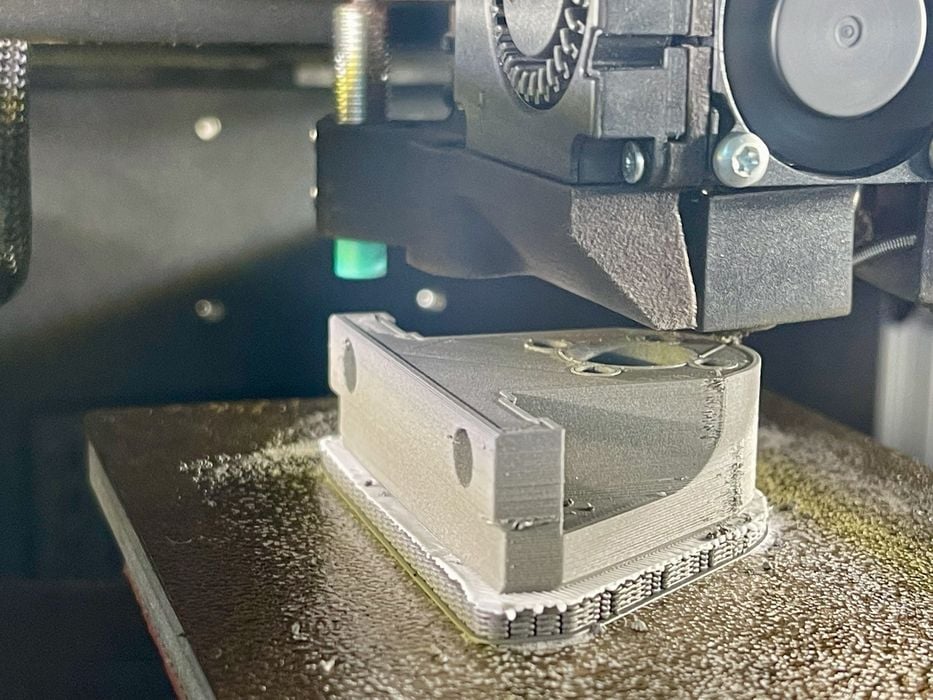
Let me explain: in a normal FFF situation you print a polymer object and you’re done. But with metal (or ceramic) FFF 3D printing there are post processing steps to do. Metal 3D printer filament is a mix of a polymer binder and fine metal (or ceramic) particles. The printed objects must first undergo debinding, where the polymer is removed, typically through a thermal or chemical process. Then, the “brown” part undergoes sintering at a higher temperature to finalize the metal part.
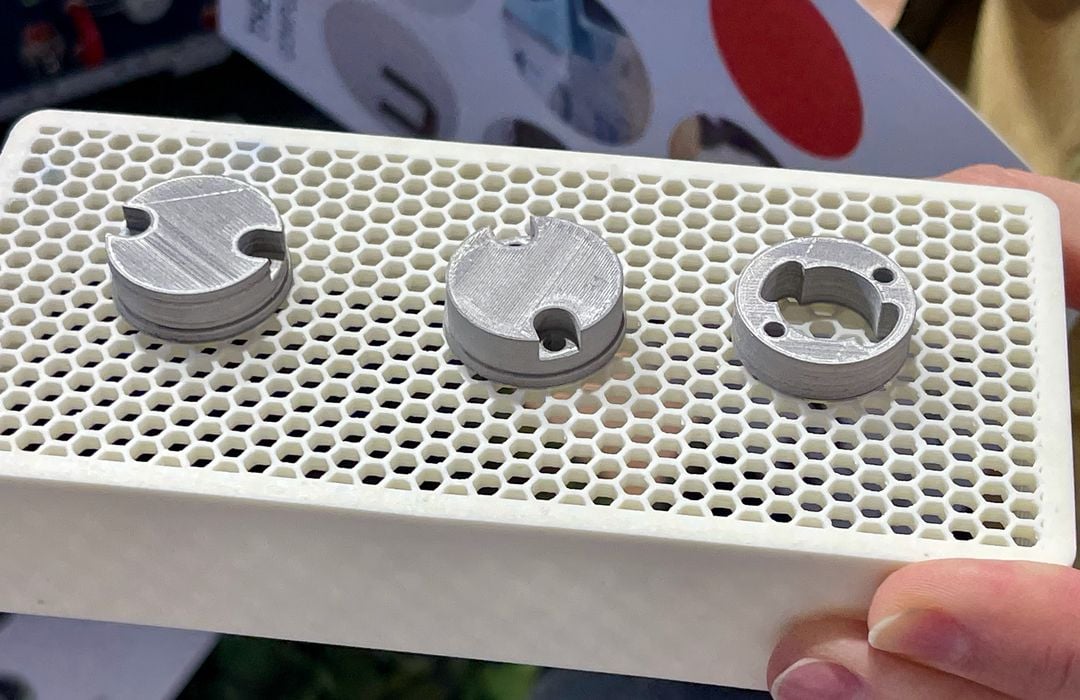
Because of this need, FFF metal 3D printing requires at least two pieces of hardware: a printer and a furnace for debinding and sintering. That’s the speciality focus for Xerion, providing integrated systems that perform these functions in a smooth operation.
Recently we were able to see one of their latest devices the Fusion Factory XS. This is indeed the pair of equipment described above, but it’s built into a modular and portable package that also includes a chiller.
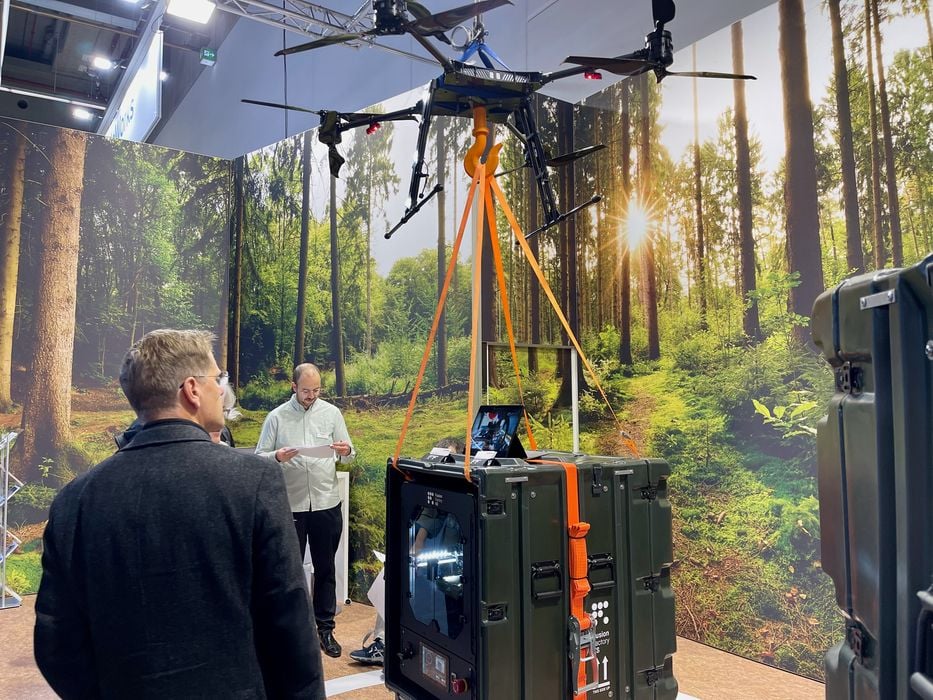
How portable? Well, the drone system shown here isn’t quite real, as the weight exceeds payload capacity. Nevertheless, the components of the XS system are neatly packaged into standard 19” Pelican cases for transport.
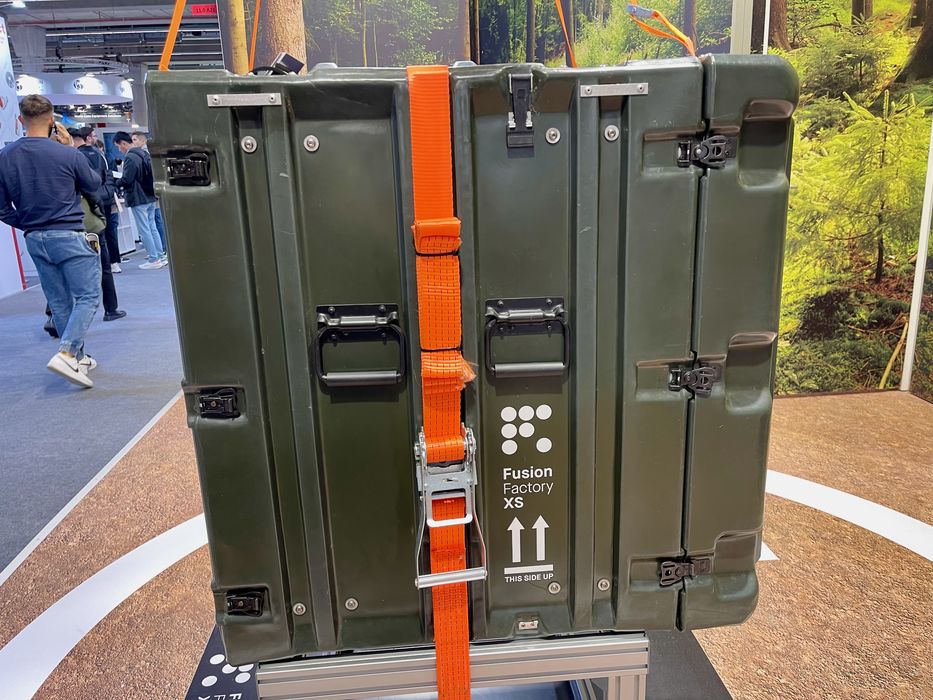
The build volume isn’t huge at only 100 x 200 x 100 mm, but the advantage here is portability, not volume.
While the XS can be used in a laboratory for experiments, it’s also designed for outdoor use: the printer and other components remain inside the cases while printing.
The use case would typically be a military situation where the XS can be quickly shipped and set up. Once ready, it is able to print production metal spare parts on demand right in the field. I should point out that the equipment does require a generator to operate.
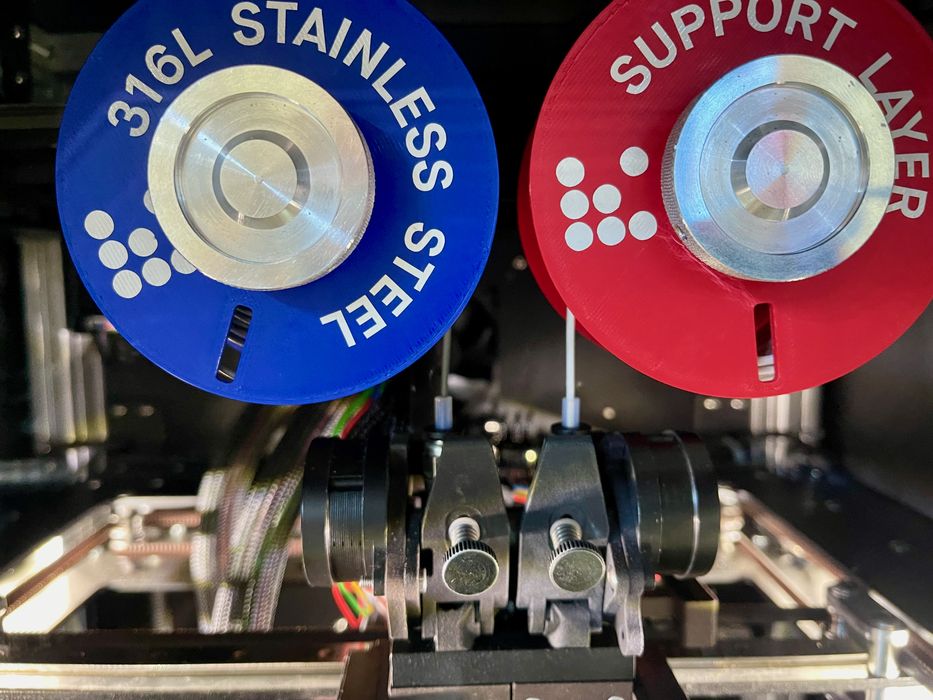
The material used by the XS is BASF’s Ultrafuse metal filament, but I suspect that other similar filaments can be used. Note that it is possible to have support structures using a different material, making the XS able to print complex metal parts in the field.
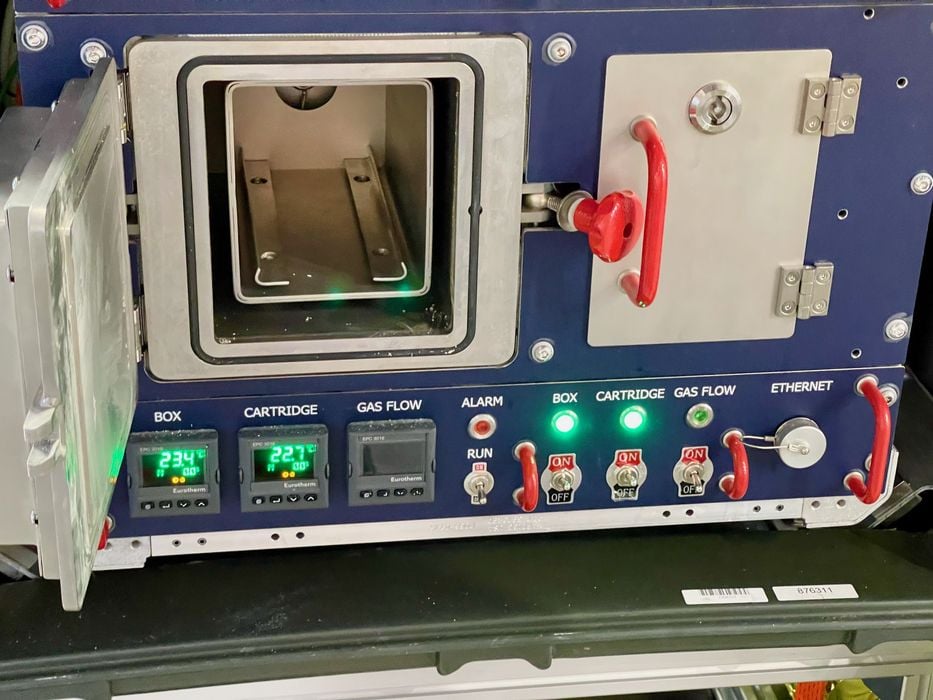
The post processing equipment is easily able to process green prints as they are equipped with thermal profiles that can take the object through the entire workflow with ease.
The XS system is yet another example of 3D print technology being adapted for use by military operators. Until recently it really wasn’t possible to produce end-use parts in field locations due to the lack of metal capabilities. Now it seems that Xerion has broken through that barrier and developed a highly useful and portable metal spare parts system.
Via Xerion