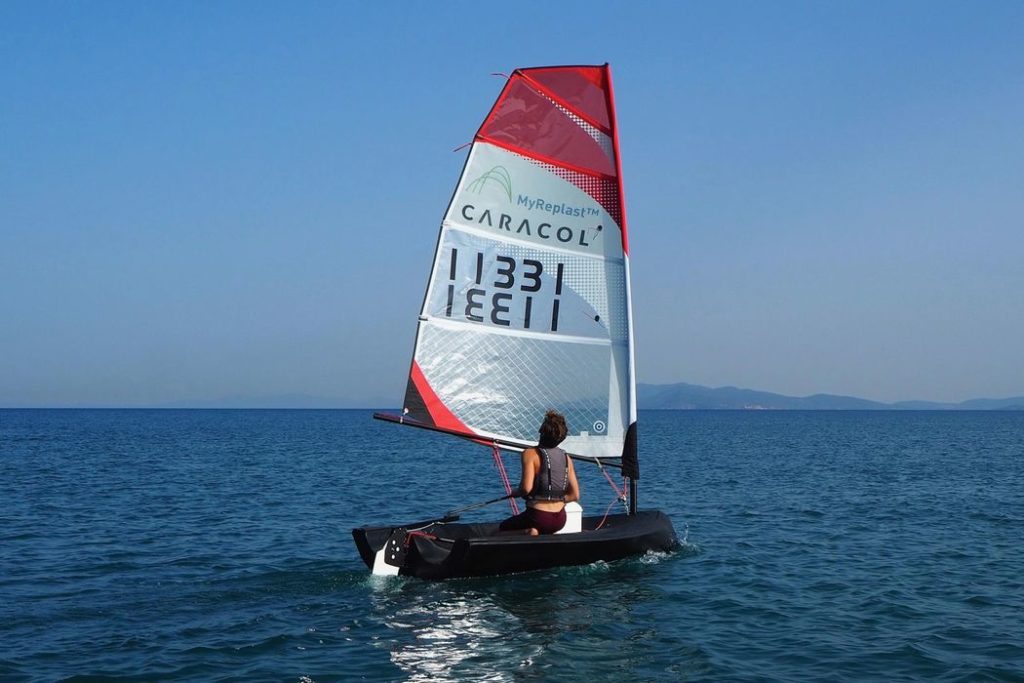
Two Italian companies have partnered to produce the world’s first 3D printed sailboat.
The project was undertaken by a partnership between Caracol and NextChem, who produced the “Beluga” a sailboat with a 3D printed hull.
Caracol is a 3D print service – and a 3D printer manufacturer. While they offer the usual FDM and SLA services using conventional 3D printing gear, they also produce their own system.
It’s a robotic extrusion system, with a six-axis reach that allows the machine to 3D print any required geometry.
In this case, the geometry was a sailboat hull. Now, this isn’t exactly the largest sailboat by any means, but it is a fully functional sailboat hull that does not leak.
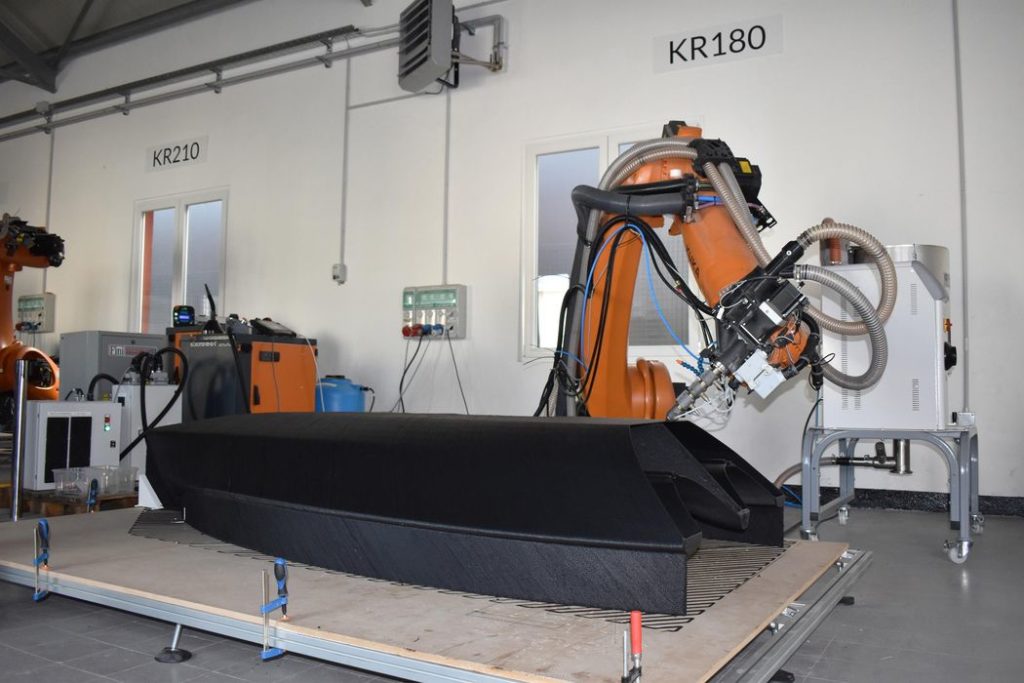
The Beluga’s hull was 3D printed in one piece using Caracol’s proprietary robotic system, and the material used was actually recycled.
They partnered with NextChem, a business focused on the production of “green” plastic material for industry. For this project, they provided their MyPlast recycled material.
The Beluga was shown recently at Milan’s Design Week event.
Why do this at all? NextChem explains:
“Caracol works with its proprietary robotic Additive Manufacturing system that can be used to improve the efficiency of various production methods while also providing a solution that is more respectful towards the environment. Traditional methods to produce sailing boats usually entail methods that require molds and use materials that are hard to recycle like fiberglass. For this reason, Caracol has employed its proprietary robotic Additive Manufacturing system to produce the hull of the sailing boat in a single piece.”
The notion of 3D printing boats would seem absurd at first. Boats are massively larger than most 3D printers, and 3D prints typically are not at all waterproof.
But this project does bring up several important points. Traditional boat building does use non-recyclable materials, and that will increasingly be viewed negatively as we slide into the climate emergency.
Boats are, as NextChem explained, typically made with molds on which fiberglass is laid and cured. That works relatively efficiently, but doesn’t open the possibility of custom designs. Mold processes are for mass production, not for customization.
Meanwhile, a 3D printed boat production facility could produce hulls of any size and dimensions on request, one after another.
However, there is the matter of software. This is a case where the hardware is well advanced compared to the software required for custom boat production. I can imagine such software using a series of templates with a number of parametric elements that can adapt as the buyer specifies preferences. But as far as I know, no such software exists.
At least, not yet.