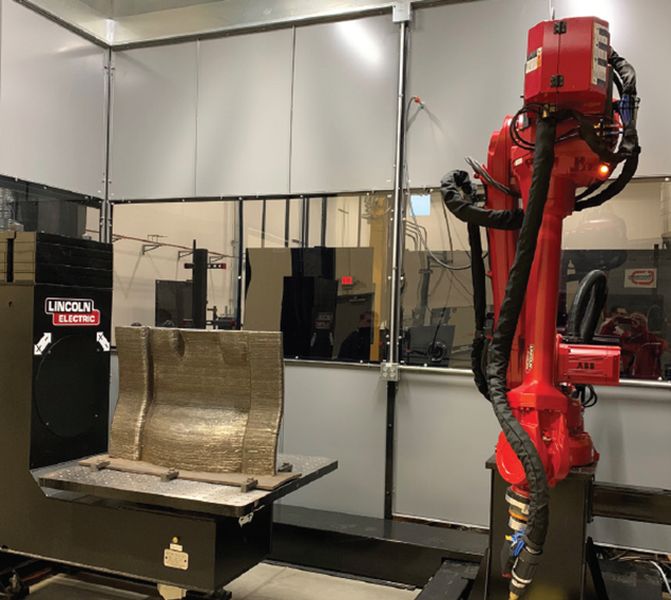
Wire Arc Additive Manufacturing Machinery [Source: Lincoln Electric]
Charles R. Goulding and Joseph Castine look at how wire arc additive manufacturing might affect several heavy industries.
Currently in Industry and manufacturing there are some significant limitations that affect both the quality and turnaround for metal parts.
Even though automated processes and lean manufacturing have increased quality and efficiency, there are still some limitations with parts for tooling use. Emerging additive manufacturing technologies have aided in overcoming some of these limitations. However, recent breakthroughs in wire arc additive manufacturing (WAAM) may provide several metal part manufacturing industries with viable alternatives to traditional tooling parts.
WAAM is an emerging technology that combines gas / metal arc welding with robotic automation motion systems. This involves the use of GMAW torches which melt layers of wire on a build platform while moving the torch using a multi-axis positional robotic system. This allows the production of fully-formed metal single parts using common welding materials. Using these new technologies to develop the molds for machine tooling, production time can potentially be cut down from months to only weeks.
Aerospace
Within the aerospace industry one of the main points of focus is the weight reduction of solid metal components. Over the years lighter composite materials have been more prevalent in this industry for this reason, however, the tooling for these composite materials can take months to produce. Production delays for major airline companies can result in tens of billions of lost revenues. According to Deloitte, global passenger aircraft traffic had decreased 70% in November 2020 compared to November 2019 as a result of the COVID-19 pandemic.
With the release of several highly-effective COVID-19 vaccines, travel is expected to rebound 56% over 2020’s performance, however, this could still be 38% below pre-pandemic levels. These figures represent potentially hundreds of billions of dollars in lost revenue in the commercial airline industry. Boeing had already shown aircraft supply chain slowdowns, and surely the global pandemic could not have improved these supply chains. Perhaps by employing WAAM techniques, portions of the supply chain for aircraft companies could be improved by drastically cutting down the tooling times.
Automotive
Although the automotive industry has seen some significant improvement in product development cycle times, companies still face challenges in product testing and supply chains. The research and development for these products is in many cases the reason for these longer go-to-market timelines. 3D print service companies with a large reach in the automotive industry like Jabil have growing 3D printing capabilities and have helped several of their clients to implement AM techniques into their processes. These additive manufacturing techniques are capable of reducing costs and production risks. Jabil has a global network of additive manufacturing facilities; if companies like Jabil embraced WAAM, that technology could permeate more deeply into the automotive industry.
Within the automotive industry the electric vehicle market continues to grow as EVs become more popular. Magna International, a Canadian parts manufacturer has become the go-to supplier for many EV startups. The company has been known to use 3D scanning techniques to more accurately integrate parts into Magna-equipped vehicles. If Magna intends to continue down their path of innovation and implement more 3D additive manufacturing techniques, the addition of WAAM into its production systems could prove beneficial.
Heavy Equipment
According to Global Market Insights Report the earth-moving and road-building machinery markets are forecasted to grow at a CAGR of 4% in the construction machinery industry by 2024. Agricultural equipment makers will experience a similar growth with a CAGR of 5% over the next four years. There are also pressures to keep up with new designs to meet global emissions standards which increase variability and R&D production costs. Companies like Caterpillar have already begun to invest in 3D printing components for heavy equipment to meet these design standards and R&D costs. With the implementation of these additive manufacturing techniques, it is foreseeable that future ventures into wire arc additive manufacturing could further improve their innovative capabilities.
Oil & Gas
During the COVID-19 pandemic some of the largest oil and gas companies, including Chesapeake, have been forced to declare bankruptcy. Several of the legacy manufacturing equipment companies that supply that industry have also gone out of business in parallel situations. This presents a unique opportunity for WAAM technology, which could be used to develop replacement parts for these legacy machines. Baker Hughes has already begun using some metal additive manufacturing techniques with remarkable success, showing the possibilities for WAAM in this troubled industry.
Research and Development Tax Credit
Companies that engage in additive manufacturing and similar techniques may be eligible to take the Federal Research and Development (R&D) Tax Credit.
Enacted in 1981, the now permanent Federal Research and Development (R&D) Tax Credit allows a credit that typically ranges from 4%-7% of eligible spending for new and improved products and processes. Qualified research must meet the following four criteria:
- Must be technological in nature
- Must be a component of the taxpayer’s business
- Must represent R&D in the experimental sense and generally includes all such costs related to the development or improvement of a product or process
- Must eliminate uncertainty through a process of experimentation that considers one or more alternatives
Eligible costs include US employee wages, cost of supplies consumed in the R&D process, cost of pre-production testing, US contract research expenses, and certain costs associated with developing a patent.
On December 18, 2015, President Obama signed the PATH Act, making the R&D Tax Credit permanent. Beginning in 2016, the R&D credit has been used to offset Alternative Minimum Tax (AMT) for companies with revenue below $50MM and, startup businesses can obtain up to $250,000 per year in payroll tax cash rebates.
Conclusion
Due to current limitations affecting the quality and turnaround of metal parts and tooling molds, WAAM has a unique opportunity for expansion and widespread adoption. With the efficiency and effectiveness of these techniques, it is likely we see a large spike in the adoption of these practices to reduce production times.