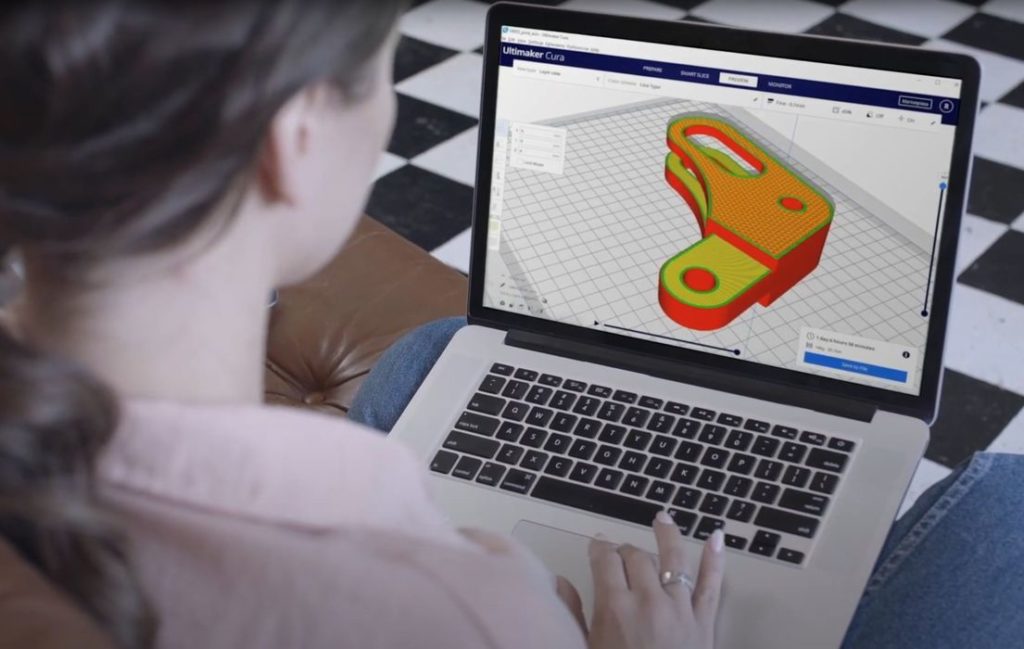
I had a chat with Teton Simulation’s Doug Kenik to find out where SmartSlice is headed.
SmartSlice is a unique product in the 3D print space, and it’s not a 3D printer: it’s a slicing software add-on. The goal of SmartSlice is to do exactly that: slice the 3D model in the most intelligent way possible. This enables operators to achieve far better results with 3D printing.
SmartSlice does this by accepting a slicing goal from the operator, such as to increase the strength in a particular area of the print.
Some 3D print slicing software allows you to define specific zones where you might change the print parameters, say to increase the degree of infill, for example. Some operators use that technique to strengthen their parts.
However, imagine if there was software that could automatically figure out all the zones required and instantly generate whatever style of extrusion is required to meet the design goal? That’s what SmartSlice does.
This video shows a bit more about how it works:
The manual process required to appropriately optimize a part can take many iterations, but using SmartSlice it’s possible to short circuit that work significantly. This greatly reduces part development time, and that should save money on the project.
So far Teton Simulation has partnerships allowing use of SmartSlice within Ultimaker Cura, GrabCAD and BCN3D Stratos.
Kenik explained that there are certain types of 3D printer manufacturers very interested in SmartSlice:
“We are continuing to expand our relationships with 3D printer manufacturers. There is a huge value proposition for huge 3D prints; the number of iterations is large, material used is enormous, etc.”
This makes a great deal of sense. If it saves cash to reduce part development iterations on smaller parts, imagine the savings for those operating large-format 3D printers, where each print takes days or even weeks, and uses several kilos of material.
He continued:
“The goal is to reduce print time or the number of iterations, and we attempt to get to one or two iterations. Most companies either perform an iteration or simply print the part completely solid. We want to increase throughput on machines.”
Indeed, 3D printing an object with 100% infill would certainly increase its strength to the maximum, but that can take much more material, particularly on large-format 3D prints, and also take considerable print time. SmartSlice should allow the suitable strengths to be found with far less material and printing.
I asked Kenik about industrial use of SmartSlice, and regarding use in the aerospace industry, he said:
“We’ve been demoing GrabCAD print, it’s a huge thing for them. They have a large lack of confidence in 3D printed aerospace parts. While parameters dictate how the part performs, even printing a part completely solid doesn’t work due to anisotropy. It’s all guessing.”
He added:
“Customers should be comfortable and confident in their parts, and the software has been lacking.”
But what about the 3D printer manufacturers? How does SmartSlice figure into their plans? Kenik explained:
“Most have an ecosystem where customers are so successful they don’t want to leave. It comes down to the 3D printer manufacturer’s strategy. They trust the OEM so much they keep using it. We think the leaders will be using our SmartSlice system.”
Kenik believes several slicers are gradually migrating to more professional modes for industrial production at scale, and that’s where SmartSlice could fit right in.
He said they do have an education problem, however, as companies are initially skeptical that a software company could save them even more after already saving by simply switching to AM techniques. However, he said, “they always get it.”
What’s next for Teton Simulation and SmartSlice? Kenik said:
“There’s a lot coming down the pipe. Many companies are getting on the train.”
It may be that in the near future, most 3D print slicing system could be a lot smarter.
Via Teton Simulation