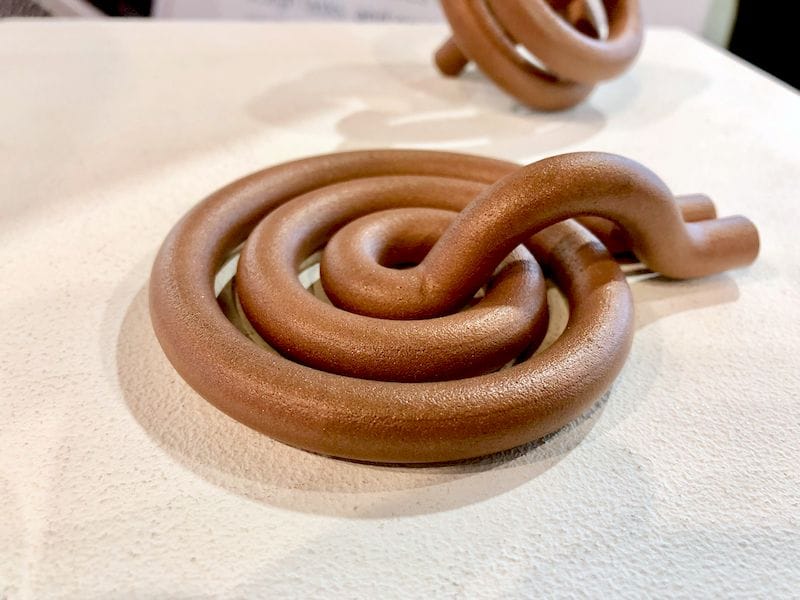
Copper is a relatively rare material in additive manufacturing operations, but that could change in the next few years.
We’re all familiar with copper, that golden-colored material seen in wiring and electrical contacts. For such a well-known material, you might think it would be more frequently used in 3D printing.
But there’s many challenges to 3D print copper.
First, it’s a metal, and that alone puts it in the more difficult class of 3D printable materials automatically. Metals can be 3D printed, of course, but they require expensive and complex equipment, and sometimes even require precisely controlled room environments. They also require considerable post-processing and even squads of engineers to tune the print jobs so that the objects don’t unnaturally warp when exposed to the tremendous heat of 3D printing.
And then there’s copper.
Most metal 3D printing setups, particularly those used for manufacturing, use the powder bed fusion (PBF) process. In this process a flat bed of fine metal powder is selectively fused by an energy source, typically a very powerful laser. Subsequent layers of powder are similarly fused and gradually a fully 3D object can be built.
That process works quite well for many popular 3D printable metals, such as aluminum, steel, nickel or titanium. But you very rarely see anyone mention copper.
The popular metals have found places in several industries, including most notably aerospace, where the combination of already-high-priced parts and the ability to create “impossible” parts was irresistible: aerospace companies could built incredibly lightweight parts that proved highly beneficial — and profitable.
Why hasn’t something similar happened with copper material?
Copper 3D Printing Challenges
One issue is that copper turns out to be incredibly difficult to 3D print using the PBF process. Copper has two challenging properties: it’s highly reflective and it transmits heat and electricity very well.
The heat transfer causes difficulties in the build chamber, which must be maintained at very precise temperatures to ensure successful metal 3D prints. It’s possible for heat from the laser meltpool to “leak” into neighboring areas, and this could result in use of lower power levels and thus far slower prints.
The reflectivity could be another issue. By injecting tremendous amounts of energy into the build chamber with powerful lasers, you want as much of that energy to be absorbed by the material as possible. That’s why several thermoplastic SLS PBF systems use dark nylon powder instead of white powder: black absorbs more light.
If that energy isn’t absorbed by the copper material, where does it go? Well, it splashes around inside the build chamber itself, generally heating up everything it can reach. This not only fouls up the precision heating, but also can damage internal components, like lenses, belts, electronics or more.
In other words, you really have to re-engineer the innards of your metal PBF 3D printer to accommodate copper material. Some 3D printers are beginning to do this, and we may see more in the future.
Copper 3D Printing
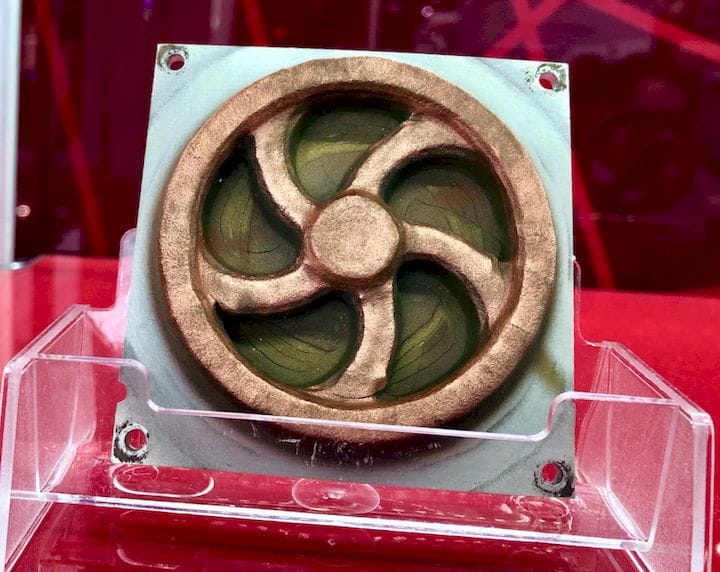
There are alternative 3D printing processes that can 3D print copper. Two that come to mind are Fabrisonic and SPEE3D.
Fabrisonic uses a lamination approach in which sheets of virtually any kind of metal can be fused together using ultrasonic vibrations.
SPEE3D uses a (literally) supersonic extruder to blast fine metal powder at a target. The kinetic energy from the particle motion causes them to fuse together. By moving the toolhead around, you can quickly build metal objects, even with copper.
However, neither of these approaches is easily able to produce the complex geometries desired by many industries, and so copper 3D printing is rarely seen.
Newer work in copper 3D printing is emerging from companies like Markforged, Xact Metal and Additive Drives.
It seems there are two areas of considerable interest for future copper 3D printing: antennae and heat exchangers.
Antennae are used in all mobile devices and many remote installations for communication. But for certain types of antennae design an omni-directional capability is required. This means the design could include a large number of mini-antennae oriented in different directions.
If anything sounds like a complex geometry suited to 3D printing approaches, that would be one.
Another would be heat exchangers. These are devices that usually carry a fluid and transfer heat from one zone to another, and as copper is a fantastic carrier of heat, it is the ideal material. An optimum heat exchange would involve the maximum amount of surface area exposed to the fluid, and as you might suspect, that’s also a very complex geometry.
It can be even more complex, however, as some heat exchangers must be installed in cramped spaces, leading to more design challenges.
Again, an ideal suspect for future copper 3D printing.
This is the market that lies ahead for those 3D printer manufacturers that are able to adapt their equipment (or invent new equipment) for copper 3D printing.