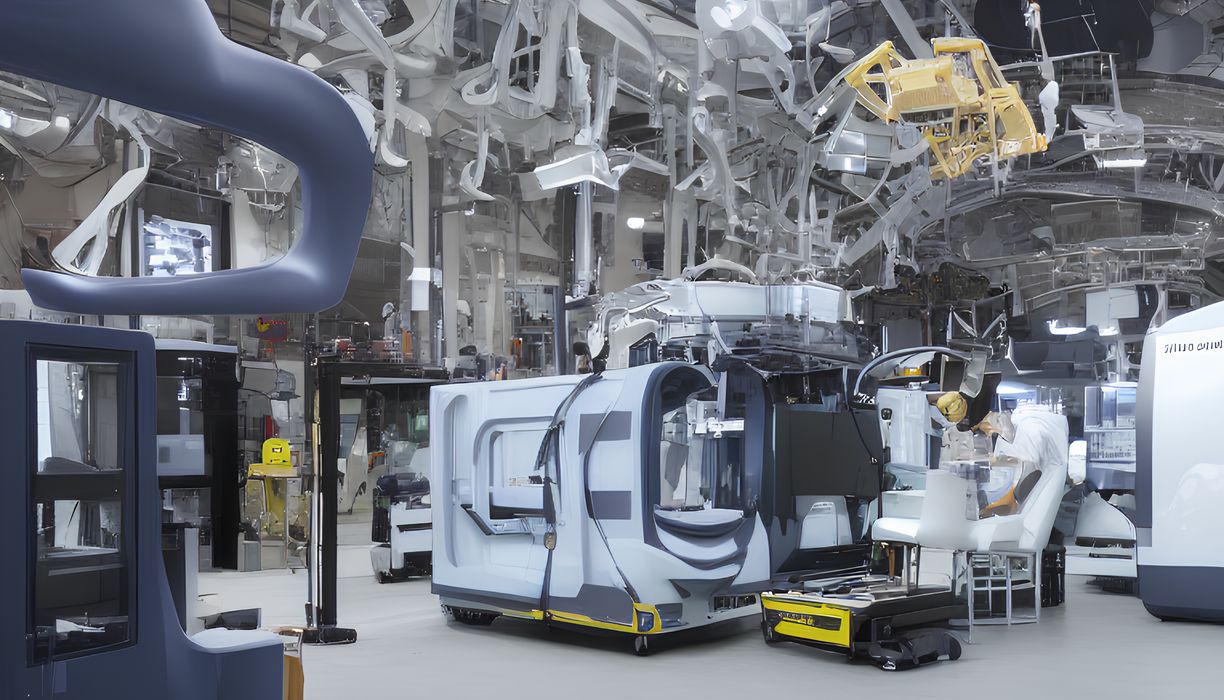
Two industries have developed extremely deep usage of 3D printing, but for entirely different reasons.
The two industries are Dental and Aerospace. Hardly a day goes by when I don’t receive at least one press release about a development in either of those domains.
This week, for example, we heard from Carbon, which has released a new sophisticated automated print preparation system for dental 3D models. We also saw a release from Structo regarding an entirely new line of MSLA 3D printers dedicated to the dental market.
The aerospace industry is much the same. Each week there are announcements about a new style of use or another milestone being reached.
Why, among all the industries on this planet, are those two industries so deep into 3D printing?
It turns out the reasons are actually quite different.
3D print technology has a number of unique capabilities that differentiate it from traditional manufacturing methods. These advantages are what attracts industry to the technology, but in different ways because each industry has unique needs.
There is one common element, however: both aerospace and dental industries are accustomed to high prices for parts. This is partly due to regulatory requirements to ensure their products are safe for the public, but both buyers and sellers expect higher pricing.
Those price levels open the door to feasible use of additive manufacturing.
In the case of dental, the key feature is personalization.
3D printing, unlike traditional manufacturing, does not require the production of identical parts. It turns out that each person’s teeth are actually different (who knew?) and so it is impossible to mass manufacture many dental tools and applications.
Enter 3D printing: because each produced part can be different simply by changing the corresponding 3D model, it’s possible to “mass produce” unique items using farms of 3D printers.
This has been done for years, particularly with aligners that must match the patient’s teeth geometry. It’s also being done for a variety of other dental applications, and I have a suspicion that this will very soon become the de facto method for most dental work.
On the other side we have aerospace.
Aerospace doesn’t really require personalization as a capability. In fact, they really need the opposite: aircraft must be identical when produced to ensure they perform identically and have the same safety measures.
Instead, aerospace focuses on the ability of 3D printing to produce parts with highly unusual geometries. Traditional manufacturing: casting, injection molding, milling, etc., all have notable constraints on the geometries that can be produced.
For example, a mold must be made so that the object can be released easily. A complex geometry could easily be created that could not come out of a mold, and that would require destruction of the mold. In order to re-use molds, which is necessary for manufacturing economy, parts must have releasable geometries.
This is not the case with additive manufacturing, because objects are built layer by layer, and there are basically no geometric constraints, aside from those derived from the specific machine involved: devices may have a minimum wall thickness, for example, as well as other minor constraints.
This capability has opened up the possibility of using parts with highly unusual designs in aerospace. Two approaches are used.
One is “lightweighting”. In this approach, parts are redesigned to minimize the amount of material to lose weight, but at the same time provide the necessary mechanical functions. Usually these highly complex designs are produced by specialized software that can generate the patterns.
Another approach is “part combination”. The simplistic geometry of historical parts required assembly into complex mechanisms. But with the ability to 3D print complex objects, we now find the aerospace industry 3D printing the entire complex object as a single part.
This provides not only a reduction in assembly costs, but also inventory management, increased reliability (fewer seams to break), and also lightweighting. The lightweighting comes from the absence of nuts and bolts that would otherwise be required to hold the simple parts together. They’re no longer needed.
The result of these approaches is a dramatic reduction in the weight of parts, and corresponding advantages to the aircraft (or rockets) overall. Flights can take place at lower costs, or more payload can be carried.
Both of these industries have seen the advantages of additive manufacturing and have gone deep into them. The advantages are quite clear, and that’s why it’s happened.
This is also why deep use has not yet emerged in many other industries. However, the key to unlocking massive industrial use is still the financial barrier: 3D prints cost too much to make.
I know there are parties working on solutions to that issue, but we haven’t seen them yet.