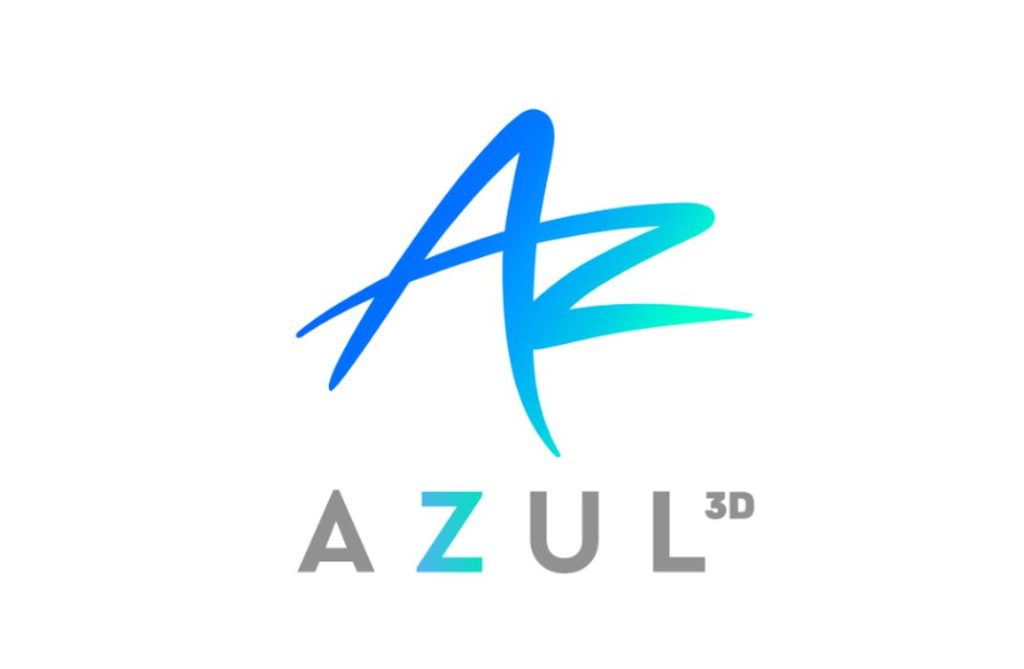
Azul 3D is one of the latest 3D print companies to appear on the scene, and we spoke to the company’s Chief Revenue Officer, Tuan Tranpham, to find out more.
Tranpham is quite familiar to Fabbaloo, as he’s had many different roles in the world of additive manufacturing over the years. These days he’s Chief Revenue Officer at the Illinois-based company, having joined them this past July.
The company launched its first 3D printer earlier this year, the LAKE. It’s a resin 3D printer that uses DLP technology, but it has a unique design that is specifically targeted at industrial users.
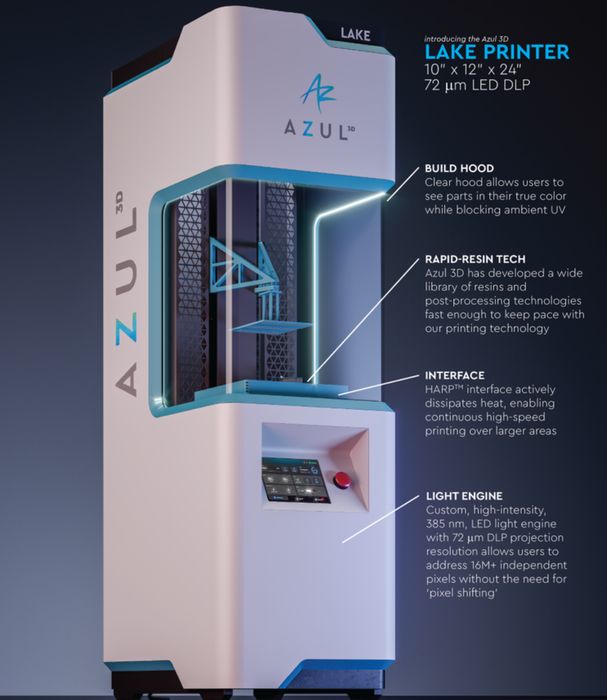
Tranpham explained that Azul3D is actually a spinoff from Northwestern University, where the founders obtained significant material expertise. Tranpham insists that the core of Azul3D is actually material science.
I asked Tranpham what is the big deal about DLP 3D printing? He explained:
“DLP is never going to be ‘production’ unless you remove the heat. This is because you eventually have to stop printing and cool down.”
Azul3D overcomes this issue by using a special cooling method:
“Nobody is using a liquid cooling interface. We use a fluorinated oil that encourages replenishment of resin. With our technology you can make tall 3D prints, for as long as you can pull up the arm.”
This is perhaps an unappreciated constraint on some DLP 3D printers: if the printer heats up over time, then tall prints might not be possible because the machine would have to cool down before reaching those heights.
The original LAKE 3D printer has a rather large build volume of 254 x 305 x 610 mm, but Tranpham said:
“We can go even higher with a ‘LAKE +’ machine.”
The machine has a resolution of 0.072mm, and a print speed of up to 300mm per hour. Tranpham explained that one of their existing LAKE printers would be able to, for example, 3D print 55,000 pickle ball paddles per year. That’s significant, and one can imagine a bank of LAKE printers producing very healthy volumes of industrial parts.
I asked about the minimum layer size for the process, and Tranpham exclaimed:
“There’s no layers — it’s continuous!”
Because of the fluid interface between the resin tank and the model material, it’s possible to 3D print without the need for repositioning the build plate. This saves an enormous amount of time during print jobs, as most other resin 3D printers require a “peel and flow” step on each layer. Meanwhile, the LAKE 3D printer just keeps printing without stopping.
Tranpham explained how this works:
“It’s like a glass aquarium. There are eight optical modules (which are plug and play), and software aligns them. In the tank at the bottom there’s a ‘lazy river’ of oil. It’s collected, filtered and chilled, and doesn’t mix with the resin. It can run for six months!”
Tranpham explained that while other companies might claim high speed printing, it’s really all about throughput for industry. By enabling continuous and non-stop 3D printing, this machine could be ideal for manufacturers.
Tranpham made sure to point out the build volume of the LAKE is very similar to Carbon’s L1 machine, suggesting that Carbon is very likely their rival in the market, which is the manufacturers of consumer products.
One other similarity with Carbon is the manner of sales: instead of selling the gear to clients, Azul3D only leases equipment. Currently, the price is about US$50K per year, including a minimum resin order. Tranpham said they want to encourage production, not prototyping.
Finally, Tranpham said the company is currently “getting ready” for a Series A investment, which would surely boost the company’s ability to both grow their sales and increase printer manufacturing capacity. They haven’t said, but I suspect they may be yet another candidate for an IPO or SPAC in future years.
Meanwhile, manufacturers might want to take a close look at Azul3D’s very interesting offerings.
Via Azul 3D