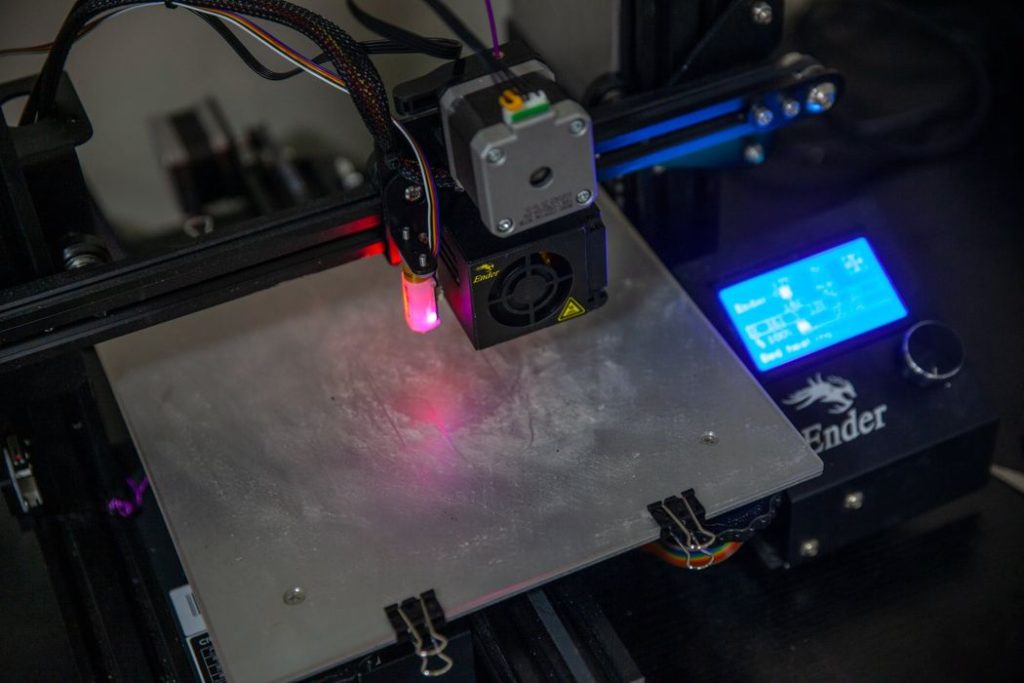
An interesting view of 3D printing from outside the industry.
Hagerty is a US-based insurance provider specializing in classic automobiles, and they also maintain a large community of auto enthusiasts. They publish a print magazine as well as a well-trafficked online site where stories are published about auto lifestyles, events and equipment..
In a recent story they wrote about 3D printing. The story “A beginner’s guide to 3D printing car parts” describes the ease in which one could potentially 3D print parts for automobiles that are hard to find.
The story is quite positive and mostly accurate, but seems a bit optimistic about how one could succeed in doing so.
The author of course relates the Star Trek replicator analogy, and writes that you can “sort of” do this.
The story recommends using low cost desktop 3D printers, and PETG material, while correctly suggesting that PLA should be avoided for all automobile applications. ABS is discussed, but ASA (UV resistant), is not.
It’s recommended that you proceed to Thingiverse, Thangs or GrabCAD to obtain 3D models to print, which is certainly doable, but there’s no mention of Printables, which is the fastest-growing 3D model repository.
For unique parts, the story recommends using Autodesk Fusion 360 to create the required designs. They write:
“Learning to design your own parts will be beneficial in the long-term, as you will not be limited to what others have created.”
That is indeed correct, but this is where I take issue with the story.
Learning Autodesk Fusion 360 is just not something you just open up and use. It takes a considerable time to gradually learn the complex interface and all the necessary tools to do anything useful. A newbie would have to sit through at least several hours of video to even get started. That’s all necessary and worthwhile, but the story doesn’t hint at the significant learning curve for 3D modeling tools, including Fusion 360.
Equally optimistic is the printing description. Every 3D printer operator with inexpensive equipment knows that:
- The probability of print failure is significant
- The possibility of the printer breaking is significant and inevitable
There’s also no mention of the possibility of 3D scanning existing parts for replication, which is enormously complex and requires significant hardware, software and experience to do properly.
Those designing parts for 3D printing know that it always takes multiple iterations to get the part correctly sized and designed. While that’s easier with a 3D printer on hand, it’s still a lot of work to do, say, ten iterations of anything.
Typical 3D printer operators spend hours building, tuning and running their desktop 3D printers. They also spend time resolving jams, cleaning debris, washing print surfaces, tightening belts, adjusting thermals, calibrating new filaments, calibrating the machine, and much more. As much as we’d like, desktop 3D printers are still not machines you can simply turn on and use. They break.
New 3D printer operators may be eager, but they have to go through a significant learning curve to really become capable. This takes weeks or months for most people.
The problem is that most of the general population is not willing to go through that ordeal, and that’s why 3D printers are not found in every home.
On the other hand, Hagerty readers are likely include the type of person that works often with parts and in all probability has a much higher chance of surviving the 3D printing learning curve.
It’s terrific that 3D printing is being encouraged here, but I fear that some may enter the space as a result of the story, only to become frustrated by the challenges and eventually abandon the tech. I don’t think that’s a good outcome.
This story is written from the point of view of folks outside the normal stream of 3D print news, and it’s an interesting glimpse into that world. There we see that at least some believe that 3D printing is simpler than it actually is.
I think this is a strong message to 3D printer manufacturers: make your machines more reliable and easier to use and you will get many more customers.
Via Hagerty (Hat tip to Pete)