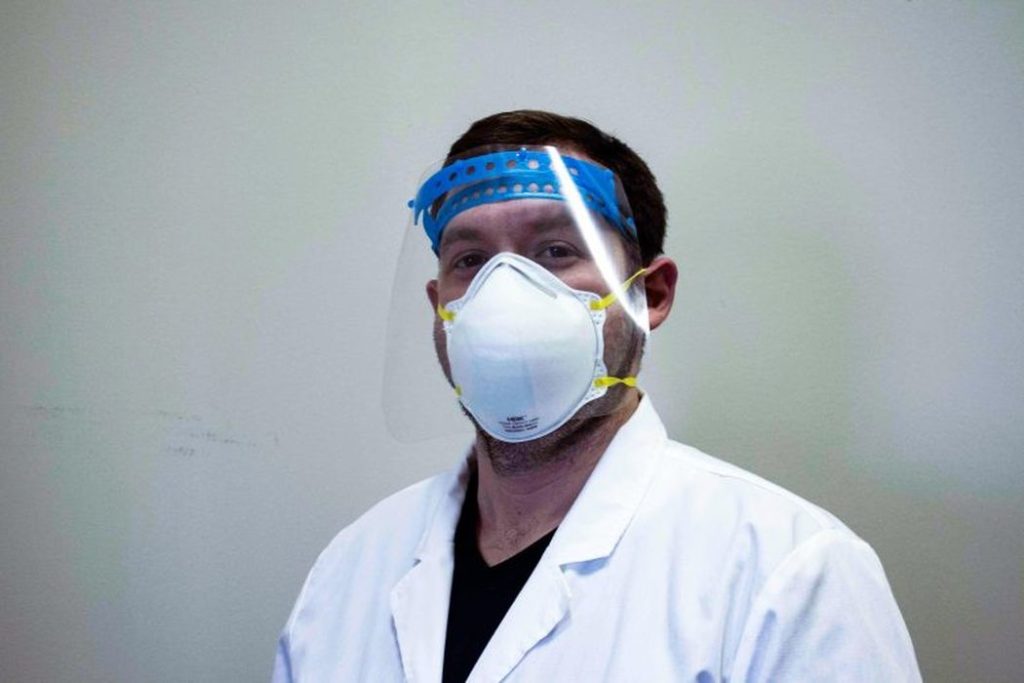
Find out why High Area Rapid Printing is worth the hype. It just might revolutionize the way goods and products are created.
In 2019, researchers at Northwestern University unveiled a new type of 3D printer capable of dramatically faster production speeds without sacrificing quality or resolution, which is a typical problem when attempting to 3D print with large equipment. Northwestern’s Mirkin Group, led by Dr. Chad Mirkin, set out to improve stereolithography printing methods to make it more likely that warehouses and manufacturers can one day transition away from creating their tools and parts with injection molds and fully embrace 3D printing. For that to happen, printers will need to be fast enough to produce parts on demand. High Area Rapid Printing (HARP) just might be the technology that makes this a reality.
What Is HARP Technology and How Does It Work?
High area rapid printing technology is a subset of additive manufacturing or 3D printing that permits continuous, high-throughput printing of large objects at rapid speeds. Compared to traditional methods of 3D printing, HARP is much faster and more efficient, capable of printing objects the size of an average adult in several hours. HARP is an improvement on older methods of stereolithography where many layers of resin are put down by a printer to create an object. Essentially, it is a process of converting liquid plastic into hardened objects.
Non-HARP 3D printers are limited by the heat they produce when running at fast speeds. Surface temperatures can top 180 degrees C, which is dangerously hot and can lead to parts cracking or deforming. 3D printers just can’t reach their top speeds without generating intense amounts of heat. HARP technology aims to alleviate this problem by working with a non-stick liquid that is similar to Teflon.
In HARP printers, the non-stick liquid circulates below the resin to reduce heat and cool the system. Light is projected through the system to rapidly harden the resin. The entire interface is non-stick, which removes the need to repeatedly cleave parts from the bottom of the print vat. This allows the printer to work at high speeds without suffering a drop in quality, even when printing large structures. Traditional 3D printers are not even capable of printing small parts at rapid speeds without facing quality issues.
The primary benefit of HARP is that it improves printing speeds up to a hundredfold, making it practical to ditch on-hand inventory in favor of on-demand printed parts and tools. Because HARP is not limited in the size of surfaces and shapes it can print, a HARP printer could potentially be used to create something as large as an airplane wing or turbine blade all the way down to a tiny medical device. Compared to established leaders in the 3D printing sector, HARP boasts 2000x throughput based on estimated 20x scale and 100x speed with more flexibility in the type of resin selected.
The technology is currently being commercialized and developed by Azul 3D, a startup company led by the researchers that was recently named a Formnext Start-up Challenge winner for 2021.
“Our technology helps manufacturers consolidate parts, create new geometries, secure a digital inventory, support localized manufacturing, and design completely customizable products. Our printers will represent a new paradigm in the industry. We will be the go-to solution for manufacturers of industrial, consumer and automotive goods,” said Azul 3D CEO Cody Peterson. “Azul 3D will fill the gap between traditional additive manufacturing (prototyping, molds & tooling, and limited production runs) and traditional mass manufacturing of plastic goods. Our technology and product portfolio fill this unmet need in today’s manufacturing ecosystem.”
How Can HARP Be Used?
At the height of the COVID-19 pandemic, the need for personal protective equipment for frontline medical workers spiked and could not be sourced quickly enough to keep up with the exploding health crisis. In this moment, the team at Azul 3D stepped up to put their printers to work cranking out masks, face shields and goggles. Azul was able to top 1,000 shields per day using a 13-foot tall HARP printer that ran 24/7. In an effort to do their part to tackle the challenge of the pandemic, Azul sped up the production of their beta printers and shipped over 10,000 shields, many of which were sent to the Navajo Nation as it suffered one of the worst COVID outbreaks in America.
“Even fleets of 3D printers were having difficulty meeting demand for face shields because the need was so enormous. But HARP is so fast and powerful that we could put a meaningful dent in that demand,” said Mirkin.
Read more at ENGINEERING.com
It has most of the same components as the pc on your desktop, however they’re so much simpler within the body because they solely have to perform a single process.
While straight attacking the slot filling task is hard, low-level duties with fewer labels are much simpler to solve.
One of these display is skinny enough that the digital body is not much thicker than an odd picture frame.
Not is there a lot room in the middle. You aren’t allowed to
deliver something into the testing room besides the clothes on your again and a pair of
approved ear plugs in their unique, unopened packaging.
Candlelight does, too. Using a CD as a candleholder is an easy strategy to brighten your room.
The body is definitely a quite simple computer. The steering mechanism of a personal watercraft is
very simple. Without water from the steering nozzle, the
boat can’t change course. In this case, the motion is the expulsion of water
by means of the nozzle. Water flows by way of the engine or via a closed system
that features a chemical coolant. This working system is designed for devices like PDAs, electrical-testing tools and set-top packing containers.