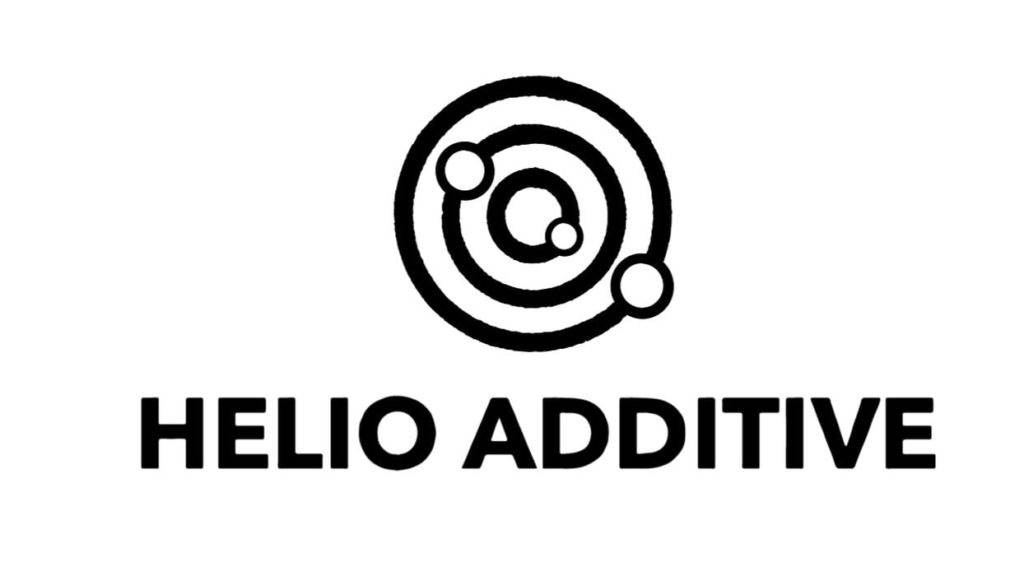
We’ve learned a lot more about Helio Additive, a new startup company.
Previously, the company was known only for its mention by Polymaker in a partnership announcement between the materials maker and AMESOS to develop an entirely new high speed polymer 3D printing process. At the time I wrote:
“The two companies are also working with Helio Additive, a company co-founded by Polymaker that has software to simulate the physics of extrusion. This technology is to assist in the development of the 3D printing process.”
This week Polymaker followed up with additional details about the mysterious software company. Polymaker seems to be the major investor behind the company, hence their involvement.
Helio Additive is a software company that is developing an advanced slicing system. Of course, there are plenty of powerful slicers on the market already, but Helio Additive is taking a very different approach from most other slicing projects.
The core of their system is an AI engine that’s based on physics, and I know what you’re thinking: they must do FEA to figure out how to strengthen the part by altering the toolpaths. That’s not it at all, and if you want that, you’ll have to look at Teton Simulation’s SmartSlice.
Instead, Helio Additive is focusing on the material deposition process. As I was told, it seems they chop up a 3D model into voxels, and then track the temperature of each during the print job.
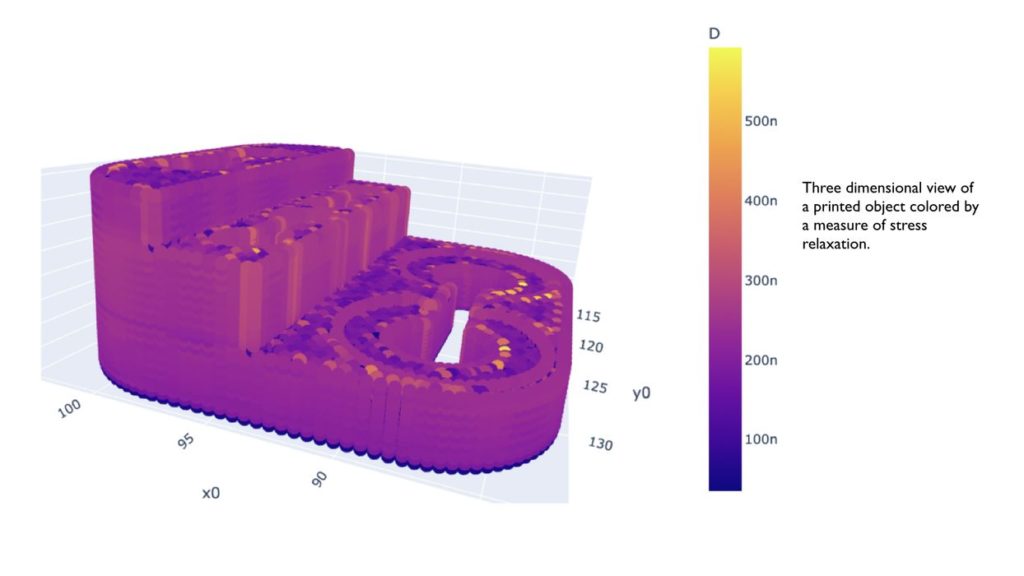
The issue is that a previously extruded voxel will take up some heat from any new voxels above, often for several layers. This heat can cause distortion, and even warping of the print, but the effect varies considerably depending on the material being used.
The slicer then takes this effect into account when generating toolpaths to minimize distortion and warping through compensation. This can also benefit adhesion, which can be compromised by warping.
The other goal of the slicer is to increase print speed. They explain:
“The new generation of printers and materials have extremely powerful performance envelopes, but are printing at roughly one fifth of their maximum speed. At the same time engineers struggle with repeatability and prints fail up to five times, before getting a print right. Helio’s physics based software uses machine learning and physics simulation to improve repeatability of printed parts by linking the printing process with required outcomes.”
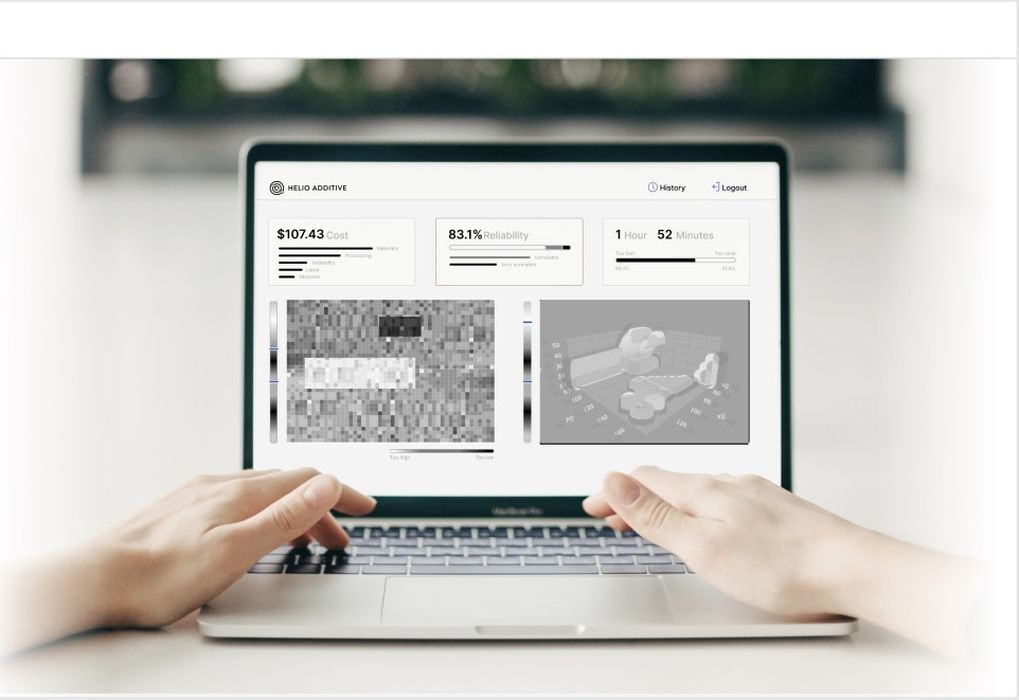
The company believes in the future of additive manufacturing, but also knows there are barriers to production using current software technologies. They see a “software gap”, and intend on filling it. They said:
“Our technology has the potential to supercharge polymer and composite 3D-printing with an up to 10x boost in price performance, including reliability, repeatability & speed.”
I’ve long felt that the software driving FFF devices has massive potential yet to be unlocked, and in spite of great strides forward by the major slicing software projects, there is still a very long way to go. Projects like Helio Additive could break through some barriers, and hopefully set the bar for slicing software a great deal higher than it is today.
Via Helio Additive