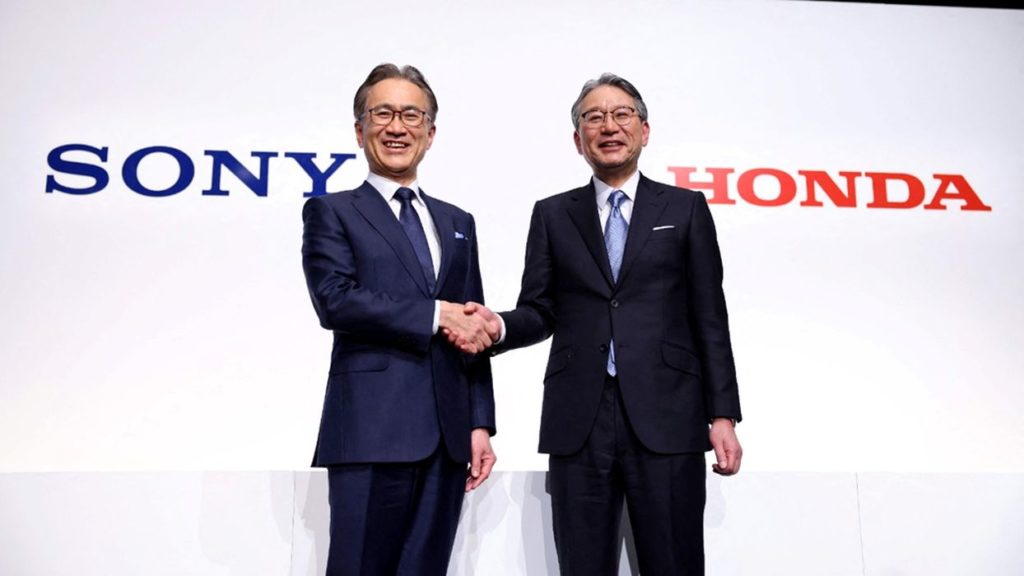
Charles Goulding and Warren Buzzell Jr. look at the recent partnership between Sony and Honda, and see what effect this may have on 3D printing activity.
Honda Motor Co. and Sony Group Corp., two manufacturing giants in Japan, recently announced a joint venture partnership to design and develop new electric vehicles (EV) by 2025. Honda plans to provide vehicle production at their facilities, while Sony plans to provide its online services and electronics expertise to the partnership. Honda is one of the world’s largest engine manufacturers, a leader in the automobile industry, and currently has a global dealership network.
Sony is a leader in the electronic entertainment industry and is well known for its innovation and creativity, also illustrated in our article “3D Printing Impact of Xbox Series X and PlayStation 5”. Sony had previously indicated an interest and want to participate in the EV industry, while Honda has had an embryonic EV partnership with General Motors that is not part of this new venture.
Sony Technology
Sony is known for its complementary metal-oxide semiconductors (CMOS) sensor technology and camera technology. CMOS sensors convert photons into electrons for digital imaging. Some important characteristics of CMOS devices are their high immunity to noise and low static power consumption. Currently, many organizations are developing new 3D printed CMOS electronics processes and components.
At the recent 2022 CES electronics trade show, Sony introduced its concept car, the Vision-S, equipped with 33 sensors and the following technologies: lidar, radar, cameras, 360 immersive audio, and a dashboard stretching panoramic display. Incorporating 3D printing technology into their electric vehicle designs enables Sony to develop more customized electronics with unique enclosures and capabilities. It also allows their engineers to design for functionality instead of manufacturability, potentially leading to more robust system designs with embedded electronics, encapsulated sensors, and unique antennas.
Honda 3D Printing
Honda has a deep 3D printing expertise, beginning in 2006 with Stratasys printers, including producing over 300 accessory components such as wheels, knobs, and trunk components. This eventually led them to purchase an Objet Eden500V for daily usage.
Since then a subsidiary of Honda Group called Honda Access has been utilizing 3D printing technology to develop custom accessory parts and prototypes on-demand. Honda has stated their love for incorporating 3DP technology into the product development phase because it allows them to accurately evaluate the fit and functionality of their designs through prototypes. It also allows them to modify their product designs on the fly–improving both the quality and speed of the prototype process.
The Research & Development Tax Credit
The now permanent Research and Development (R&D) Tax Credit is available for companies developing new or improved products, processes and/or software.
3D printing can help boost a company’s R&D Tax Credits. For example, wages for technical employees creating, testing, and revising 3D printed prototypes can be included as a percentage of eligible time spent for the R&D Tax Credit. Similarly, when used as a method of improving a process, time spent integrating 3D printing hardware and software counts as an eligible activity. Lastly, when used for modeling and preproduction, the costs of filaments consumed during the development process may also be recovered.
Whether it is used for creating and testing prototypes or for final production, 3D printing is a great indicator that R&D Credit eligible activities are taking place. Therefore, companies implementing this technology at any point should consider taking advantage of R&D Tax Credits.
Conclusion
The EV partnership with these two giant companies gives Japan a national direction and should encourage Japanese universities and research centers to support the development of more 3D printed EV technology. Furthermore, whether it be for prototype testing or improving electronic capabilities, the leading European and the United States EV product manufacturers, universities, and research centers should also take notice of the robust opportunities available by utilizing this technology.