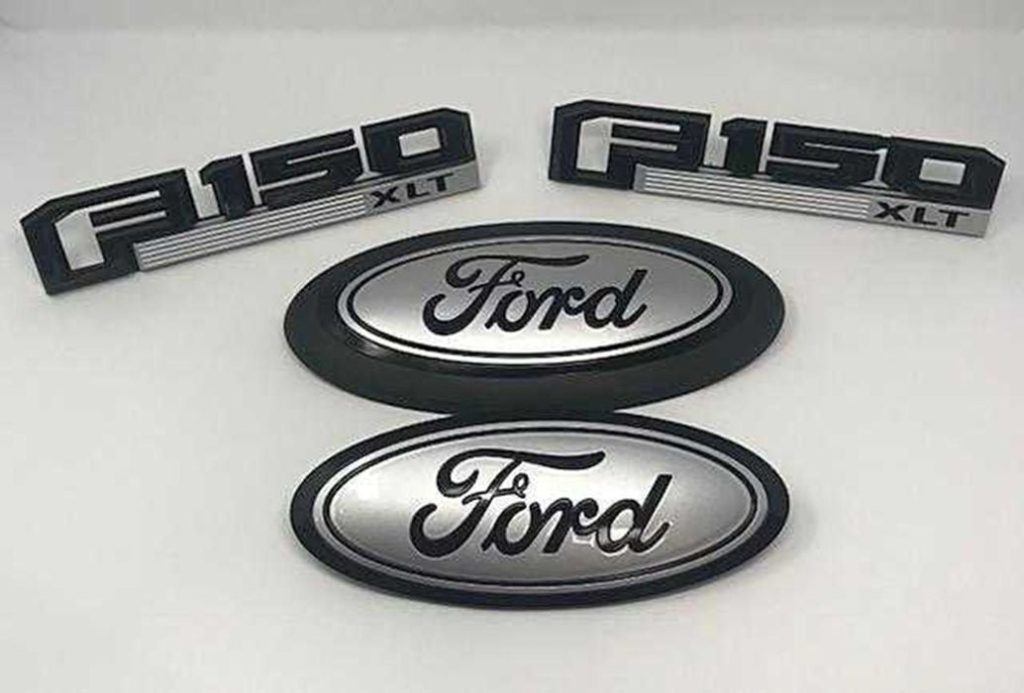
Charles R. Goulding and Preeti Sulibhavi wonder why Ford didn’t use 3D printing to resolve a recent supply chain issue.
One of the greatest movie lines comes from the 1974 Mel Brooks movie, “Blazing Saddles.” The line goes, “Badges, we don’t need no stinkin’ badges!” The original line came from the 1948 classic, “The Treasure of Sierra Madre.”
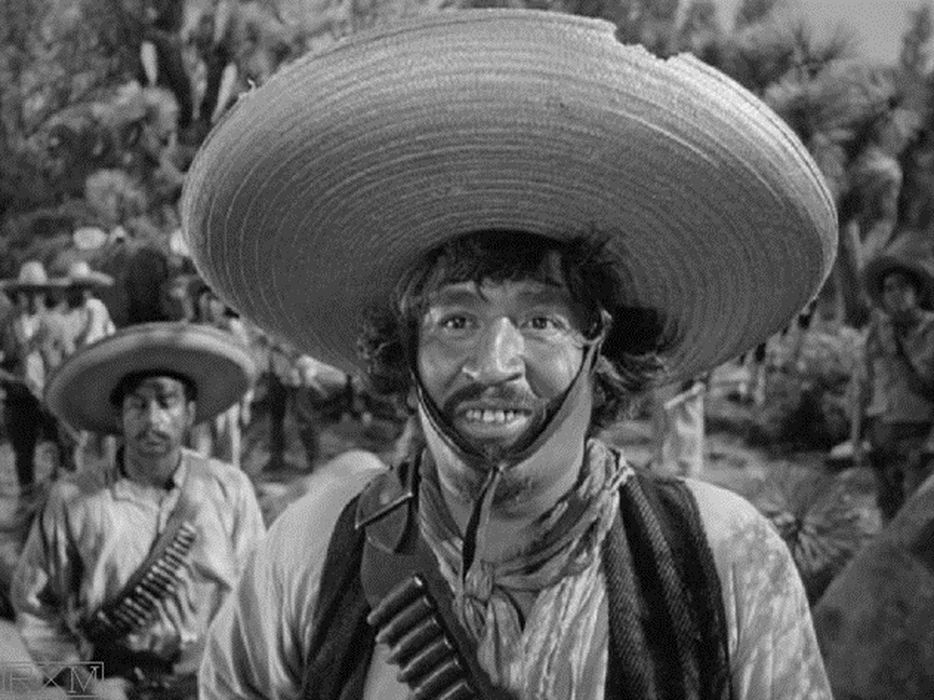
Recently Ford Motor Company has been unable to ship multiple new model brands due to a shortage of Ford-branded tradename plates. When Ford was asked why they simply didn’t 3D print them, the response was that the 3D printed versions they tried didn’t have the appropriate quality.
Frankly, we found this to be a surprising response. We would have thought that high-quality emblems could certainly be 3D printed. It’s disappointing in this supply-constrained new car market, to see an automobile delivery further delayed simply for the lack of a nameplate.
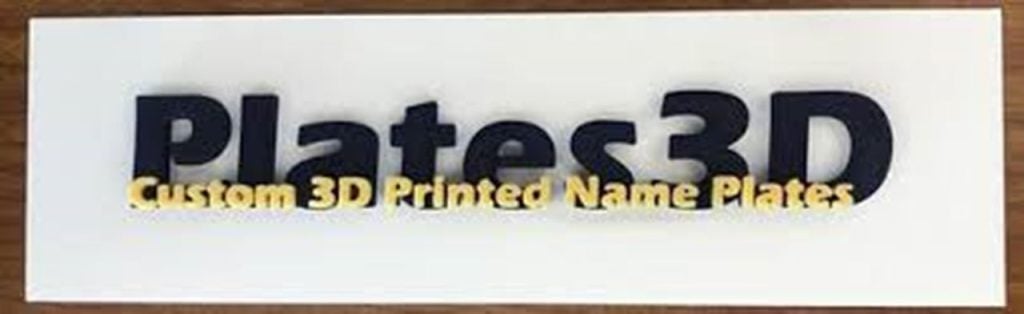
There are a variety of sites online that offer customized, 3D printed name plates that includes personalized license plates (with proper documentation). So, Ford’s explanation does not seem reasonable, especially with recent advances in 3D printing to include high quality aluminum and other metal 3D printing capabilities.
Perhaps they did not find the right vendor or use the most appropriate 3D printer. Either way it appears they have quickly overlooked finding solutions to what could be the answer to their supply chain problems.
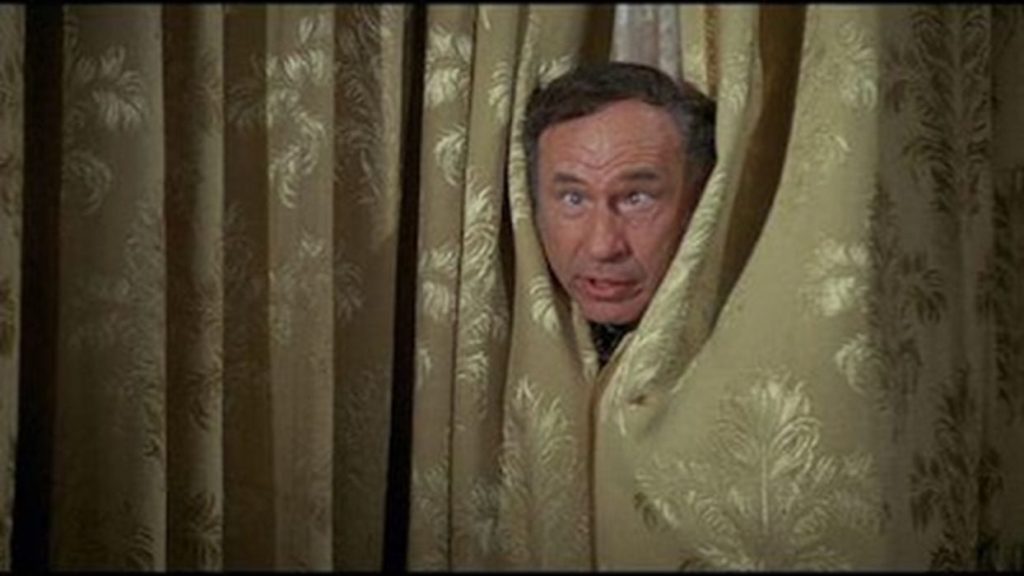
The name plate fiasco is actually more symptomatic of serious supply chain challenges at Ford. The company has recently announced US$1B in additional costs related to supply chain issues and a realignment of senior executives to address these supply chain issues.
The Research & Development Tax Credit
The now permanent Research and Development (R&D) Tax Credit is available for companies developing new or improved products, processes and/or software.
3D printing can help boost a company’s R&D Tax Credits. Wages for technical employees creating, testing and revising 3D printed prototypes can be included as a percentage of eligible time spent for the R&D Tax Credit. Similarly, when used as a method of improving a process, time spent integrating 3D printing hardware and software counts as an eligible activity. Lastly, when used for modeling and preproduction, the costs of filaments consumed during the development process may also be recovered.
Whether it is used for creating and testing prototypes or for final production, 3D printing is a great indicator that R&D Credit eligible activities are taking place. Companies implementing this technology at any point should consider taking advantage of R&D Tax Credits.
Conclusion
Ford could give 3D printing a second try if it would like to find a quick, high-quality workaround to its supply chain and material sourcing issues. We do need those stinkin’ badges, and 3D printing can help!