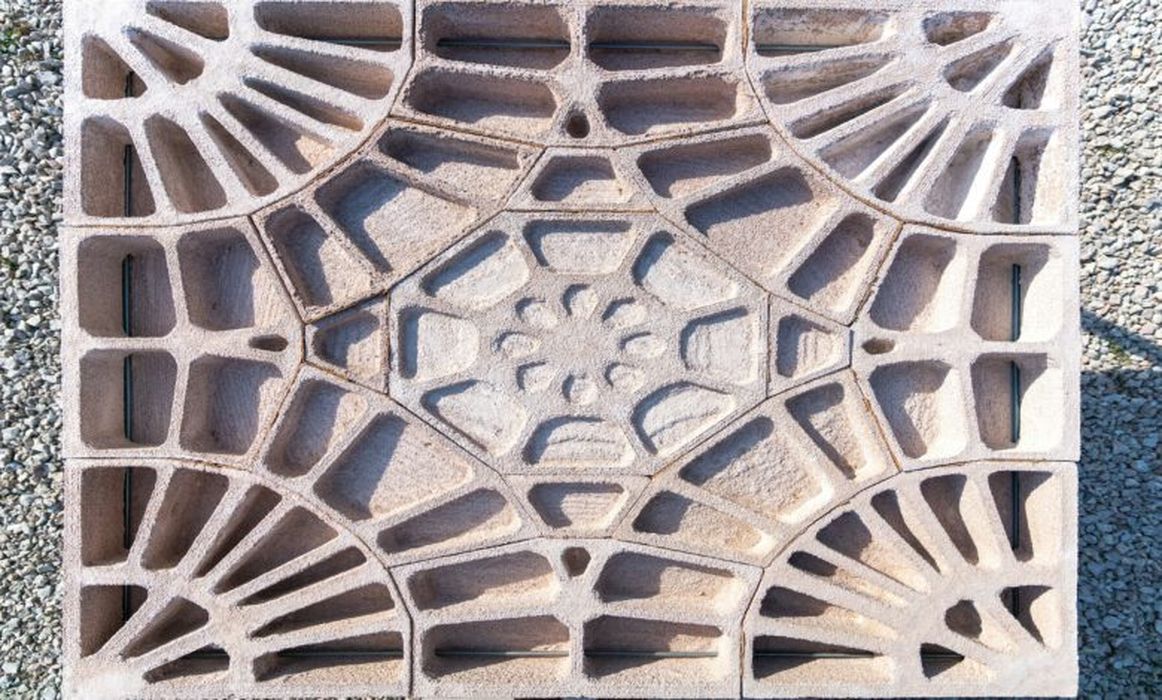
In places like Ticino, Switzerland, ‘rock flour’ can constitute up to 40% of total production, according to ETH Zürich.
According to Digital Building Technologies, researchers at the Swiss Federal Institute of Technology Zurich (ETH) and the University of Applied Sciences and Arts of Southern Switzerland (SUPSI) have developed a 3D printer designed to transform large quantities of stone waste from quarries into customizable architectural elements.
The stone waste, or rock flour, in places like Ticino, can constitute up to 40% of total production. The printer was demonstrated in a case study, where it fabricated an optimized floor system using the byproduct of a marble quarry in Ticino.
This project offers a real-world example of how 3D printing can reduce overall construction material consumption and foster the usage of local, recycled resources. The final product, an assembly of the floor system, will be showcased at the Venice Architectural Biennale in 2023.
The team at ETH Zurich has innovated upon the existing Binder Jetting (BJT) 3D printing method. The traditional BJT, which uses a binding compound to solidify granular material layer by layer, was found to have limitations for construction use due to the brittleness of printed parts and poor fire and weather resistance.
The researchers propose an alternative binder based on geopolymer – leading to a redesign of both the hardware and software known as Geopolymer Binder Jetting (GeoBJT). This system not only improves the performance of the printed parts but also allows a wider range of materials for binders and particles, and higher build-up rates. Furthermore, it employs a mobile container-based setup for on-site operation, akin to a field factory.
Read the rest of this story at VoxelMatters