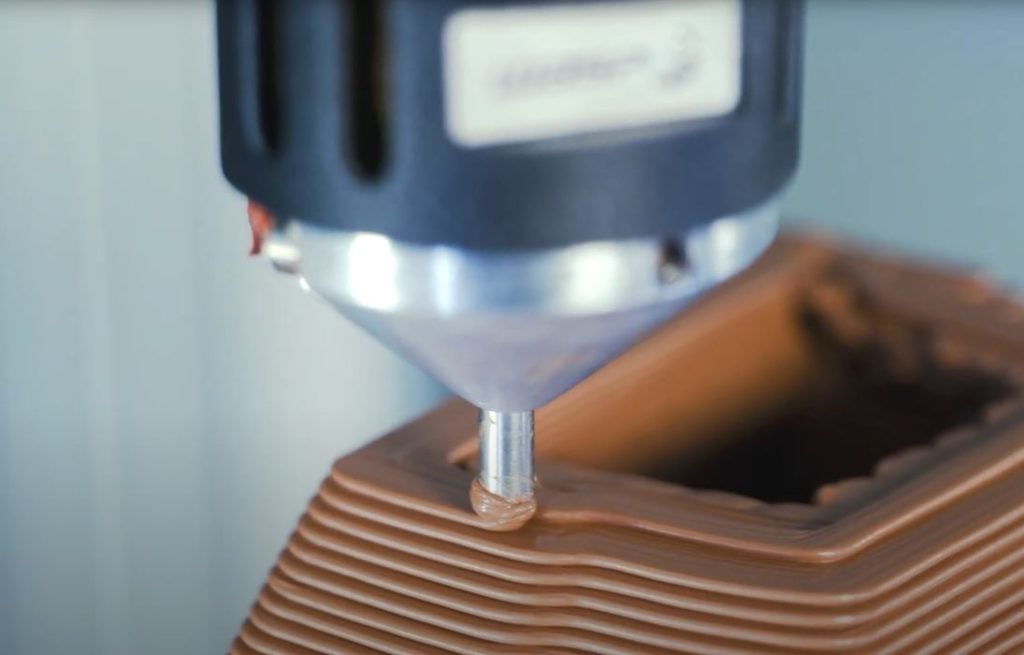
WASP has partnered with Honda to develop a new process using 3D printed clay.
Italy has been producing clay 3D printers for as long as I can remember, having first seen them way back in 2013. Their goal at the time was to produce a means for building homes in remote areas using local materials. That local material was to be clay.
Since then they’ve had some success in that area, announcing the “Crane WASP” in 2018, which intended to take their clay-printing technology to the point where entire buildings could be 3D printed.
The company has always been exploring unusual niches for 3D print applications, and this week’s announcement of a partnership with Honda R&D Europe follows the same line.
WASP explains:
“HONDA R&D Europe and WASP D&D (Discover & Development) have worked to innovate and speed up the industrial development process. The new process accounts for an unprecedented freedom in manufacturing. The prototypal parts obtained can be easily hand-finished and re-worked in case they do not meet the required specifications. The industrial clay used in the process can be re-used and re-printed countless times and with minimal waste in a logic of environmental and economic sustainability.”
What this means is that they’ve been able to use their clay 3D printer, likely the WASP 3 MT, to produce rough clay models for automotive designs.
A design is first created using digital CAD tools, and then transferred to the WASP 3D printer. The printer then produces a life-size clay replica of the 3D model. However, as the clay extrusion is quite coarse, the final print includes highly visible step-like layers.
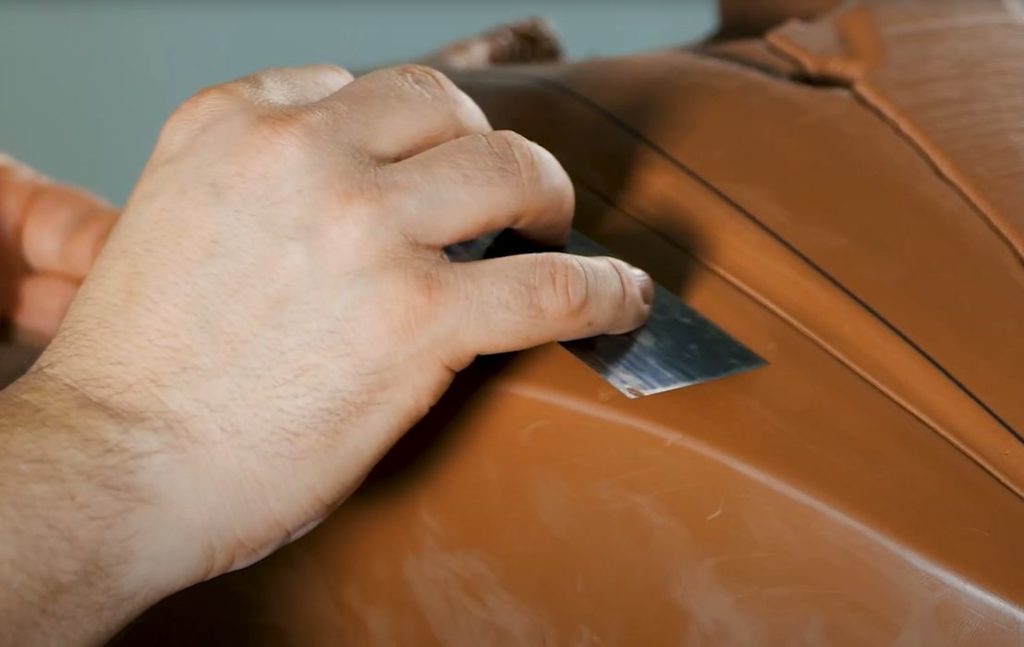
Then the traditional clay modelers take over and smooth the print’s surface with manual tools. At this point the clay model is essentially identical to those that would have been produced with a manual process, except that they are more accurate, completed more quickly and easily replicated.
Traditional approaches might have created the clay model using milling, or built entirely manually.
For Honda, it means they can take advantage of 3D print technology without having to do major surgery on their traditional workflows. They need only produce the clay print and insert it into their normal workflow, which continues as it has always done.
Heres a video of the process:
This is indeed a niche application for clay 3D printing, but it’s one I haven’t seen previously. Having demonstrated this approach successfully at Honda, it may be that other automotive design facilities may take notice and try out the new clay technique.
What other applications might be identified for clay 3D printing? I’m not sure, but there are certainly many more.
Via WASP