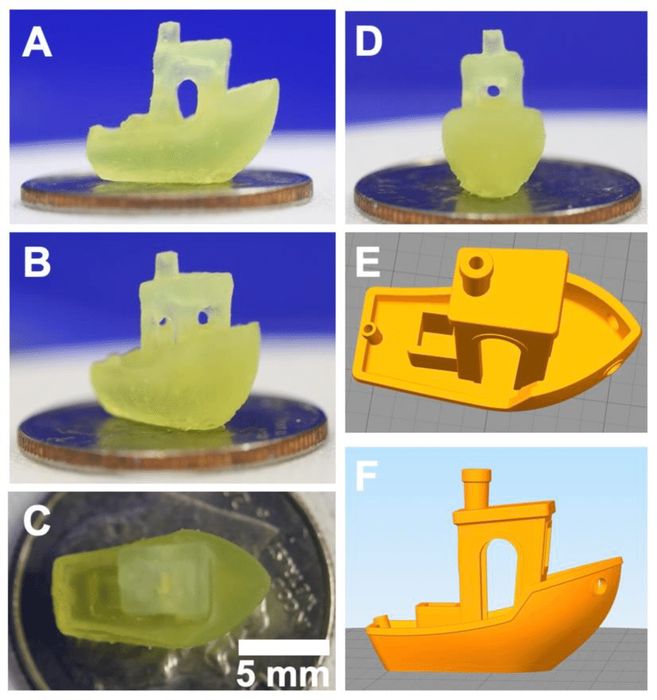
New developments in volumetric 3D printing suggest only one future for resin 3D printing: volumetric.
If you still haven’t heard about volumetric 3D printing, I’m not surprised because there are very few — maybe only one — commercial volumetric 3D printer products announced, and none have yet shipped.
The buzz about the technology is slowly growing as more people discover what it is about and how it could change things. We’ve written multiple stories on the technology, including one piece on the first announced volumetric device from xolo, the xube.
The basis of the technology is to use a vat of transparent photopolymer resin and light projection to form objects. That sounds a lot like standard SLA, DLP or MSLA approaches, but they are all 2D in nature: they print objects layer by layer.
Volumetric 3D printing, on the other hand, is able to 3D print the ENTIRE OBJECT ALL AT ONCE.
The process involves projecting changing light patterns into the vat as it rotates. The images projected are generated by creating a kind of “X-ray” view from each respective angle.
If that sounds familiar, you might realize this is similar to CT scans, where X-rays pass through a patient and are combined to form a 3D image. Volumetric 3D printing is exactly like that, but in reverse. Generate the images to print the “patient”.
The advantage of volumetric 3D printing is mostly speed: prints can actually be completed in only minutes, sometimes even seconds! This technology is the one that will forever shatter the speed barrier that’s held back 3D printing ever since it was conceived decades ago.
But there are many challenges yet to overcome.
There are plenty of questions about the possible materials that can be used, as there is a requirement for transparent resins. This may preclude resins that include additives that provide useful properties, which are commonly used in 2D resin 3D printing.
There’s also questions about the amount of power required to push light through a large and deep vat: if the energy is absorbed too early, then quality may suffer.
Those and other problems may spell the end of volumetric dreams, but this may not be true. There is significant research underway today in several institutions to overcome them and generally increase the capability of volumetric processes.
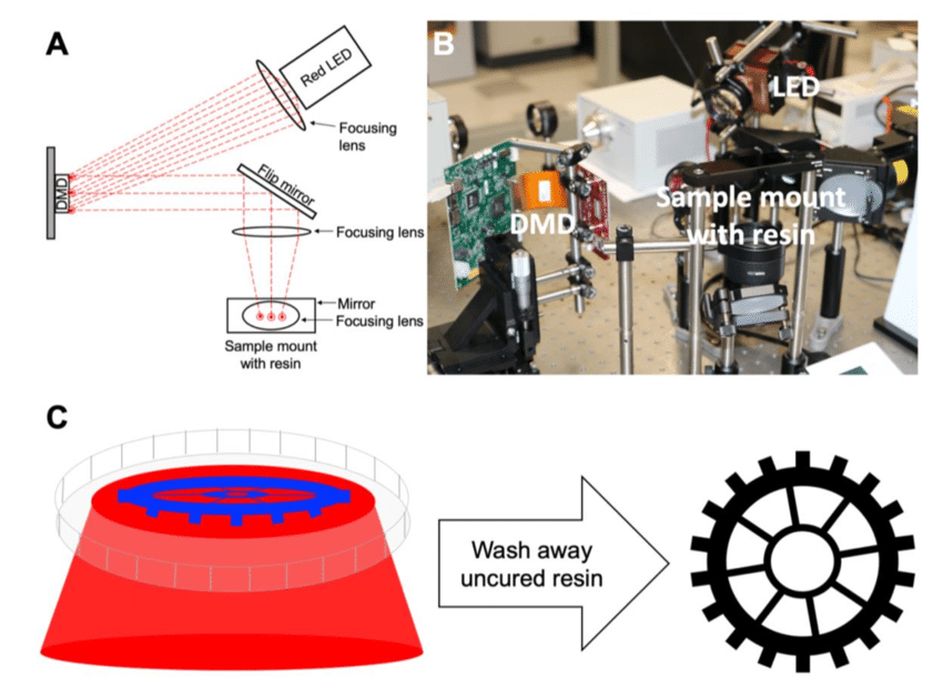
One recent example of volumetric improvement appeared in Nature, where researchers added capsules to the resin that would upconvert incoming light to more favorable frequencies for polymerization. They explain:
“To induce photopolymerization deep within a vat, the key advance is the nanoencapsulation of photon upconversion solution within a silica shell decorated with solubilizing polymer ligands. This scalable self-assembly approach allows for scatter-free nanocapsule dispersal in a variety of organic media without leaking the capsule contents. We further introduce an excitonic strategy to systematically control the upconversion threshold to support either monovoxel or parallelized printing schemes, printing at power densities multiple orders of magnitude lower than power densities required for two-photon-based 3D printing.”
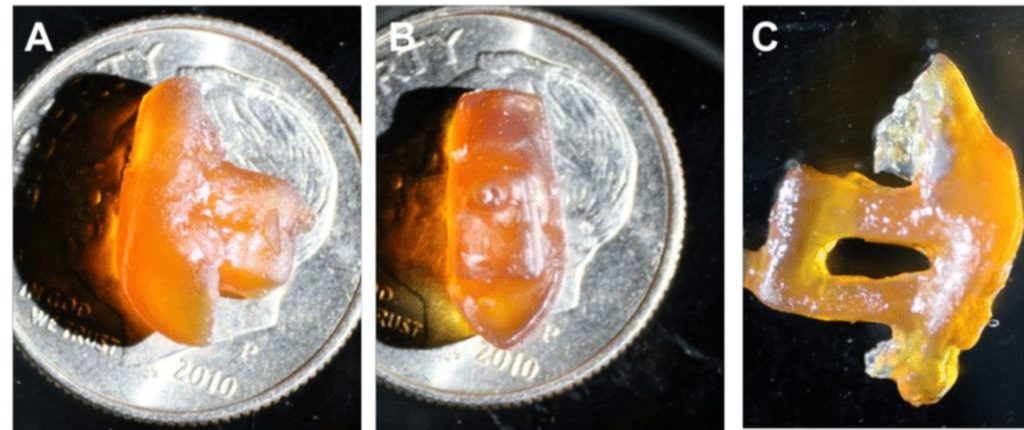
Basically the researchers, with the unusual resin additives, were able to 3D print with vastly less power than used by earlier volumetric 3D printer designs. They call this process “triplet fusion upconversion”.
It’s a fascinating process where red light passes through the resin to cause a collisions that emit blue light, which causes polymerization. Through this approach they are able to gain significantly control over the polymerization process.
By tuning the chemistry of the additives, the print speed and laser power, they could “trace a well-defined focal point in space throughout.” This allowed them to reproduce features as small as 0.05mm, and they believe they could achieve even better in the future.
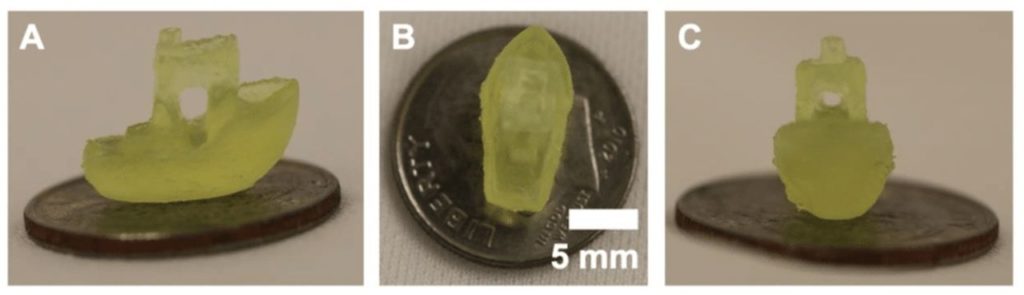
Where could this research lead? They explain:
“This technique enables printing in resins that cannot be printed in a traditional SLA 3D printing setup, such as resins with high viscosity, resins requiring air-free polymerizations techniques48, or prints with soft or flexible parts. Moving forward, optical engineering of projection-based systems to achieve high numerical aperture over large field of view will allow access to increasingly complex 3D prints at 100,000s of pixels at a time using continuous wave, low energy lasers: 3D printing without steps between layers.15,47 We expect the ability to tune the threshold behavior over orders of magnitude to facilitate tailoring of these UCNCs to a variety of printing excitation schemes beyond the simple monovoxel or parallel excitation printers demonstrated here, such as full projector-based printing approaches, which can enable a variety of applications that require rapid, customizable, precision 3D printing. Finally, we expect to combine this technique with recent technological developments in optical parallelization to greatly increase print speeds.”
This is incredibly good news for volumetric technology. While the process is still under development, the fact that researchers were able to break through several barriers in this paper suggests there is more to come.
At some point the technology will be feasible for commercialization, and then we’ll start to see a rapid explosion of volumetric technology that could ultimately replace many of today’s resin 3D printers.
Via Nature