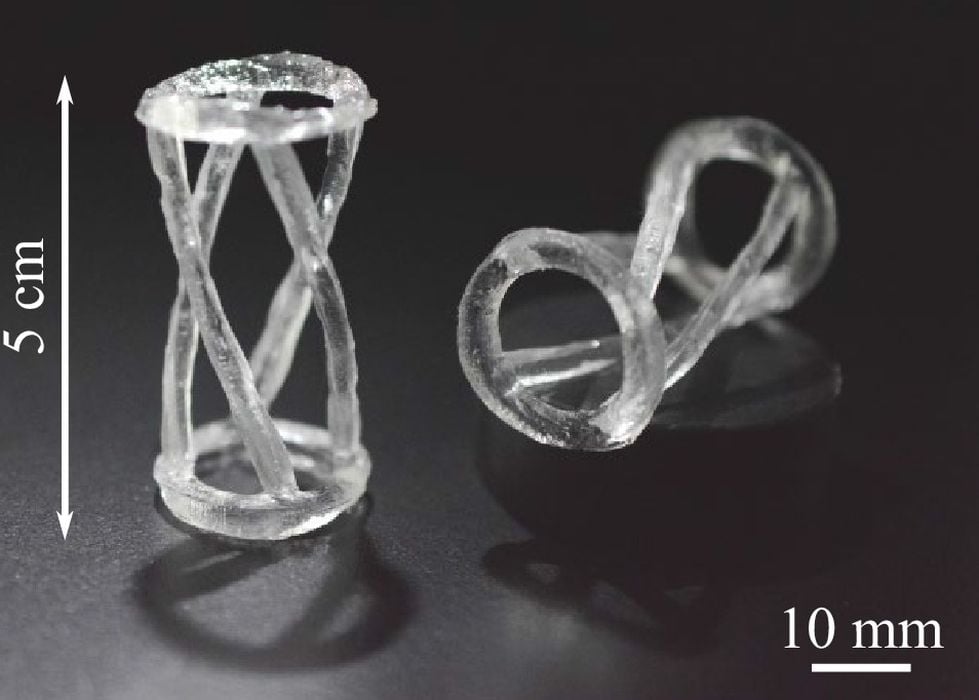
A new approach to volumetric 3D printing, VHAM, enables production of larger objects.
Volumetric 3D printing, sometimes called VAM (Volumetric Additive Manufacturing), is an entirely new approach to building 3D objects.
Rather than building the object layer by layer as is done in virtually every conventional 3D printing process, the volumetric approach involves forming the object all at once.
The basic approach is like the reverse of a CT scan. Instead of capturing 2D images of a 3D subject as is done with CT scans, 2D images are projected into a vat of photopolymer resin. Typically the vat will rotate, allowing projection to take place from multiple angles.
The idea of the repeated 2D projections is to produce sufficient energy delivered to any voxel intended for solidification. You might think that blasting UV rays through a resin vat would simply cause the entire chamber to solidify, but that’s not how it works.
Instead the energy is moderated so that it passes through the entire chamber. But subsequent exposures from different angles can cause accumulations of exposure at desired points in 3D space within the vat. Eventually the accumulation is sufficient to trigger polymerization.
Volumetric 3D printing can produce objects very rapidly, and there are experimental examples of objects being produced in only minutes or even seconds in some cases.
The approach shows much promise for the future, but for now there are still some limitations.
One is that the resin must be optically clear to allow UV light to penetrate to the center of the vat.
Another is the build volume. Current approaches are limited to objects in the centimeter range, which is pretty small. If volumetric 3D printing could produce larger objects it would immediately become far more practical for applications.
That was the challenge undertaken by researchers at EPFL, who developed a variation of the process they call “Volumetric Helical Additive Manufacturing”, or VHAM.
Their method is relatively straightforward, but apparently hasn’t been previously attempted using volumetric processes.
While their VHAM system rotates the resin vat, it also slowly rises it as the print proceeds. This results in a helical trajectory for the material, as it spirals upwards. The vat actually moves rapidly upwards and downwards during the print job.
This enables the off-center projector to access much more volume within the resin tank, increasing the size of objects that can be printed with VHAM. However, it also requires more complex calculations for generating the projection images.
The researchers were able to 3D print a number of objects using their experimental VHAM setup, and verified the accuracy and reliability of the process. They were able to produce objects up to 30 x 30 x 50 mm, “in only a few minutes” using VHAM.
This is a promising development for volumetric 3D printing that shows there is much more to the process than first seen. My expectation is that volumetric technology will gradually increase in capability until it eventually supersedes current resin processes.