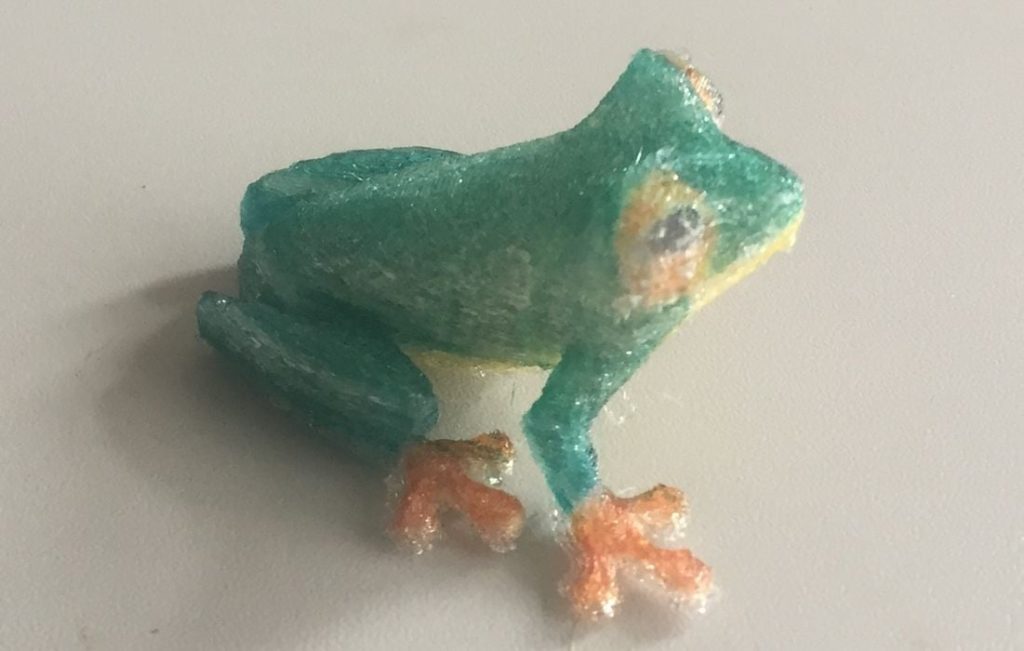
Aad van der Geest is working on a new concept called “Double i3” that should be able to 3D print in full color.
If the name “van der Geest” sounds familiar, it’s because he’s been in our pages previously. Way back in 2016 he developed something called the “ColorPod”, a way to modify a FFF 3D printer into a full color powder 3D printer. This system used a color 3D printing process similar to the original ZCorp process from decades ago.
Later, the ColorPod was adapted to 3D print edible objects.
Now he’s developing another color 3D printing system, but not using powder.
The Double i3 concept is exactly what its name implies: it is essentially two i3-style 3D printers in one. There’s a standard extrusion system to deposit thermoplastic material, and the second system is a toolhead that applies colored ink to each layer. The accumulation of plastic and ink layers results in an object with color.
To make this work, van der Geest uses clear PLA material and water-based inks. The clear material easily absorbs the color application, and there are no “color lines” in the resulting print.
van der Geest explains how the process works:
“First experiments are done with clear PLA and water based ink. After a plastic layer is laid down the build plate moves to under the second frame where colour is added in the form of cyan, yellow and magenta ink.
Models are sliced with Cura and also with a full colour slicer. Each time before the extruder moves to the next layer special software lets the inkjet printhead move in a zigzag movement over the printed object. It all works with the stock marlin firmware in the i3. Signals for the unused second extruder now control electronics that lets Marlin switch output between the first and the second vertical frame.”
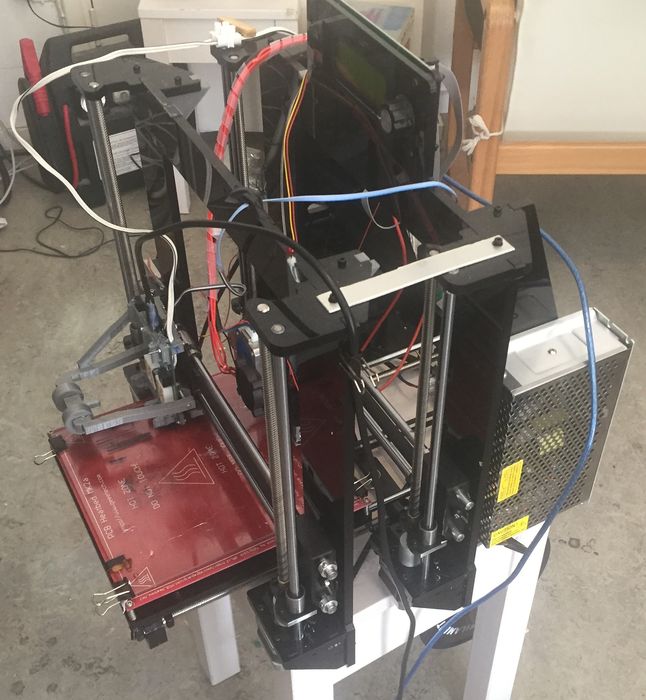
He has been modifying Geeetech Prusa i3 C kits to implement the color system, but I suspect the approach could be modified for use with other i3-style devices.
I’ve seen something slightly similar to this approach previously, with the XYZprinting da Vinci Color mini. However, instead of using a second print head, the da Vinci Color mini would squirt some ink into the clear filament path as it proceeded. The results were full color, but not particularly accurate. This device is still offered, along with a higher-end device, the da Vinci Color.
van der Geest’s approach is different in that the layer itself is fully “inked” after deposition. This could be an advantage over XYZprinting’s approach, where the accuracy of color deposition can be inaccurate due to filament flow. Now-defunct MCOR Technologies used this “color layer” approach with their paper 3D printer, and they were able to achieve reasonable color resolutions.
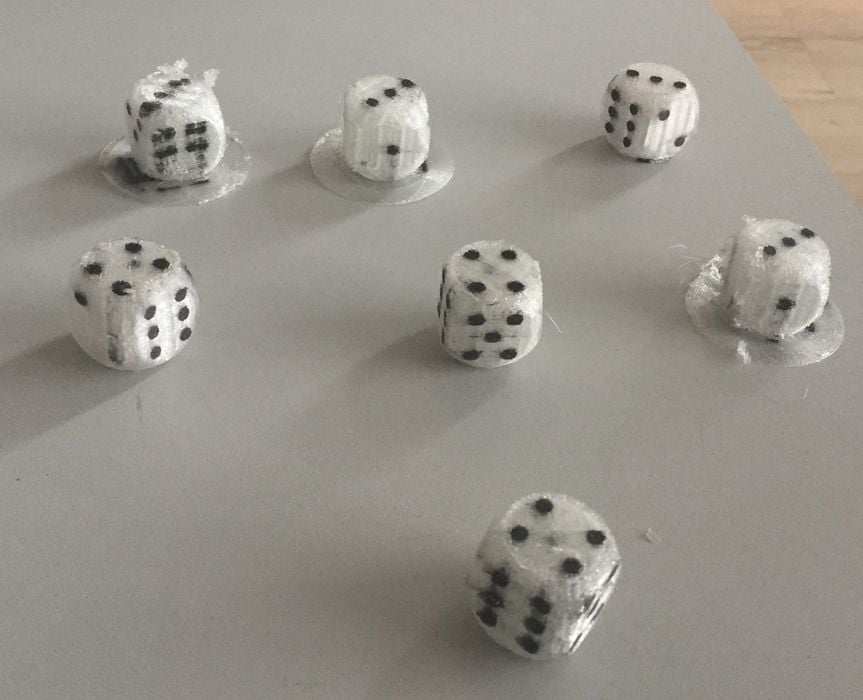
At this time, the Double i3 seems to be an experiment, as there is no way to purchase a device or conversion kit, nor even a website. The results, as you can see in the images and videos here, are less than spectacular. This is to be expected on a new technology.
van der Geest told us he is testing other types of inks and filaments, and he may be able to uncover a combination that works very well.
If this can be made to work, it could be quite important. Current low-cost color options for 3D printers are only “spot color”, where the color palette is limited to the input filaments: systems are merely switching between filament colors, not making new combinations.
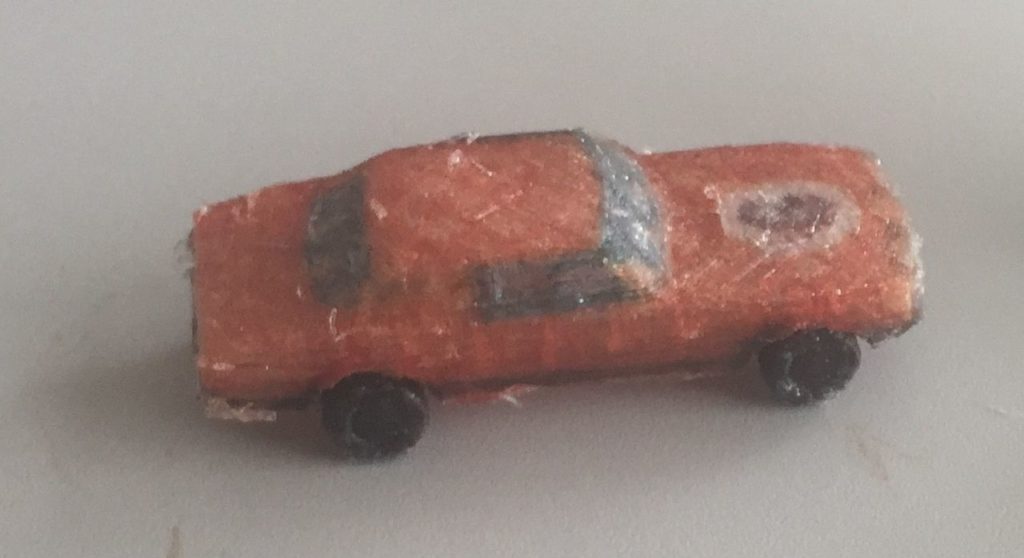
Combining colors is precisely what’s done with inkjet systems: Cyan, magenta and yellow can be combined to produce ANY imaginable color. This means that the Double i3 approach could, in theory, produce photorealistic textures on prints.
Currently, the lowest price option for this style of color is probably the latest Mimaki 3D printer, which costs around US$40K.
That is, if the current color contrast problems can be rectified.
Perhaps we’ll see a low cost full color 3D printer appear soon that costs under US$2000.