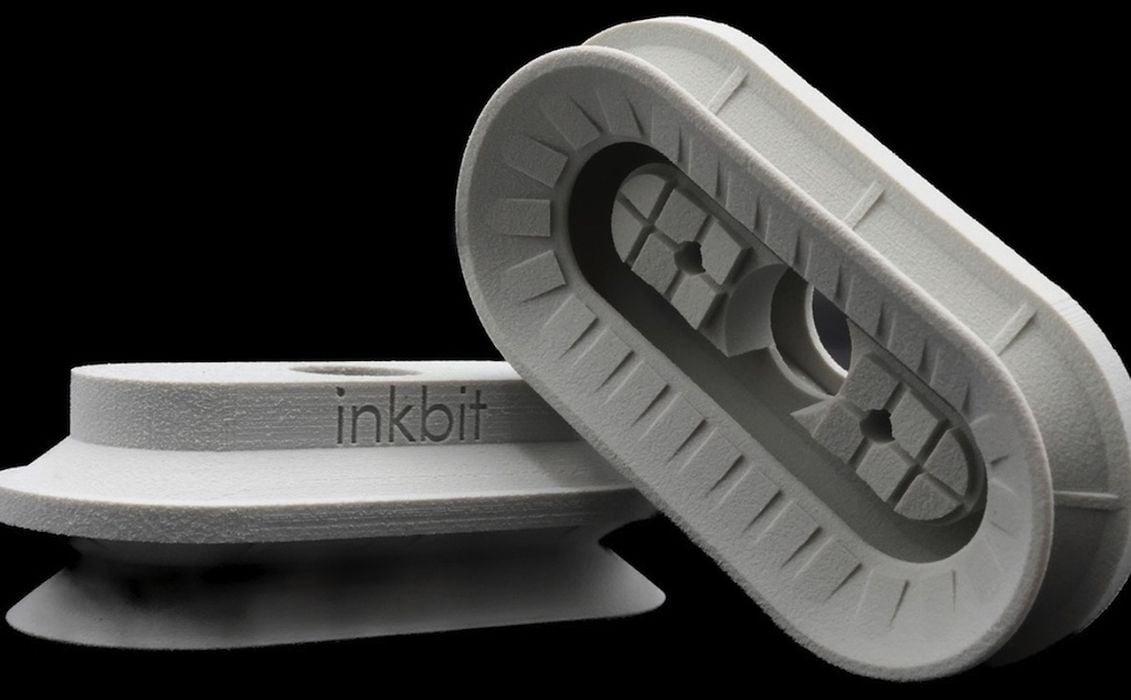
Inkbit announced a new material, and I think this is quite a bit more important than you might realize.
The company has developed a unique 3D printing process they call “Vision Controlled Jetting”, or “VCJ”. It’s designed for high-throughput production 3D printing, and it’s quite fascinating to see in action.
VCJ involves a massive toolhead that rapidly swings back and forth over a large build volume. On each pass it’s selectively dropping tiny droplets of materials — from up to four sources.
The technical challenge with VCJ is keeping the huge toolhead and inkjets perfectly aligned during its rapid motion. They seem to have solved this issue, and it might have something to do with the “V” (vision) part of the process’ name.
VCJ printing typically produces a huge 500 x 250 x 250 block of parts embedded in wax, which is their support material. By simply heating the block, the wax melts and releases all the parts. The parts I’ve seen have extremely high resolution and dimensional accuracy, making for a very decent production machine.
On to the new material: it’s TEPU 50A, a “soft-medium durometer elastomer”. This is a flexible material, the second for Inkbit in their equipment. Inkbit describes the material:
“TEPU 50A is a thiol-ene polyurethane-based elastomer with a Shore 50A durometer and low compression set that offers excellent UV stability and strong chemical compatibility. TEPU 50A is the latest addition to the Inkbit Vista ecosystem, developed in response to customer requests for a Shore 45-55A elastomer that could accurately produce intricate detail in a wide range of geometries with excellent surface finish and elastic resilience.”
The company previously announced a TEPU 30A material, but it seems that TEPU 50A is UV resistant. That means it is suitable for outdoor applications where it can be exposed to the sun without fear of degradation.
This opens up many possibilities for multimaterial parts. Consider that a print on the Inkbit system could include both rigid and soft materials. Think of grippers, handles or flexible flaps.
One can only imagine the geometric possibilities of combining rigid and soft materials into a single print. It’s conceivable that some “final products” could now be produced with VCJ without the need for assembly afterwards.
The new material will also be of interest to the automotive industry, where countless gaskets and seals are routinely produced. This material could allow auto makers to develop that type of part with unusual geometries that are not normally possible with conventional manufacturing systems.
My suspicion is that Inkbit is also working on the development of further advanced materials that they could eventually announce. Today’s TEPU 50A announcement would be one more step on that path. Ultimately, it may be that VCJ operators would have a huge choice of materials and thus be able to produce large quantities of parts containing up to three different materials.
Via Inkbit