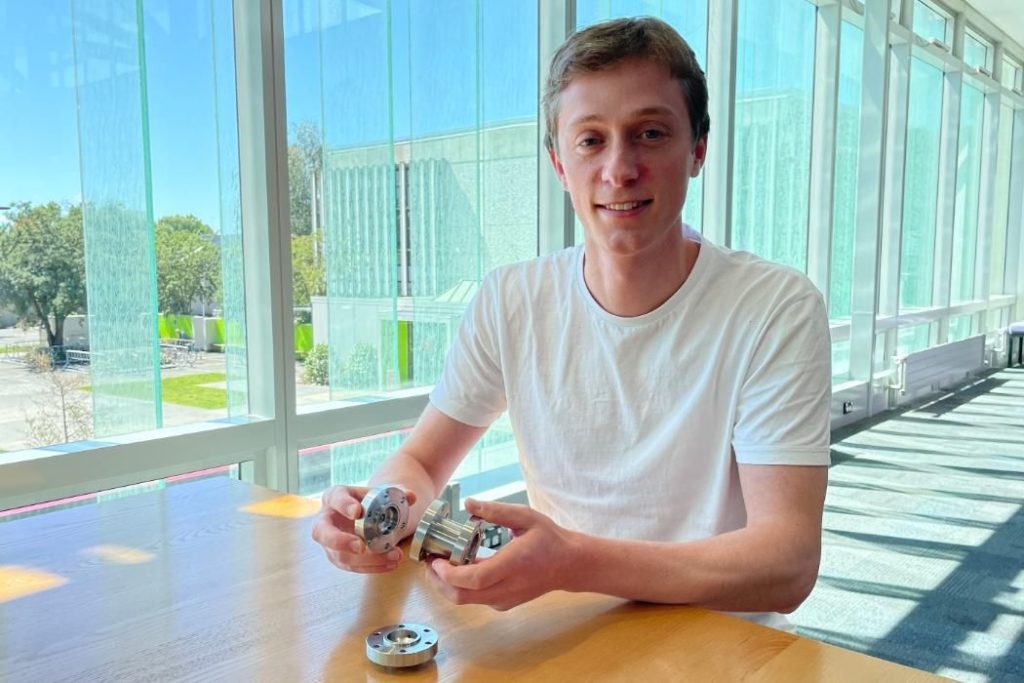
A PhD student in New Zealand is 3D printing catalysts to enable use of safer rocket propellants.
Simon Reid is exploring ways of creating unusual geometries for hydrogen peroxide catalysts, and the only way to do so is by leveraging 3D print technology’s capabilities.
Let’s back a bit. Why is this required? It turns out that it all has to do with something called “hypergolic” propellants. Normally you need three things to create fire (or a rocket engine firing): fuel, oxidizer and a trigger. Sometimes the trigger is an electrical mechanism, other times it’s chemical.
However, that trigger mechanism is extra parts and extra weight. Could they be eliminated somehow in a vehicle that’s dependent on weight? The answer is yes, hypergolic propellants are those which automatically ignite upon contact with another substance. This removes the need for an igniter and not only lightweights the application but also makes it far more reliable. You wouldn’t want to be sitting on the Moon with a rocket engine that wouldn’t start, would you? That’s why the Apollo landers used hypergolic fuels in their engines.
However, there’s a big problem: the most commonly used hypergolic fuel is hydrazine, which is enormously toxic. It is said to cause cancer and can damage internal organs even with small amounts of exposure. Nasty stuff.
There’s another possibility for a much safer hypergolic propellant: hydrogen peroxide. “H2O2”, when in contact with certain catalyst materials including platinum or silver, will separate into a flow of oxygen at 700-1000C. This can be mixed with common kerosene to instantly ignite a rocket engine. And that’s far safer than using hydrazine.
But there’s a problem. The catalytic process H2O2 undergoes tends to corrode the catalyst away quickly. This is why this approach hasn’t been used much.
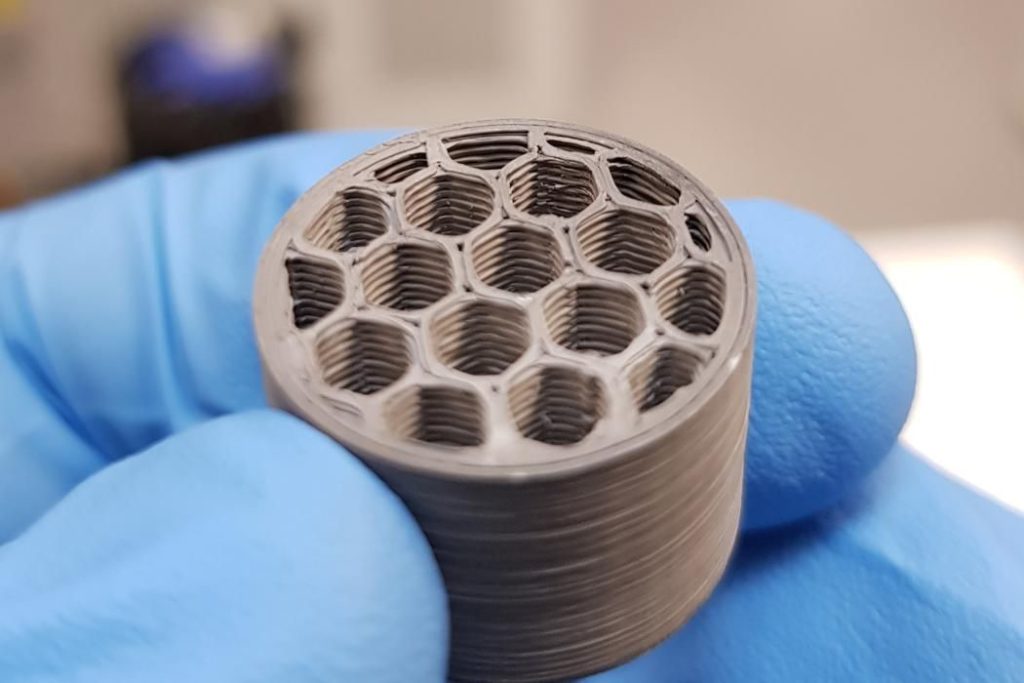
Reid’s project is to design a complex flow channel through which H2O2 could be properly exposed to a catalyst lining the chambers inside before it hits the combustion chamber. As you can see here, the design involves maximizing the surface area to make the reaction process most efficient.
Reid explains:
“Only a few companies are seriously considering hydrogen peroxide. Hopefully by designing these efficient catalysts we can promote it as a viable alternative to hydrazine, and help make the aerospace industry that little bit safer.”
This is a complex project, as it requires Reid to balance a number of factors in the engineering design. One key factor is that the extreme temperatures produced in the reaction can quickly erode many types of catalyst materials.
The approach used by Reid seems to be 3D printing the rocket engine part in a ceramic material that can withstand the extreme heat, and then coating it with the catalyst material.
It appears the project is not yet complete, but with 3D printing’s ability to quickly iterate new designs, I’m certain this project will have a good outcome.