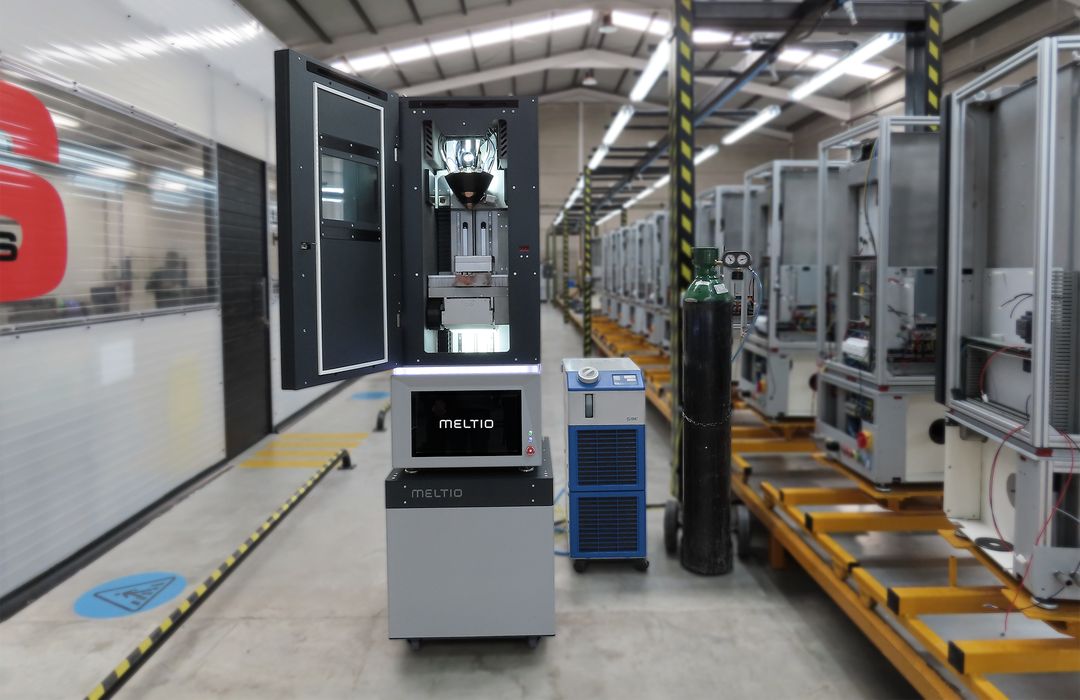
Meltio has been selected by the US Department of Defense as a strategic partner.
The Spanish company produces a unique 3D printing system comprised of a robotic arm and wire-based additive manufacturing printhead. Wire is fed through the printhead, where an array of powerful lasers quickly melt the material, a process known as “Direct Energy Deposition”, or “DED”. As the printhead moves around robotically, it gradually deposits material to build up complete 3D objects.
The award was part of the US Army’s xTechInternational Advanced Manufacturing and Materials program. What’s that all about? The army explains:
“The U.S. Army would like to invite interested entities to participate in the 2023 xTechInternational Advanced Manufacturing and Materials competition, a forum for eligible international small businesses and international academic institutions to engage with the Department of Defense, earn prize money, and potentially participate in the accelerator program. xTechInternational offers an opportunity for eligible participants to pitch novel technology solutions directly to the DoD.”
Meltio worked with their US distributor, Phillips Corporation, to participate in the xTechInternational program, which had a theme of “advanced manufacturing and materials” this year. Apparently more than 300 companies participated this year, coming from many different countries. Evidently Meltio was the first Spanish company to ever be selected from this program for additive manufacturing.
Meltio explained further:
“This award consolidates Meltio’s relationship with the U.S. Army and increases its possibilities of having a relationship with other U.S. defense departments and also with armies of other countries.
Meltio’s goal is to become a technological reference in 3D printing of metal by welding wire (known as DED, directed energy deposition for the creation of metal parts layer by layer by laser fused deposition).”
The US Department of Defense explained their decision:
“This is a technology with a very robust capability for fabrication and for near net shape part production. It offers a very valuable approach that uses standard welding wire that is already available in U.S. Department of Defense manufacturing environments, a coil of wire can be made into a near net shape for any part, thus avoiding the need for large stocks of shapes/forms/sizes of raw material.”
This is not surprising, as DED would be one of the more useful additive manufacturing processes that can be used for military purposes. Most other metal 3D printing processes have constraints involving stability, gravity, etc., and would not be as easy to implement in environments typically found in the military.
This is particularly evident on ships at sea, which are subject to constant motion. A bed of powder would not be stable in such a situation, suggesting that DED could be a better solution.
The DoD is aware of this , and in fact they are already performing tests of Meltio’s products shipboard on the USS Bataan. One can imagine the Meltio DED system being able to continue printing with accuracy even as the ship tilts slowly from side to side.
For Meltio, this could be a significant breakthrough. We have previously seen interest from the military in other non-LPBF metal 3D printing systems, and it seems that Meltio has joined the party.
Via Meltio