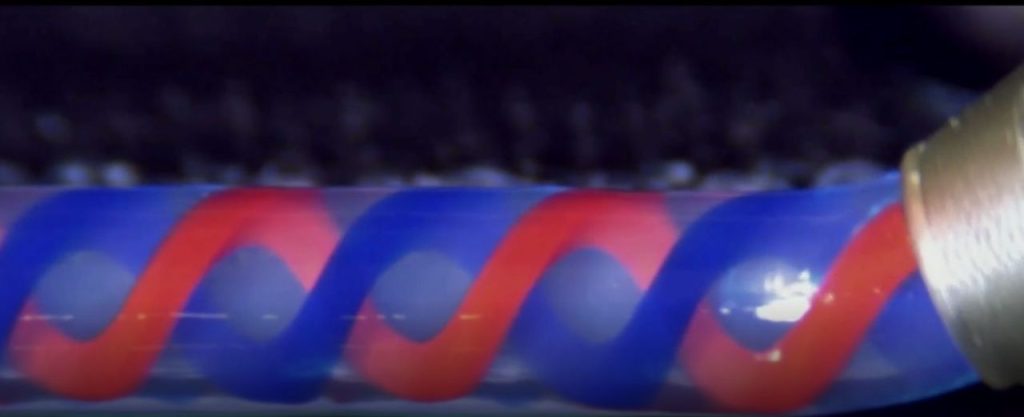
Researchers from Cambridge have developed a new form of 3D printing called Rotational multimaterial 3D printing, “RM-3DP”.
The print results of RM-3DP are probably best explained by looking at the image at top, where you can see they’ve somehow managed to extrude four different materials simultaneously into a helical pattern.
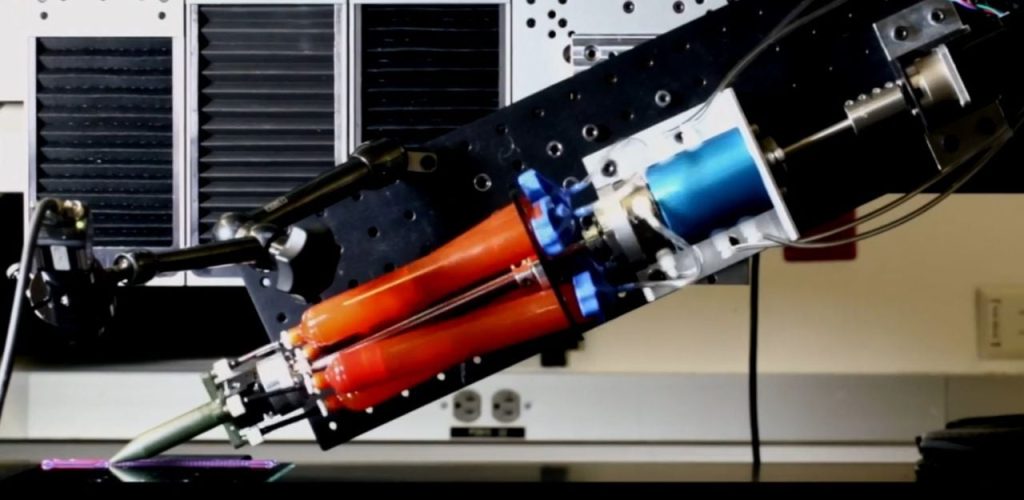
At first I thought this was an interesting, but likely a niche area: who needs to print helixes?
But then I started reading the paper and realized there are countless applications for this form of 3D printing, and likely many more that haven’t yet been discovered.
Helical structures are present everywhere, if you know where to look. Examine a typical cable, and you’ll find several different “filaments” that are wound together with a precise rotational angle. That’s a helix. Other common applications would be ropes and springs.
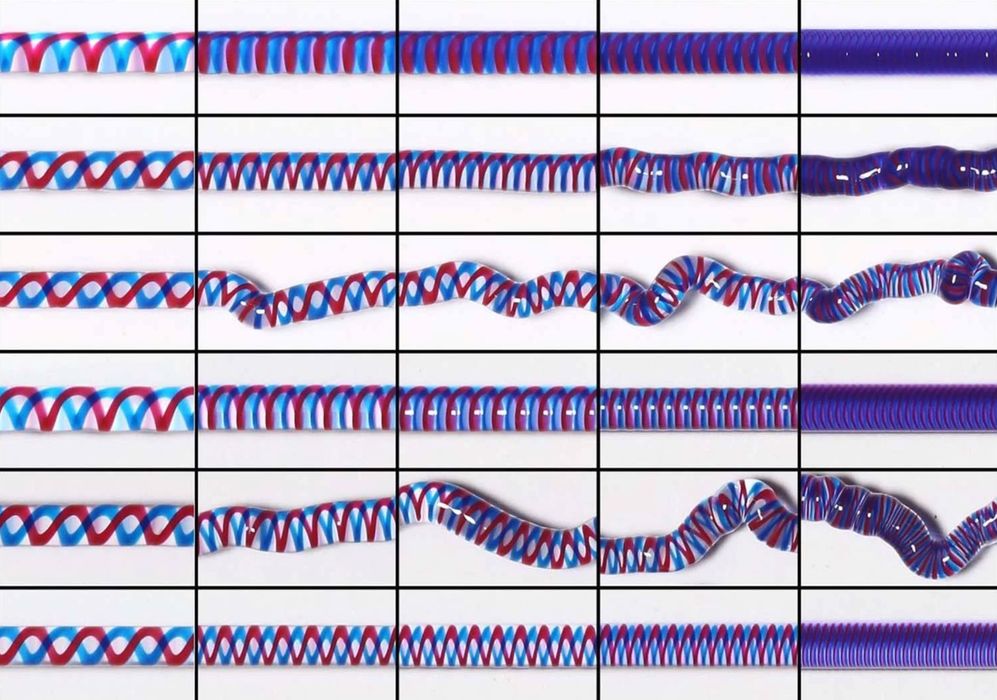
But all of those have one thing in common: they use a standard material throughout the length of the strand. This is where RP-3DP differs, as it apparently has the capability to control the extrusion not only on a rotational and angular basis, but also on a “sub-voxel” level. They write:
“Here we report a rotational multimaterial 3D printing (RM-3DP) platform that enables subvoxel control over the local orientation of azimuthally heterogeneous architected filaments.”
Their approach was to construct a specialized multimaterial nozzle that was able to control the angle of extrusion, while simultaneously rotating at a specified RPM. They explain:
“By continuously rotating a multimaterial nozzle with a controlled ratio of angular-to-translational velocity, we have created helical filaments with programmable helix angle, layer thickness and interfacial area between several materials within a given cylindrical voxel. Using this integrated method, we have fabricated functional artificial muscles composed of helical dielectric elastomer actuators with high fidelity and individually addressable conductive helical channels embedded within a dielectric elastomer matrix. We have also fabricated hierarchical lattices comprising architected helical struts containing stiff springs within a compliant matrix.”
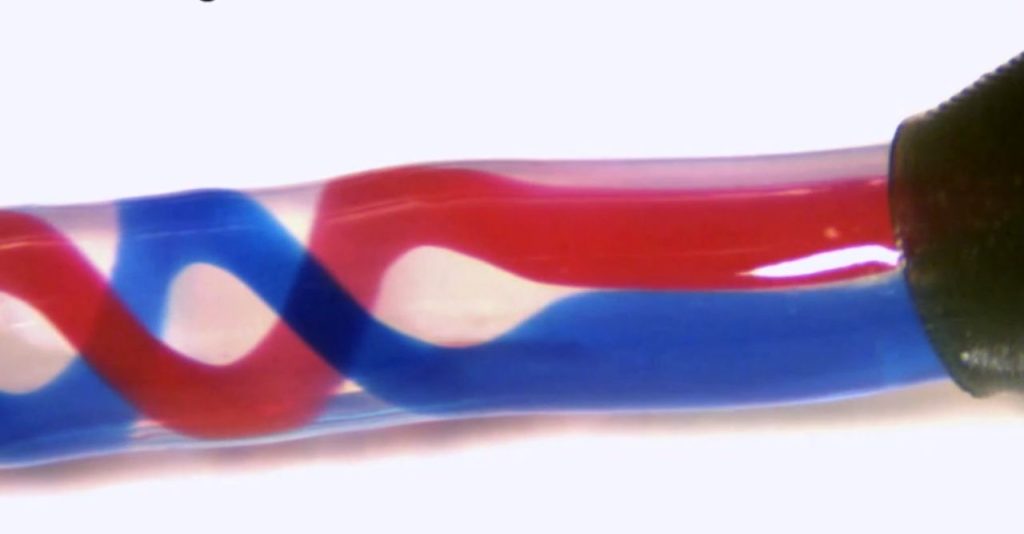
Here you can see how this works in action, as they’ve actually changed the angles of extrusion during a print job, resulting in the change in structure. You can see how this is very different than simply winding wires together.
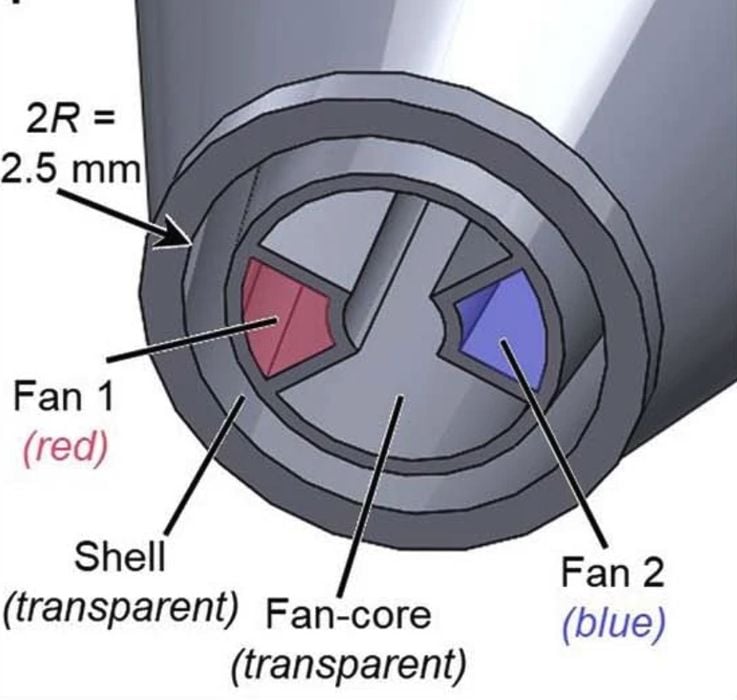
Their design involves this rotatable nozzle, which as you can see has four points of input for material, with a single complex nozzle, shown below. Imagine this spinning while splurting material on each tip.
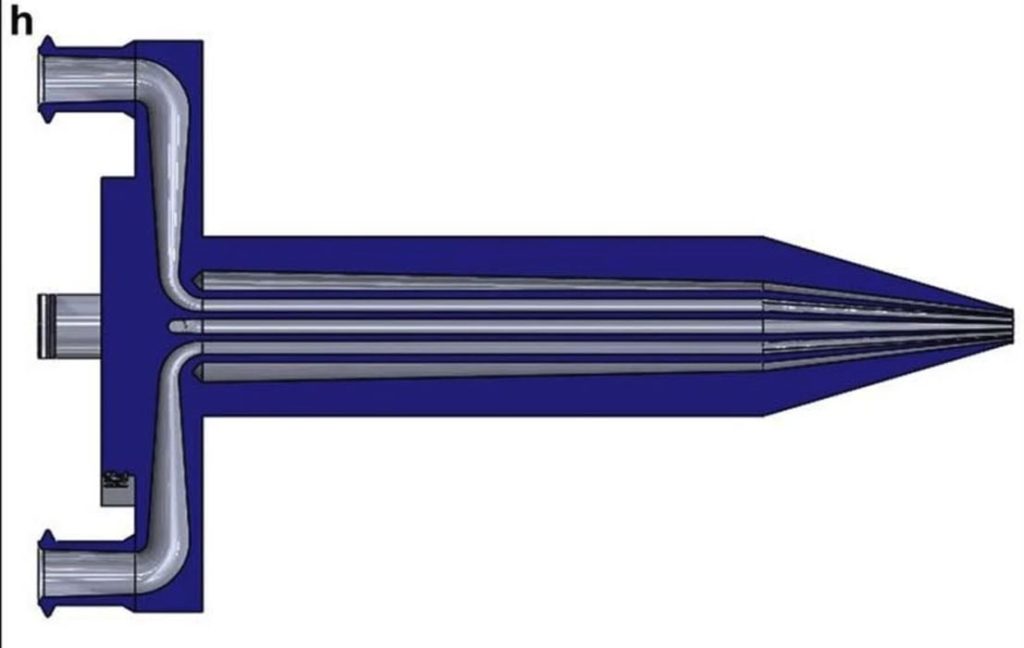
After extrusion, it appears that the materials are polymerized by an appropriate dose of UV radiation, as is commonly done in many resin-based 3D printers. Here you can see sample extrusions, and the UV light source following along.
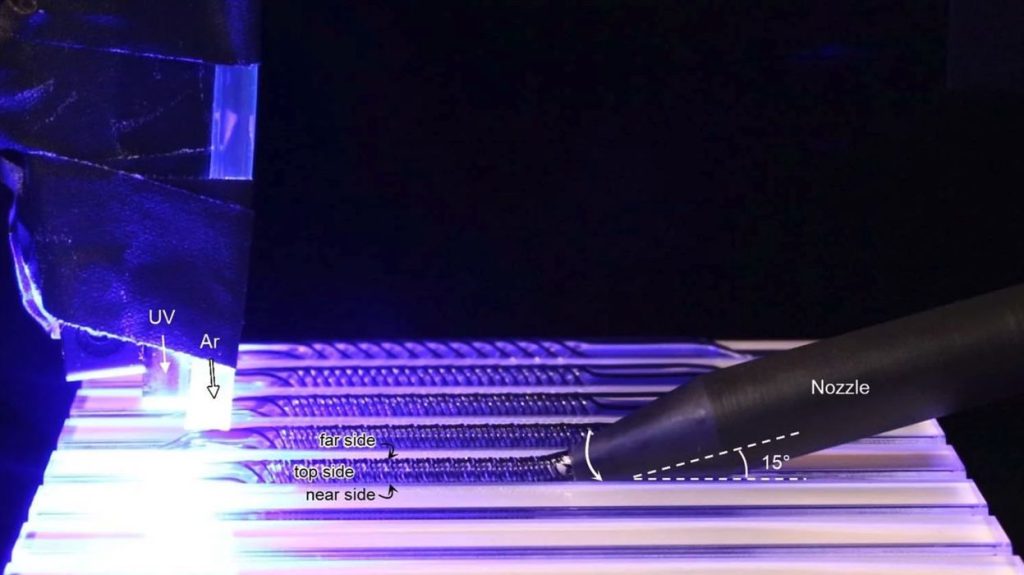
It’s pretty clear the researchers are using a gel-style resin, which as has been done by many other resin systems, could be made with all kinds of different properties. These might include conductivity, flexibility, strength, optical capability, etc.
It is also possible to layer these helical extrusions as seen here. This suggests it would be possible to 3D print very strong fabrics, perhaps even with embedded conductive elements.
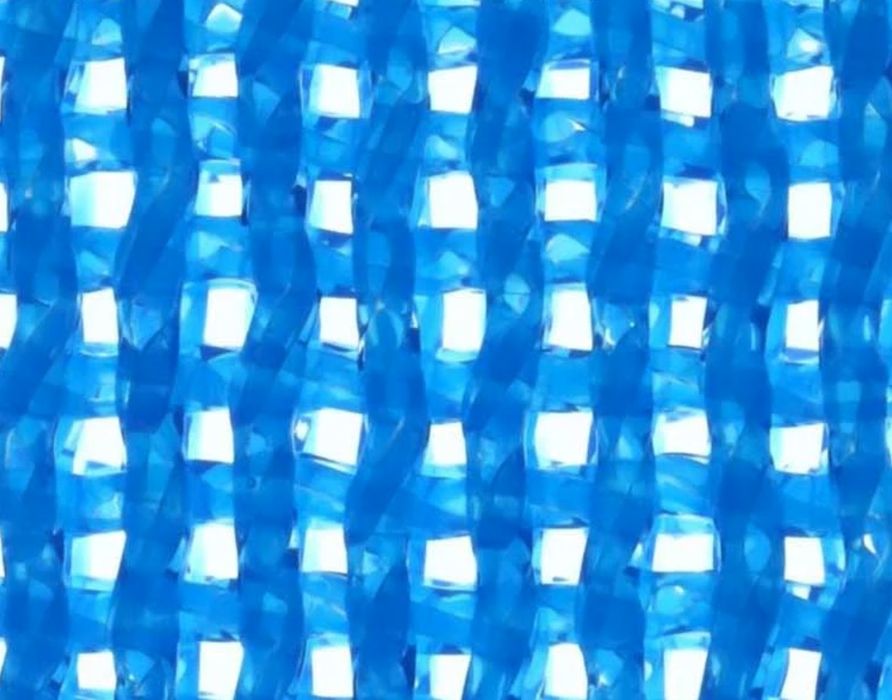
There may be questions about the materials available with RM-3DP, but my thought is that a company commercializing this tech would essentially open up a large, unexplored material space ready for innovations. Start with the basic material and then expand over time.
This is a unique technology that the industry has not seen previously, and opens up many possibilities. To that end, the process has been patented, so you can be sure there’s a startup company ready to emerge shortly to exploit this process.
The final word is to the paper’s authors, who write:
”Our additive-manufacturing platform opens new avenues to generating multifunctional architected matter in bioinspired motifs.”
Via Nature (Hat tip to Tuan)