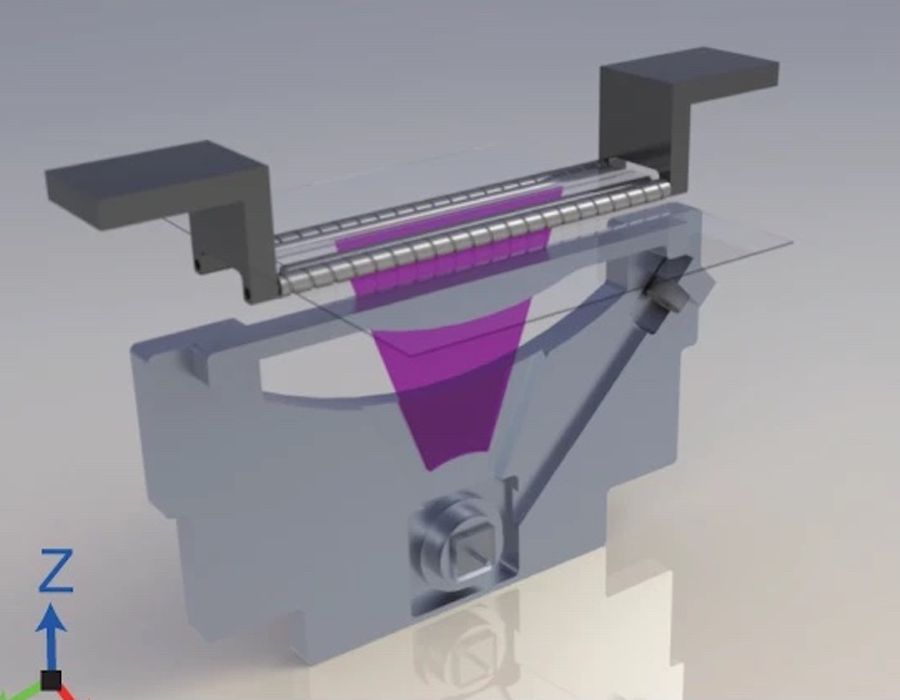
Researchers have developed a new 3D print process “LSVP”, which can apparently handle highly viscous resins.
Viscosity is one of the key barriers to the expanded use of resin 3D printing. While for a time the biggest problem was the duration of the peeling process between layers, that has been resolved by several companies that reduced or eliminated that problem entirely.
Carbon, for example, uses an oxygen-permeated film to prevent adhesion of resin to the tank during curing, thus making it possible to print near-continuously without layer delays.
But when one barrier is breached, there are others. Even though peeling may be more-or-less solved, the next big issue is viscosity.
As a partial print is raised during a resin print, fresh resin must flow into the space occupied by the previous cured layer. This is normally by simply waiting for the resin to flow into those spaces, powered by gravity.
This works well — if the resin is not viscous. If the resin is viscous, it could take a very long time — or forever — to have it flow into the vacated spaces. Because of this all 3D printer resins have low viscosity, and usually have agents mixed in to dilute the viscosity.
The problem is that viscous resins are highly desirable. Most commercial resins used in non-3D print applications are viscous, and using them in 3D printing would be a goal for many.
It’s just that it can’t be done. Apparently researchers have already shown that with current resin 3D print technology, the maximum viscosity for 3D printing is 5000 cPS (centipoise), but most resins are far less than that.
Some approaches, such as those used by Lithoz’s ceramic devices, can print somewhat higher viscosity resins. However, none can reach the levels where commercial resins can be generally used.
Until now.
The researchers developed a unique 3D printing process they call “LSVP”, or “Linear Scan-based Vat Photopolymerization”.
LSVP involves using a set of rollers and a FEP film. The viscous resin is applied to the ongoing print by sliding the film along the rollers, whereupon the laser fires between the rollers to selectively fuse the resin.
The resulting LSVP system was able to handle resins of far higher viscosity, and the researchers say in theory it could be used up to 600,000 cPs, which is quite incredible.
The system involves a laser and a prism rotating at 16,000 rpm. Light bounces off the prism, and then through a corrective mirror that ensures light rays are perpendicular to the print surface.
LSVP doesn’t scan the entire print surface as is done in MSLA, nor traces a path as does SLA, but instead scans repeated straight paths along the print surface. This is why it’s called “Linear”.
The design of the system also dramatically reduces any forces on the partial print, something that messes up some other approaches as the resin viscosity increases.
This is a very promising approach that could eventually be commercialized. However, due to the nature of the LSVP system design, it is likely to be a fairly pricey solution. The requirement for a laser, precision corrective mirror and perfectly timed rotating prism to me signals extra cost over today’s resin 3D printer designs.
However, that may be a cost some are willing to pay in order to gain access to a far wider array of resin materials for 3D printing.
Via Nature
This is already exactly how the Formlabs Form 3 printer works. I’m sure it’s patented.