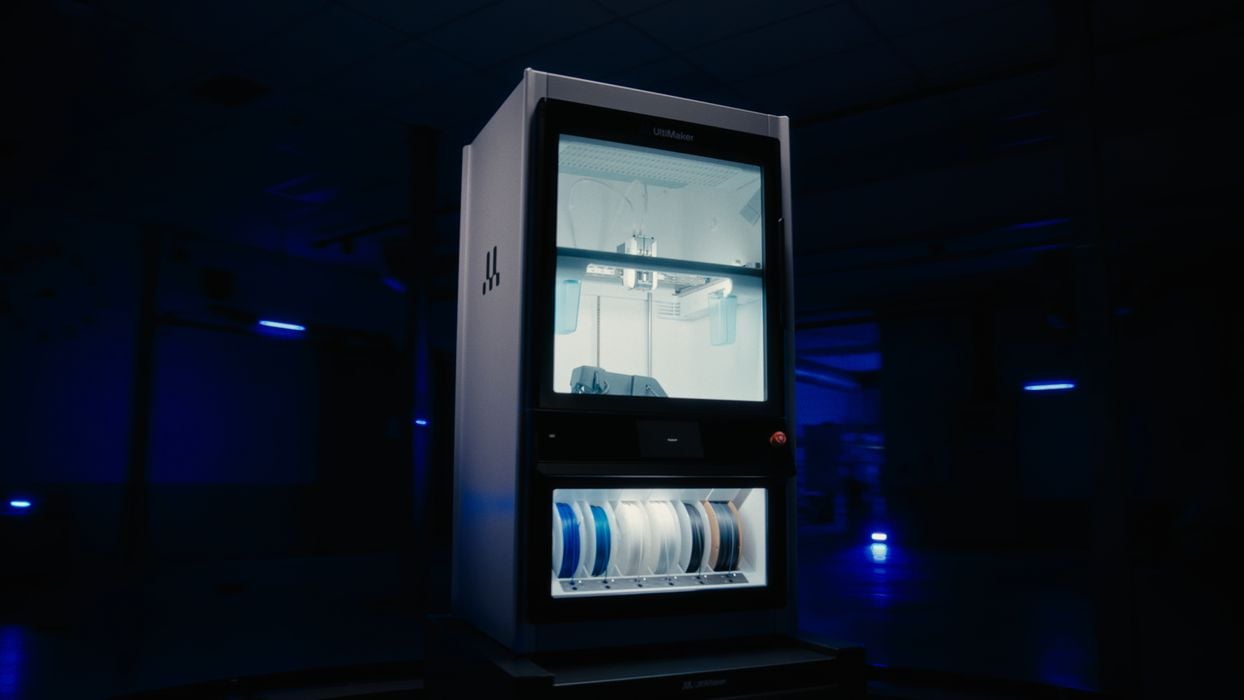
UltiMaker today announced a new flagship 3D printer, the Factor 4.
The company has focused on industry ease-of-use and quality aspects for the past few years, and the Factor 4 seems to follow that pattern. They describe it as: “Industrial 3D printing, reliable and repeatable results.”
The word “repeatable” is probably the most important of this announcement, as that seems to be what UltiMaker is trying to achieve. Repeatability is extraordinarily important for many regulated industries, where parts absolutely must be identical — within tolerances — regardless of which specific machine produced them.
But let’s take a look at the Factor 4 itself.
It’s a dual extrusion FFF device with a huge build volume of 330 x 240 x 300 mm. The print core is able to reach 340C, implying the possibility of printing in a wide variety of engineering materials, including abrasive composite materials like carbon fiber-reinforced filament.
The Factor 4 still uses 2.85mm filament, and UltiMaker is perhaps the last major 3D printer manufacturer to do so.
UltiMaker has engineered the Factor 4 to be quite precise. They say parts produced on the machine will be within 0.2% of nominal part length, which should be good enough for many production applications.
The visual appearance of the Factor 4 is reminiscent of the company’s “Bundle”, which combined the 3D printer with a filament storage/switching unit. Here the Factor 4 integrates all that together into a single unit.
The system is designed to be operated entirely from the front, with no need to access the side or back of the device. This opens up the possibility of placing multiple Factor 4s in a row, side by side. This should save floor space and enable low volume production to take place more efficiently. In fact, the Factor 4 includes the standard red “STOP” button seen on factory equipment.
The now-integrated material handling system can accommodate up to six spools, and maintains proper environmental conditions for optimal 3D printing. Humidity levels are kept below 15%, so the filament is guaranteed to be very dry.
As you might expect, the Factor 4 is directly integrated into UltiMaker’s wide materials ecosystem. From UltiMaker Cura, operators can directly access print parameters for a wide variety of third party materials and ensure print success. The company suggests the Factor 4 has “95% print completion success”.
UltiMaker said at launch the Factor 4 will immediately support UltiMaker-branded materials, including PPS-CF, PLA, Tough PLA, nylon, PETG, PET CF, and PVA. As this is a new machine, it may take a bit of time for third party material producers to develop their own Factor 4 print parameters to integrate into the system.
One very interesting feature is a print process report that can be automatically created at the end of each print job. This report provides insights into the job based on data collected from the considerable number of sensors on the Factor 4. This could be of interest to those producing end use parts as a means to ensure consistent part quality.
The Factor 4 seems to be targeting industry with a package of features that seems quite attractive. Customers will be able to reliably build strong parts in a variety of materials and expect consistent results across their Factor 4 farms.
Via UltiMaker