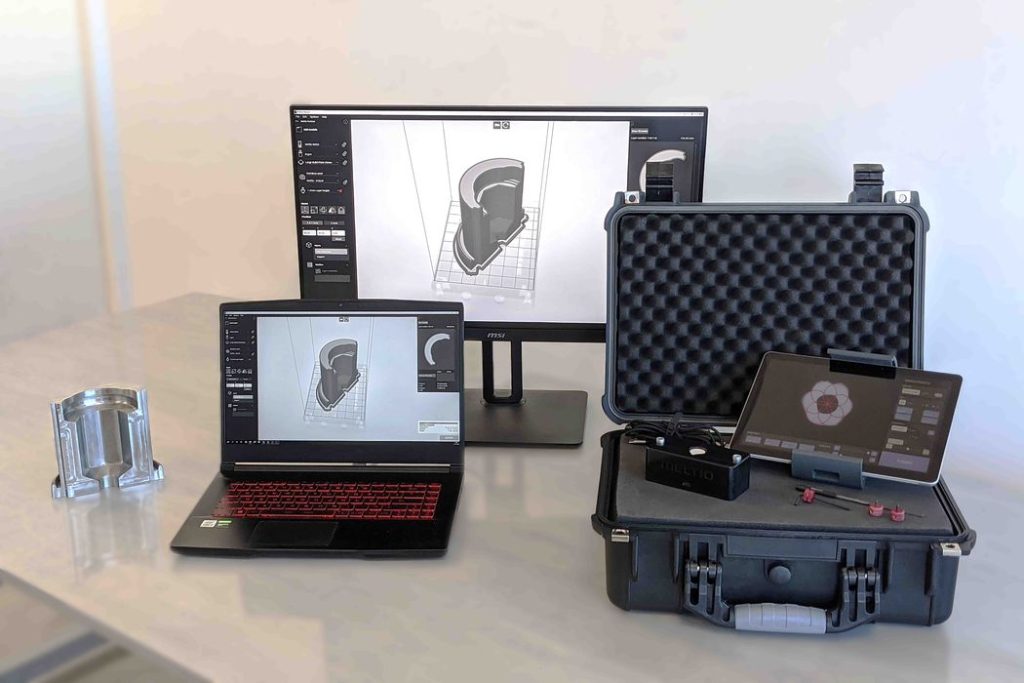
Meltio has introduced two new innovations: “Horizon” slicing software and a laser calibration system.
The Spanish company produces metal 3D printing equipment that is easier to operate than most typical LPBF metal 3D printing systems. While other systems tend to use toxic, explosive and expensive metal powder as material, Meltio’s solution involves wire that can be easily handled, purchased and used.
This technology immediately eliminates the need for much of the expensive safety systems required for powder-based metal 3D printers.
Because of this, Meltio’s 3D printers are quite suitable for metal production operations with less ability to dedicate resources to the technology, and that’s quite a large market.
Now, Meltio has developed two new innovations that should complement their products in that market.
Meltio Horizon
The first innovation is new job preparation software, called “Horizon”.
The easy-to-use software includes the usual job preparation features, but also includes settings related to Meltio’s wire additive manufacturing system.
Horizon also includes a feature to compute the true cost of each print job. This will be incredibly useful to customers, many of whom will be using additive technologies for the first time and might have issues computing costs without such guidance.
Meltio has merged material profile information to be centralized on the slicer, whereas previously there were some settings that would have had to be done on the printer itself. Now it’s all in the software and much easier to access and use.
Because the Meltio system allows the use of differently-sized metal build plates, Horizon is now able to handle these configurations. It adjusts the build volume in the slicer to match the assigned build plate.
There’s many more features, and Horizon also now updates itself to the current version automatically. This includes release of new pre-made print profiles, which could be quite useful.
Laser Calibration
If you’ve ever used a laser system of any kind, you’ll know that the laser must be calibrated precisely. This is because the energy from the laser is typically focused to a point where energy levels are sufficiently high to cut material, or in the case of wire additive manufacturing as used on Meltio’s systems, melt the metal.
Meltio’s calibration is a bit more complex as their technology is not just one laser, but SIX! These six laser must each be focused and then aligned on the same spot to ensure maximum energy.
Meltio has simplified the process of calibration with a new laser calibration kit.
The kit is composed of a special camera, which is placed by the laser and provides a “clear view of the laser focus point”. This view then greatly simplifies the calibration as the operator is able to see instantly the results of an adjustment.
This should not only increase print quality on Meltio machines, but also avoid inefficient use of energy: misaligned lasers would not melt the metal as effectively.
What’s quite interesting about this calibration is that apparently the system tracks the adjustments. This allows the operator to “back up” if adjustments go wrong, and also the ability to consistently adjust the lasers, ensuring part consistency.
These are two excellent improvements to the Meltio system.
Via Meltio