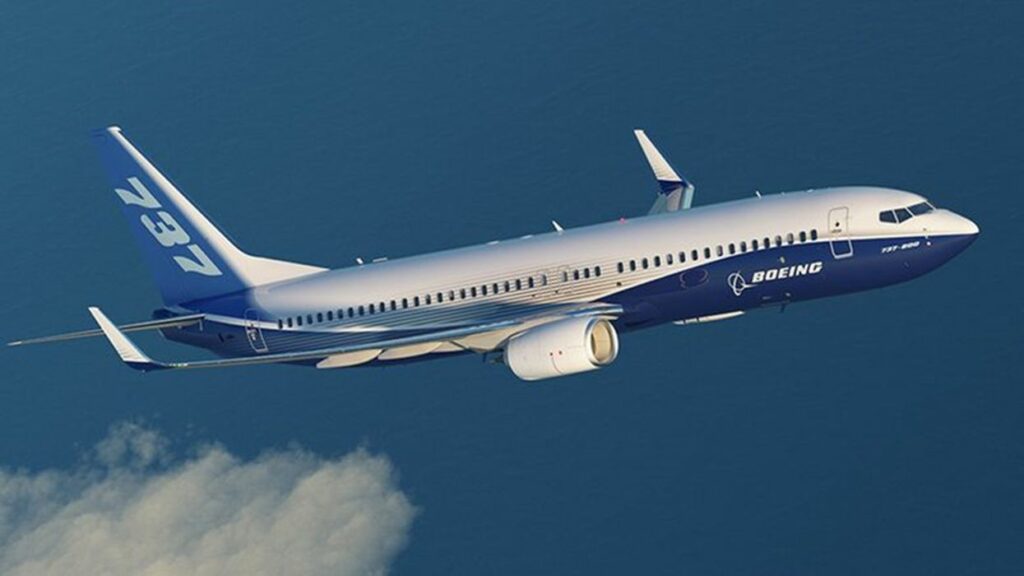
Charles R. Goulding and Julia Wallace look at Triumph Group’s investment into 3D printing technology for aerospace.
Triumph Group is in the late stages of its “Path to Value” reconstruction plan, which began in 2016 to reduce risk and increase financial stability by divesting some of its locations, and plans to soon transition toward a period of growth.
The company has also committed itself to lowering its carbon footprint, publishing its first ESG report along with its 2021 annual report. In this, the company reported net sales of US$1.87B and a 25% increase in sales to the military end market, offsetting the decline in commercial, business, and regional sales that resulted from the COVID-19 pandemic.
The parts manufactured are largely sold to Boeing, which has a history of working with supply companies that use 3D printing technology
3D Printing at Triumph
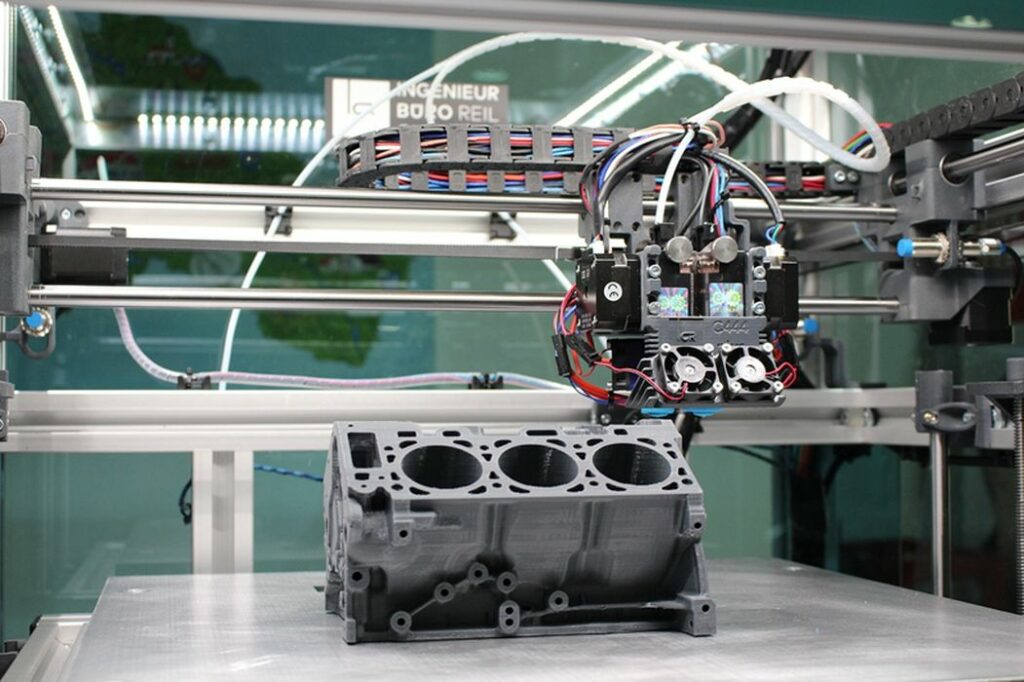
Part of Triumph’s plan to lower its environmental impact and cost is the use of its Additive Manufacturing Center of Excellence. Here, parts for aircraft are 3D printed, rather than machined, out of metal. This way of production discussed and demonstrated in Episode 20 of the Fox Business show “EARTH with John Holden,” allows the pieces to be lighter, less expensive, and more efficiently made.
The weight decrease has greater implications, as well. As explained in the show by Brian Sitt, division head for sustainment technologies at the University of Dayton Research Institute, for each one-pound gain in the weight of an aircraft, gallons more of fuel is needed per flight, and over 11 tons of CO2 emissions are emitted in that aircraft’s lifetime. These lighter parts, made possible by Triumph’s 3D printing, would reduce those emissions.
The company is actively doing research on additive manufacturing in hopes of completely transitioning to this method of production in order to be more environmentally friendly and fuel-efficient. As Triumph’s chief administrative officer Jennifer Allen explains, they are committed to working with their customers to find innovative solutions to increase aircraft efficiency and decrease aircraft weight, which in turn causes fewer emissions. Triumph also works with a large network of additive manufacturing suppliers.
The Research & Development Tax Credit
The now permanent Research and Development (R&D) Tax Credit is available for companies developing new or improved products, processes and/or software.
3D printing can help boost a company’s R&D Tax Credits. Wages for technical employees creating, testing and revising 3D printed prototypes can be included as a percentage of eligible time spent for the R&D Tax Credit. Similarly, when used as a method of improving a process, time spent integrating 3D printing hardware and software counts as an eligible activity. Lastly, when used for modeling and preproduction, the costs of filaments consumed during the development process may also be recovered.
Whether it is used for creating and testing prototypes or for final production, 3D printing is a great indicator that R&D Credit eligible activities are taking place. Companies implementing this technology at any point should consider taking advantage of R&D Tax Credits.
Conclusion
The increased use of 3D printing in part manufacturing by Triumph Group has great implications for both cost and environmental impact. We expect that Triumph will increase its use of this technology as they continue to work with Boeing and both businesses begin to regrow their companies.