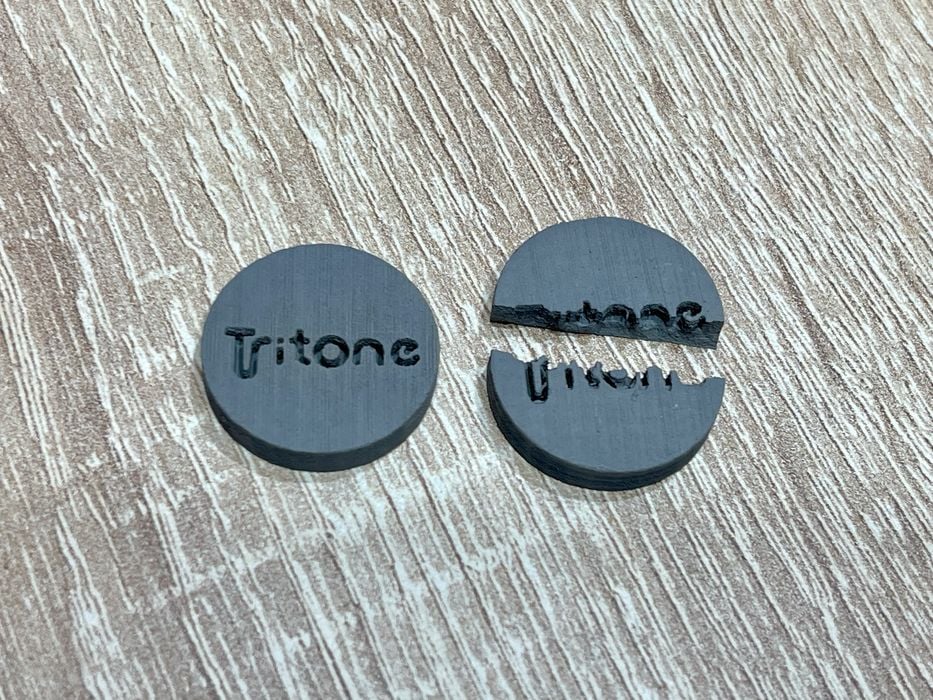
I spoke with Tritone and caught up with their latest developments.
The company’s MoldJet process is quite different from other 3D printing approaches. Instead of 3D printing the object directly, they are printing a mold — but at the same time they fill the mold.
As each layer is deposited, there is a portion that’s “mold” and another portion that’s “model”. The model material can be any standard MIM (metal injection molding) powder. The mold material is designed to hold the MIM powder in place until it’s sintered together in a post processing step. No support structures are necessary.
The implication is that the Tritone process is able to produce objects made from almost any MIM powder, vastly increasing the variety of materials possible. This is quite different from most 3D printing processes, which have very constrained sets of possible materials.
The green parts printed by the process are surprisingly strong; most green parts are extremely fragile and must be handled quite delicately.
Not so with Tritone’s green parts. At top you can see two green parts printed by Tritone. I was just barely able to break the one on the right with considerable force. They’re not kidding when they say the green parts are strong.
This does have some production implications: it would be far easier for operators to handle batches of green parts made with Tritone’s process.
We first encountered Tritone several years ago as they first introduced their powerful technology. But what’s happening these days?
It seems that the company is through the development stage and now focuses on sales. This is a critical stage for tech companies that have developed a solution. It is important for them to identify a specific focus market to drive sales.
In this case it seems that the jewelry industry is where Tritone’s business may be heading. That industry produces many small metal parts in a wide variety of materials.
There’s also the consideration that by and large, jewelry cannot make use of traditional mass manufacturing techniques. It would seem that they now can using Tritone’s equipment.
Applications could include high end watch components, but Tritone representatives mentioned they’ve also seen their technology used for mass producing shoes with titanium, and certain medical applications.
They’ve also seen applications with ceramics, which is also possible with their technology. We were told that Tritone is willing and able to work with customers to develop new materials or certify usage.
It seems to me that Tritone has a unique package of benefits that would certainly appeal to several specific industries. It may be that they can transform some into larger-scale mass manufacturing scenarios.
Via Tritone