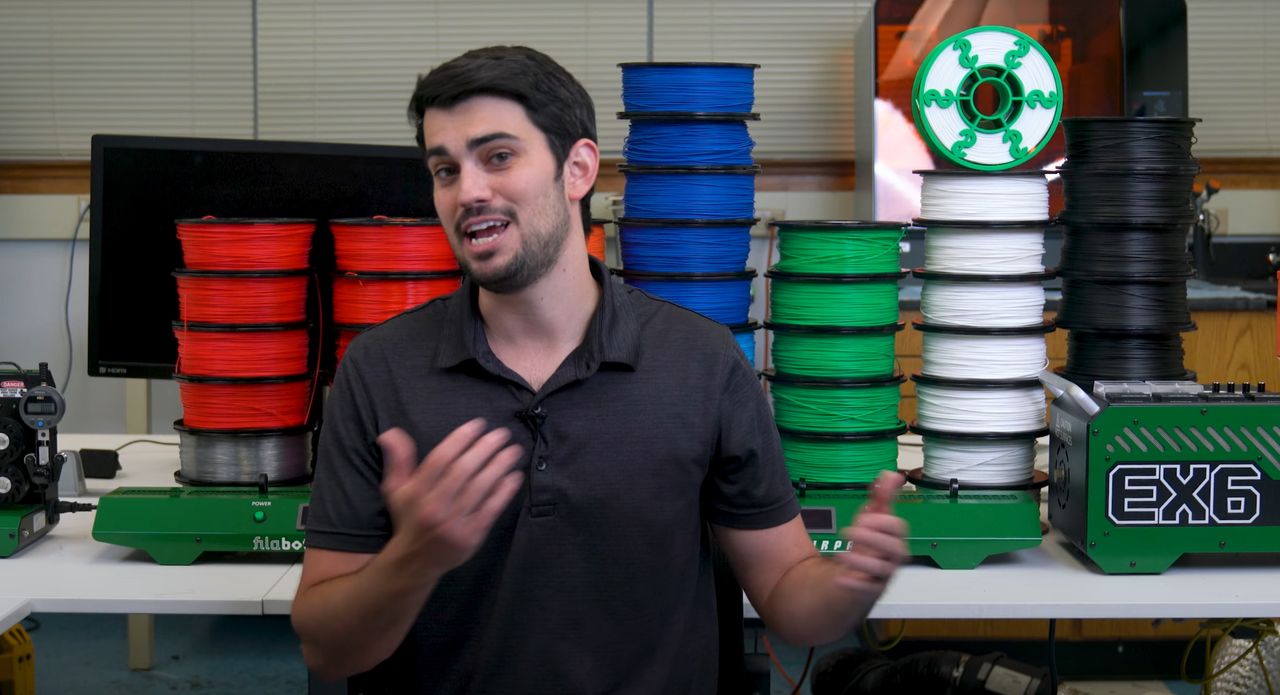
Making your own filament is easy. Isn’t it?
The truth, unfortunately, is that filament production is anything but simple.
On the surface the making of filament may seem straightforward, with these steps being imagined:
- Chop up some plastic or buy pellets
- Feed them into a unit that melts the plastic
- Extrude the plastic through a circular nozzle
- Wind it up on a spool
- Profit!
You could do this — and some early desktop filament-making systems did — but you’d fail miserably.
The problem is that today’s FFF 3D printers require highly consistent input material. Consider that the slicing parameters are calculated based on the amount of material coming through the extruder. 3D printers spend considerable time dialing in their parameters to ensure the prints are perfect.
However, their tuning depends utterly on the quality of the filament. By “quality”, I mean having a consistent diameter and cross sectional shape.
Imagine if the filament varied in diameter as it passes through the extruder. If it’s suddenly wide, you’d get a splurt of extra material at the nozzle, just as if the flow rate was momentarily bumped up. Correspondingly, if the filament became thinner, it would be as if the flow rate was decreased intermittently.
None of that leads to good quality 3D prints.
The key is to make the filament ultra-consistent, and filament diameter is not something current 3D printer can detect. They simply assume it’s all the same diameter and use it as such, for good or evil.
How does one make filament ultra-consistent? It takes a bunch of equipment, considerable tuning and a lot of patience. Systems always include a method of cooling the hot, freshly extruded filament slowly to ensure it maintains its shape. This is typically a very long water bath kept at a specific temperature. The exposure to this water also implies that the filament must be dried out later on in the process.
Most filament production facilities will have multiple laser diameter measuring devices set up as the filament comes out of the extrusion line. Through a feedback loop, the production system’s parameters (temperature and extrusion speed) are slowly dialed in to achieve a consistent diameter.
Once that’s done, the production facility will ram through massive quantities of pellets to produce as much as possible using the determined parameters. Filament produced will be initially captured on large spools, but then later dried and re-spooled onto smaller spools for sale.
Can all this be done on a desktop system?
Possibly. There have been many attempts at making desktop filament production devices, and most have failed for one reason or another. The failures have been both technical and in some cases financial — if you can’t produce spools at less cost than buying them commercially, then why do it at all?
Two companies producing desktop filament production gear that seem to have survived are 3devo and Filabot.
3devo’s market niche is for those interested in making unusual filaments that are not on the market, typically for experimentation. It’s hard to compete against large manufacturings that can leverage economic scale.
I recently watched a very interesting video explaining the Filabot system by David Florian, a.k.a. “Dr. D-Flo” online. Florian’s 35 minute video goes into considerable detail explaining the ins and outs of filament production, and it’s way more complex than you could ever have imagined.
If you watch the video, you’ll see there are vastly more things to worry about than just temperature and extrusion speeds. For example, as the screw pushing pellets turns, friction and pressure can generate considerable heat on their own, messing up the thermal profile of the material as it passes through the system.
After watching this video, I think you’ll gain a new appreciation for the complexities of 3D printer filament production.
And it will likely remove any possible motivation you had previously to make your own filament.