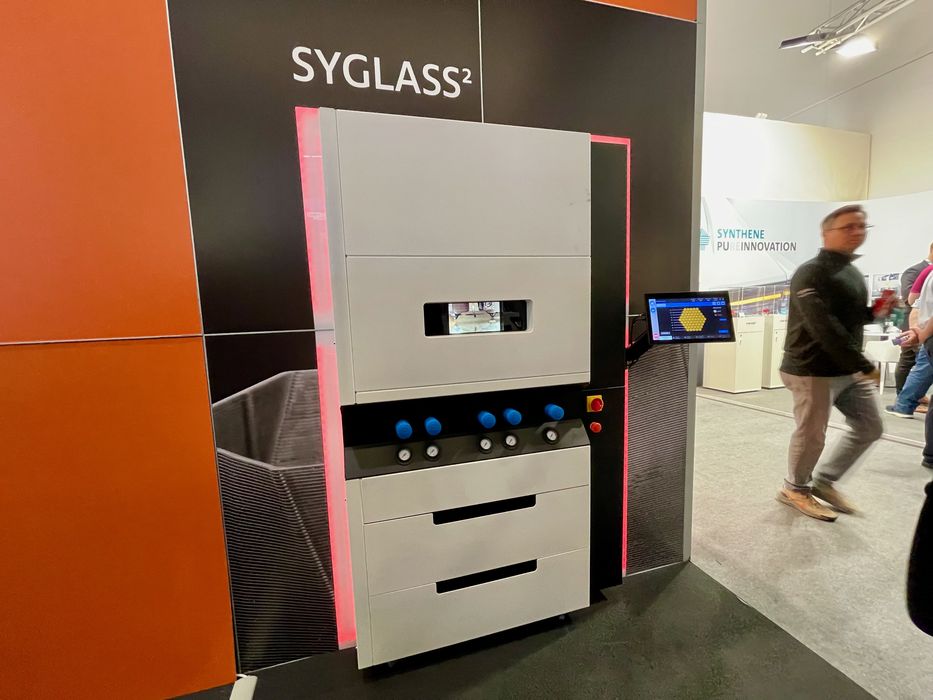
After looking at the SYGLASS2 3D printer from Sygnis, I am astonished at what it can 3D print: kilometers of optical fiber.
First of all, glass 3D printers are not a common thing. Glass is a notoriously difficult material to 3D print: it requires extraordinarily high temperatures to soften, and even then it is extremely viscous and quite difficult to form objects.
We’ve seen a few attempts to 3D print glass material in the past, but none have been particular successful. Perhaps the most interesting in recent years has been Glassomer’s glass resin that can be used to print small pure glass objects.
SYGLASS2, however is quite different. It’s a real 3D printer that prints glass. The company produced what they call the “world’s first low temperature glass 3D printer”, the SYGLASS_01. Now they’ve come up with the SYGLASS2.
The system uses a high-temperature syringe, which is heated to an astounding 1000C. Then, an air pressure-powered piston pushes the molten glass out through a nozzle for deposition.
The build chamber of the SYGLASS2 hits an amazing 600C, perhaps the highest build chamber temperature I’ve ever heard of.
How can this work? It turns out that Sygnis is using a special low-temperature glass, which seems to be the secret sauce of this technology. It’s said to be a mix of pure glass an “other compounds”, knowable only under NDA. The lower temperatures allow the system to properly extrude strands of molten glass.
The thin nozzle can lay down strands of glass as designed in their software to form 3D objects.
I asked what type of objects would be made with such a system, and was told, “fiber optic cables”.
Hold on, fiber optic cables are tremendously long items that vastly exceed the build volume of any 3D printer. How could they be made in the SYGLASS2?
It was explained that they simply print a small 5-10cm block of glass with fibers aligned along the long axis, as shown in this image.
These blocks, which contain a large number of thick strands, are then taken to other equipment that’s designed to make fiber optic cables. Basically this block is heated and then slowly stretched to enormous lengths by the other equipment, and spooled up for use.
In the image you can see the beginning of this process, where the glass is being stretched.
I asked how long a cable could be made from this small block, and, after some calculations, was told 1km, or 1,000 meters. This enormous distance was verified afterwards by Sygnis representatives. This enormous length is possible when stretching glass cores of only 0.01mm diameter, which is quite incredible. Who else can print a 1km cable on their 3D printer?
This is an incredible achievement, something I’d never have expected to emerge from a 3D printer.
Wait, there’s more.
Because the printing of the glass starter blocks is under complete control of the designer, it’s possible to develop variations in the strands (which become cables). The strands that are normally “straight” could have their end points scrambled in a unique way.
This provides a measure of physical security, as an attempt to tap into the line would be confused by the layout of the strands. Even better, these could be changed up on each cable segment so that the cable configuration could be constantly unique. This provides security in a non-powered, no-software physical way, rather than using a complex encoding system, for example.
For now Sygnis intends to operate SYGLASS2 as a service, as there are likely not that many clients and it’s so new that potential users may not even realize what is possible with this technology.
Via Sygnis