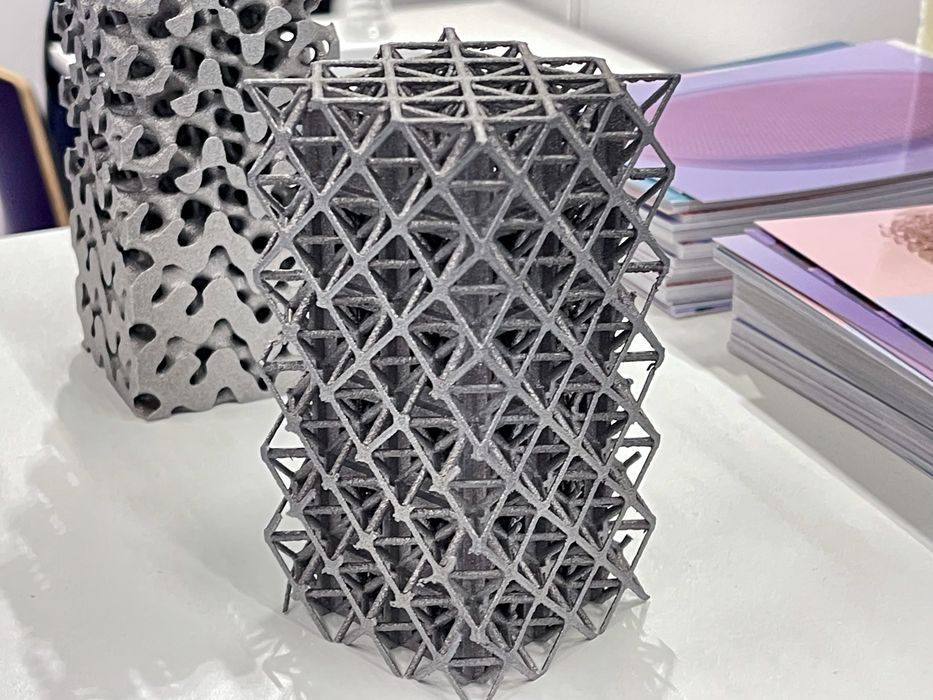
After seeing a great deal of new metal 3D printers recently, it seems that there are new classes of equipment emerging.
For many years “metal 3D printer” meant a LPBF device that could reliably produce small to medium-sized objects. You can still acquire such a device, but today’s metal 3D printer market has branched into a series of different classes. At least that’s what it seems to me, after seeing dozens of metal 3D printers at the recent Formnext trade show.
Let’s take a look at these segments.
Experimental
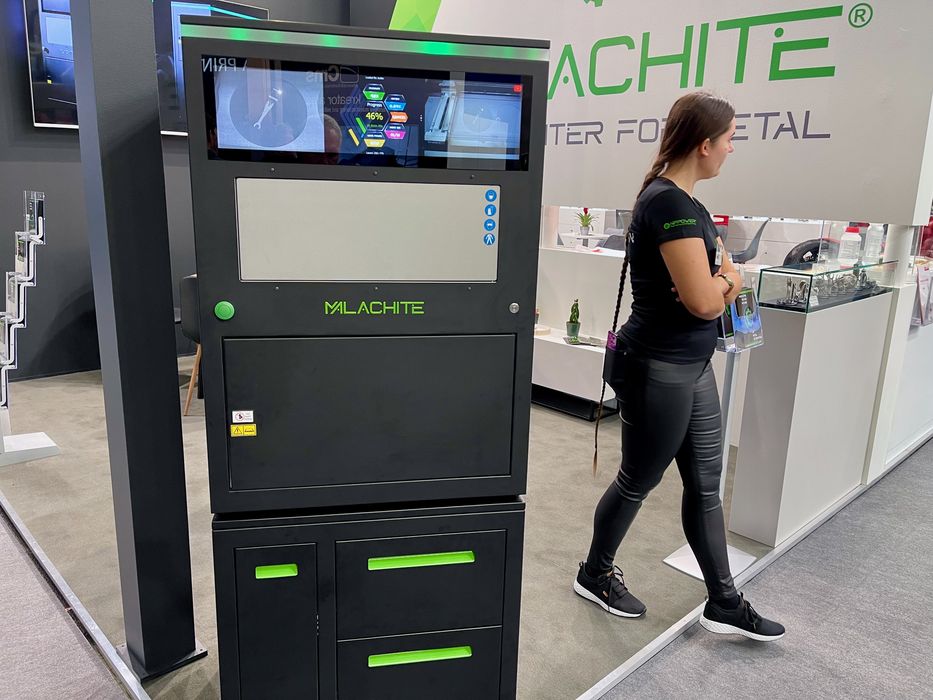
There is a group of metal 3D printers that specifically address the need for materials development, particularly for lab environments and testing configurations.
These machines are characterized by quite small build volumes, sometimes around 100mm. This is done purposely to reduce the expense of experimental metal powder: when you’re mixing up new alloys, you want to minimize the amount used. Testing the alloy doesn’t take much build volume.
Example companies providing this class of equipment: Freemelt, NPPower, Xact Metal.
Small Format
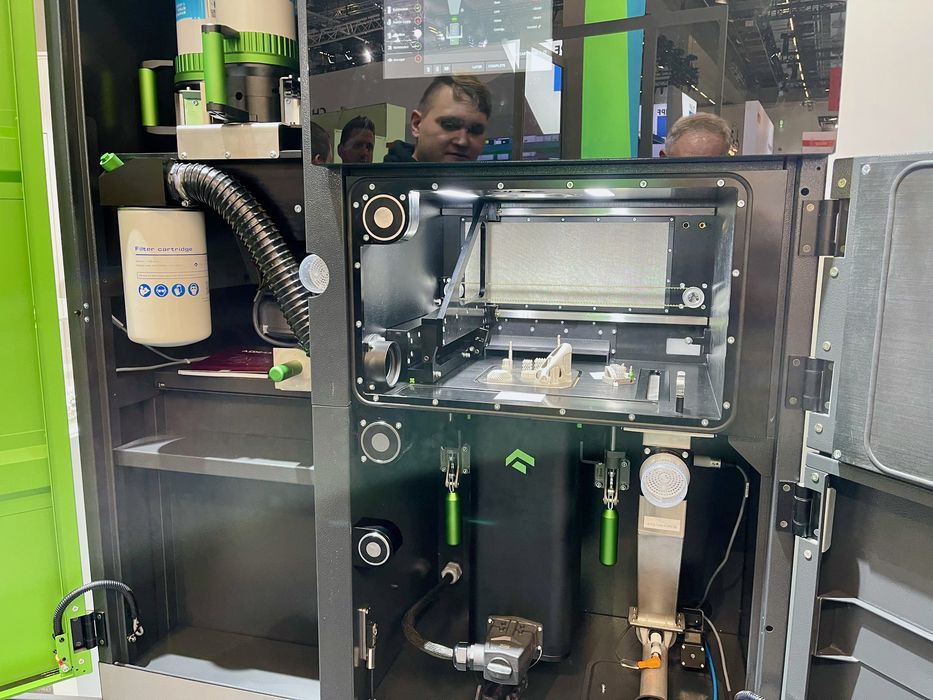
A new class that’s emerging is one with smaller build volumes. These may be smaller than traditional, but apparently offer sufficient space for many companies to produce the parts they need.
Machines in this class tend to have build volumes at or lower than 300mm, but otherwise are much the same as traditional PBF systems.
Example companies providing this class of equipment: Xact Metal, OneClick, Sinterjet.
Traditional
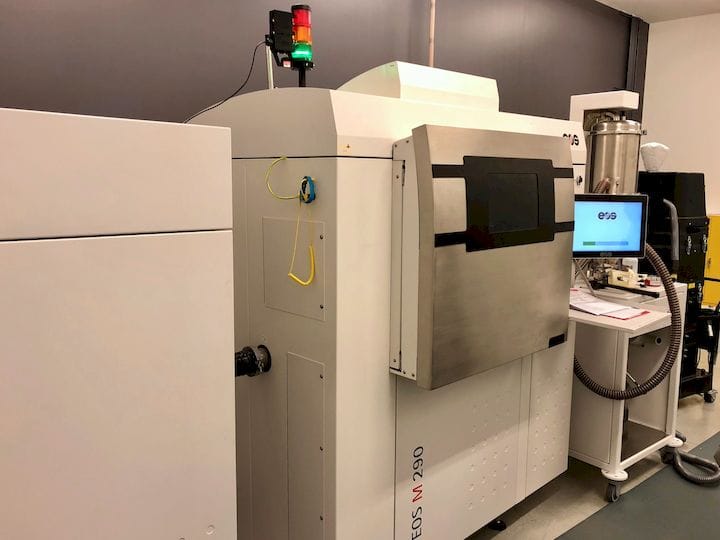
This segment is the granddaddy of the field, with several companies offering PBF equipment in some cases for decades. These are powered by lasers or electron beams and offer build volumes up to 500mm or even more. Typically this type of equipment is used to produce expensive parts for regulated industries such as healthcare or aerospace.
Example companies providing this class of equipment: EOS, Velo3D, SLM Solutions, Farsoon, 3D Systems, and many others.
Massive
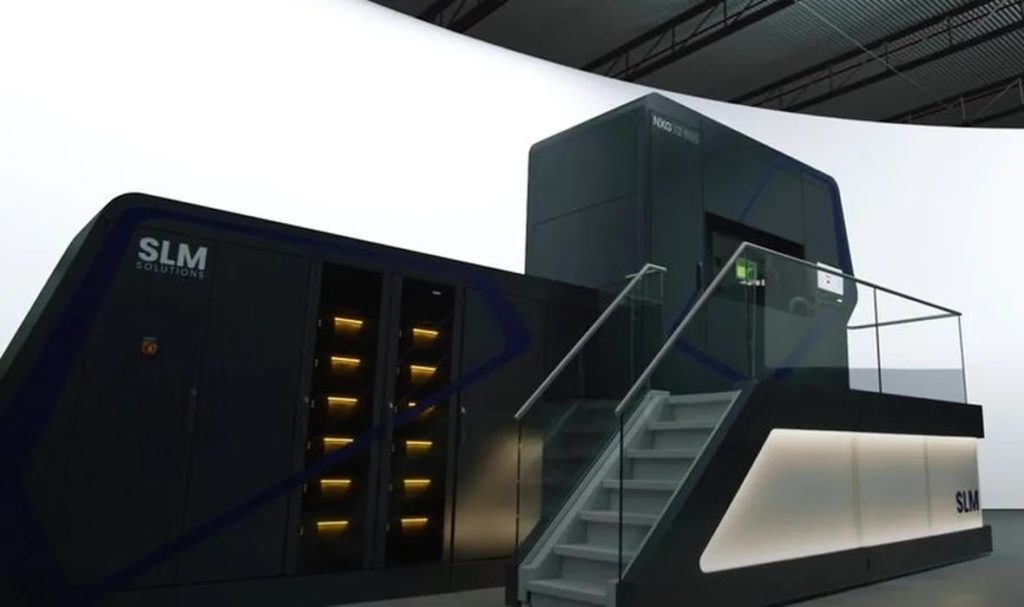
An emerging class is manufacturers offering PBF equipment but with massively larger build volumes. These devices have been created due to customer demand, where companies found traditional equipment too small for the parts they require.
Example companies providing this class of equipment: SLM Solutions, EPlus3D.
Coarse
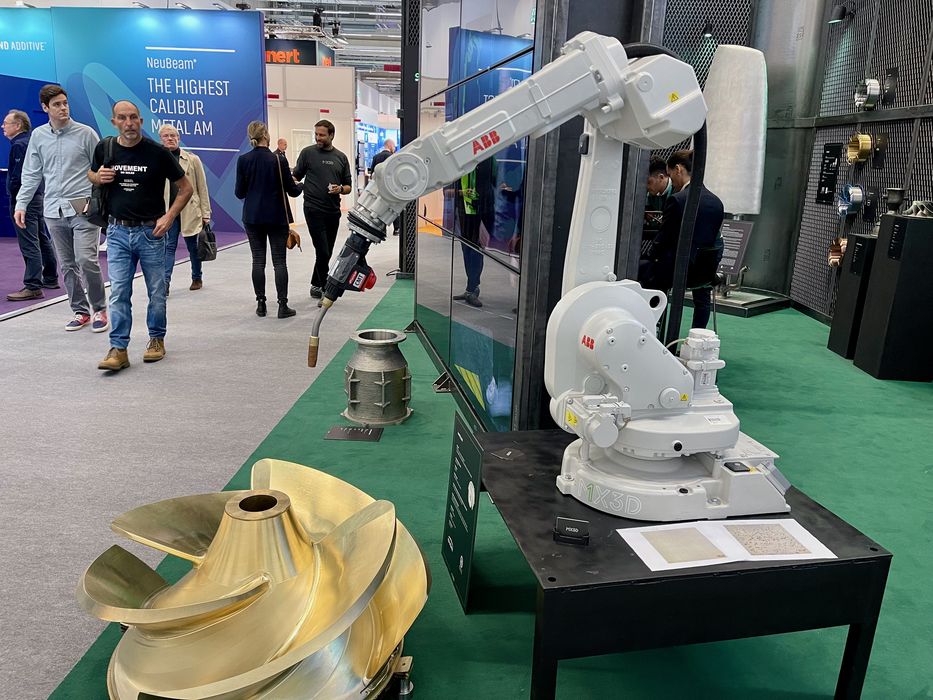
A number of companies have produced financially effective equipment using combinations of robotic technology, power or wire deposition methods, and other approaches. They all have in common the ability to quickly build relatively large metal parts, but at lower resolutions than found with traditional PBF technologies.
A frequently seen approach is simply to attach a DED wire deposition print head to a robotic arm. However, other methods exist but produce parts with similar properties.
Example companies providing this class of equipment: MX3D, Meld3D, Meltio, Spee3D, and countless CNC companies that have introduced Wire DED systems.
Foundry
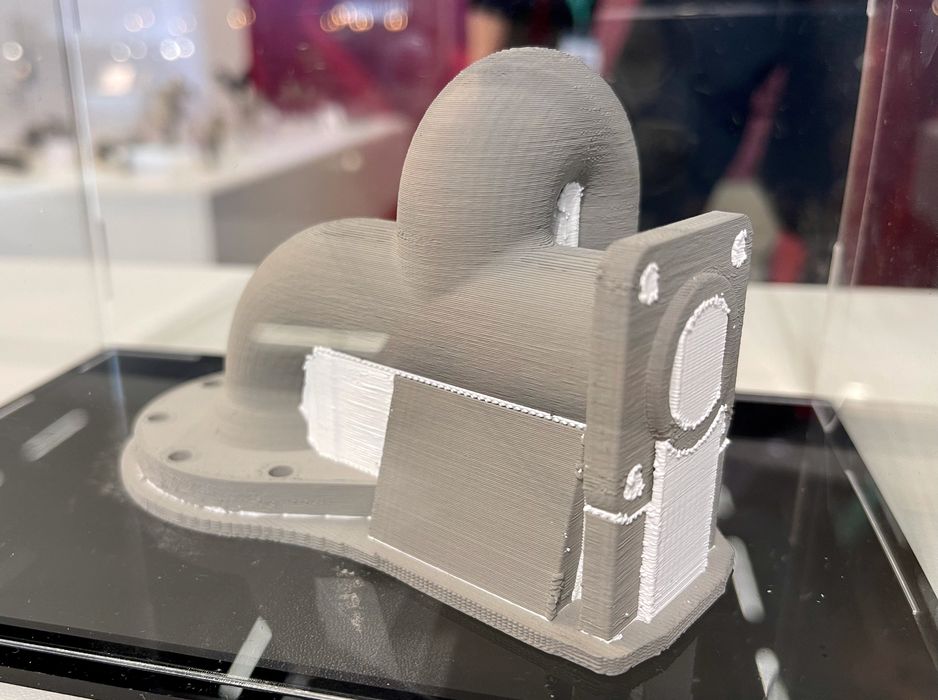
The high cost of traditional PBF systems has effectively locked out many industries that normally produce more inexpensive metal parts. Now that’s changing with a series of innovative companies that produce equipment capable of making “good enough” metal parts at far lower cost.
The processes used by these systems vary considerably, as do the specific advantages of each. However, all target foundries that are mostly stuck in older technologies and unable to afford traditional PBF systems. My hope is that these companies will bring an enormous number of small to medium metal foundries into the world of 3D printing.
Example companies providing this class of equipment: Rapidia, XJET, Desktop Metal, Foundry Lab.
Desktop
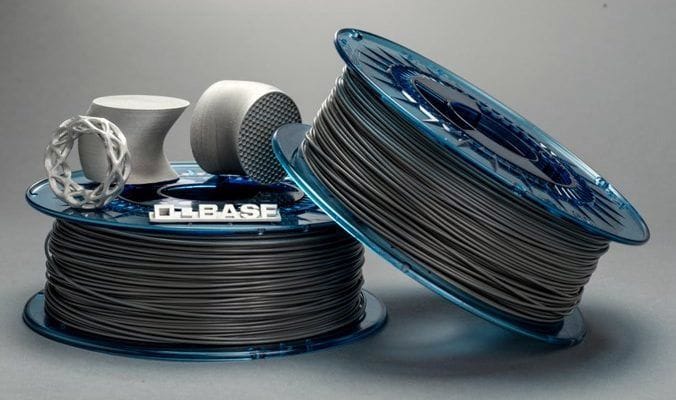
This final class isn’t so much a machine but a method. It is possible to 3D print metal objects on standard FFF 3D printers by using specialized filaments. These materials are a mix of polymer and metal, and prints are “green parts” that can be transformed into fully solid metal parts using debinding and sintering steps after printing.
While it’s possible to produce metal parts with this approach, they tend to be of quality levels less than required by many industries. However, it’s a very inexpensive method of producing metal parts.
Example companies providing this class of equipment: BASF (Ultrafuse), Virtual Foundry.