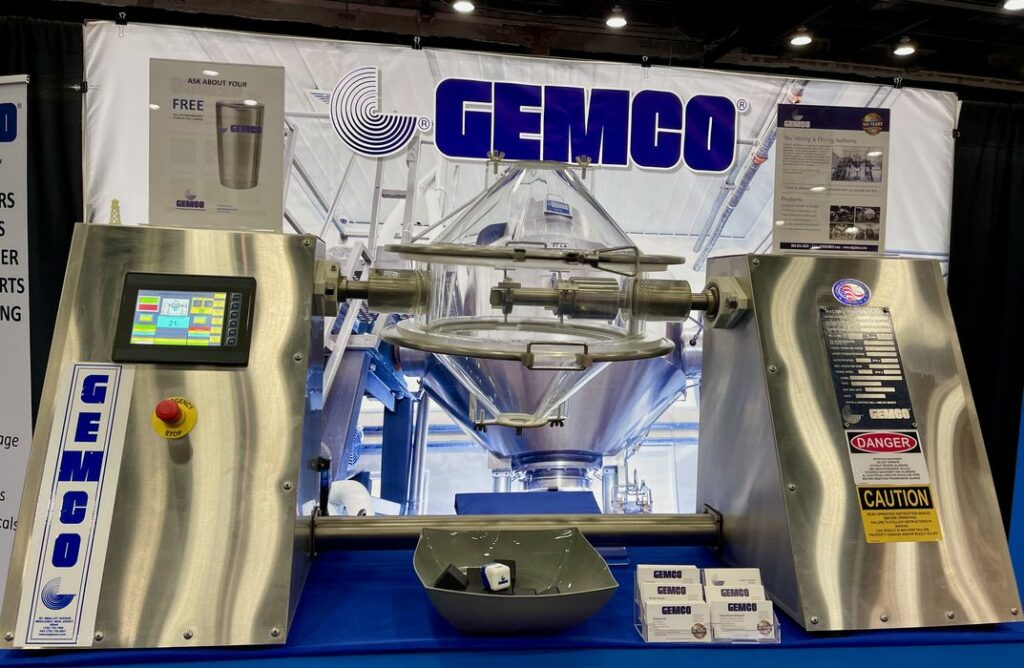
Do you know what is the real first stage of 3D printing?
You might say it’s when the operator hits the “print” button on a 3D printer. Or you might say it’s when the designer creates a 3D model in a CAD system.
But let’s wind it back even farther — and I’m speaking about metal 3D printing here.
Metal 3D printing begins with the powder being used. PBF systems require uniformly-sized, fine metal particles that are made in precision processes. Typically this is done by vaporizing a metal alloy and having it condense into small particles that solidify as they cool. By sorting the particles by size, the powder suppliers can prepare quantities of uniformly-sized powder.
But hold on, where exactly do you get that alloy to toss into the powder-making machine?
That’s where companies like New Jersey-based GEMCO come in. The over-100 year old company produces mixing and drying equipment for metal and polymer powders.
The idea is to collect raw materials, which are then mixed in the appropriate ratios for desired alloys in the GEMCO equipment, which then move on to further stages in manufacturing, eventually becoming 3D printable powders.
I spoke with representatives from GEMCO to understand how this type of mixing equipment works, and to my surprise it was quite a bit more complicated than I had imagined.
Most metal powders must be very carefully isolated from the environment, lest they be contaminated by oxygen, humidity or other external factors. This is why much of today’s advanced metal 3D printers include complex powder handling systems that fully contain the powder.
It turns out that this is also required at the mixing stage, well before the actual 3D printable powders are produced, and that’s what GEMCO is all about.
Bags of raw materials can be loaded into their equipment, which uses a tumbling approach to mixing, which ensures “zero waste”. The mixing equipment they provide can be explosion proof, similar to metal 3D printers in that the materials are isolated. They can also handle mixes of up to an astounding 400cf (11,000L)! Their gear can also make the materials undergo high pressures or temperatures up to 400F (200C) if required by metallurgists or polymer designers.
The results of their equipments’ processing is raw powder that’s perfectly suited for transformation into 3D printable powder by others. They say “it’s good every time!”
It’s easy to think of 3D printing as a technology that takes some powder and makes useful objects from it, but the true path requires many steps well before that printing takes place.
The next time you’re 3D printing, think for a moment about the material you’re using and ask yourself, “Exactly how did this material get here? How was it made?”
Every material has a story behind it.
Via GEMCO