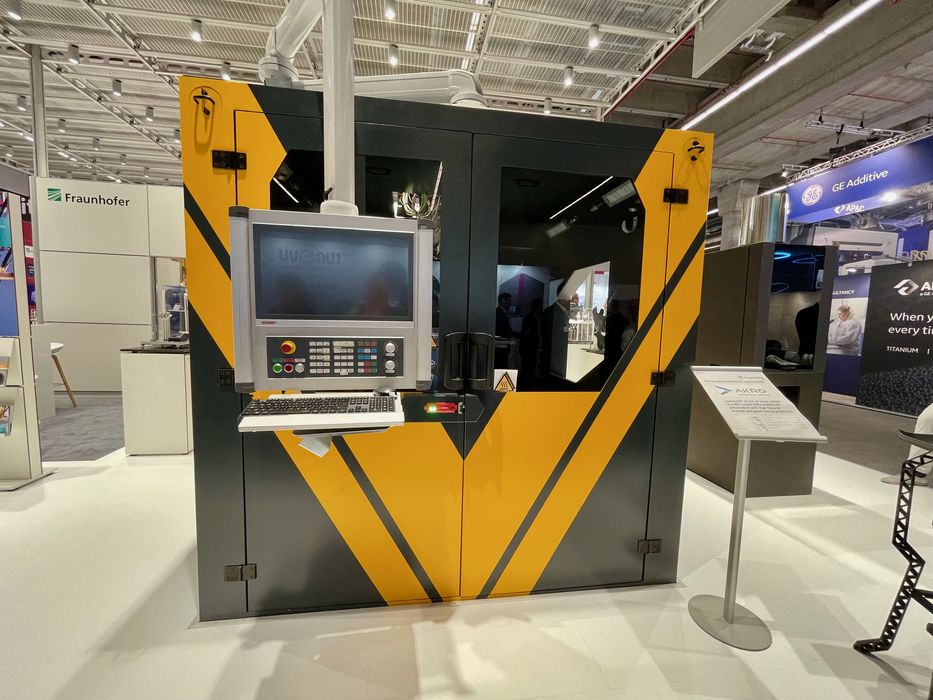
We had a look at the very unusual METROM SEAMHex 3D printer.
The SEAMHex is a large-format 3D printer built by METROM, a CNC machine tool company. They worked with the Fraunhofer Institute to implement a new form of 3D printing they call “SEAM”, or “Screw Extrusion Additive Manufacturing”, which uses granular (or pellet) input material.
Pellet 3D printers are not new; they’ve been used for many years and have a very clear advantage: material cost.
Most thermoplastic extrusion systems use filament, which is in fact just pellets that have been extruded into a uniform strand. To produce that filament, effort and cost is incurred, making the cost of filament always significantly higher than the same material in pellet form.
Ingenious engineers years ago realized this and developed pellet based extruders. These systems basically have an auger-type screw that pushes the granular material into a hot chamber, where the thermoplastic melts. The incoming pellets creates pressure that ultimately creates the extrusion of softened thermoplastic through the nozzle below.
This approach has been successfully used for years, but there is a problem: the flow rate is difficult to control. This is because that pressure created by the screw is “elastic”. In other words, stopping the screw doesn’t immediately stop the flow from the nozzle, there’s a notable delay.
The result is that pellet extruders typically have issues reproducing complex shapes. Corners in particular are challenging because the toolhead slows down to change direction, but the flow remains the same. Blobs can appear at corners, for example.
The SEAMHex overcomes this effect with a very interesting solution. The machine is able to very precisely control the flow from their pellet extrusion system.
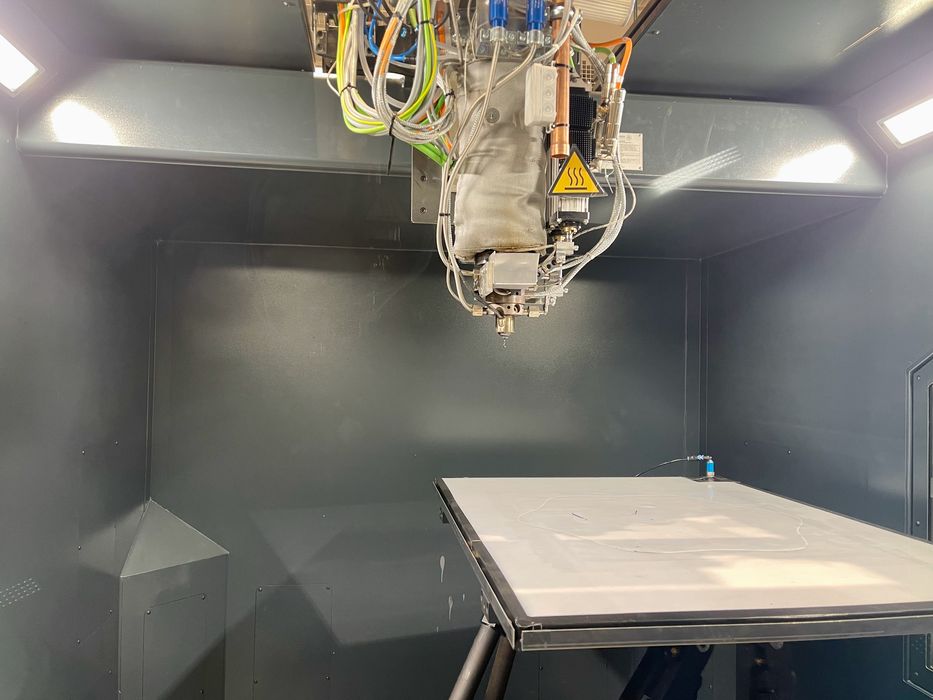
How is this done? Do they have an ai-designed screw mechanism? No, it’s actually quite a bit simpler: they have a valve on the hot end.
The screw mechanism basically produces constant force when operating, that doesn’t change. What happens is that the valve opens and redirects material elsewhere, slowing down the flow. This apparently can be moderated to allow precise control over the flow. You can even see the valve lever move during operation.
The result is that the SEAMHex machine can attempt far more complex 3D prints than can be done with typical pellet extruders.
METROM deploys the mechanism in a variety of kinematic solutions. It’s possible to use the SEAM system in cartesian motion systems, as well as robotic. The system can also be integrated with other types of toolheads to create hybrid-style equipment.
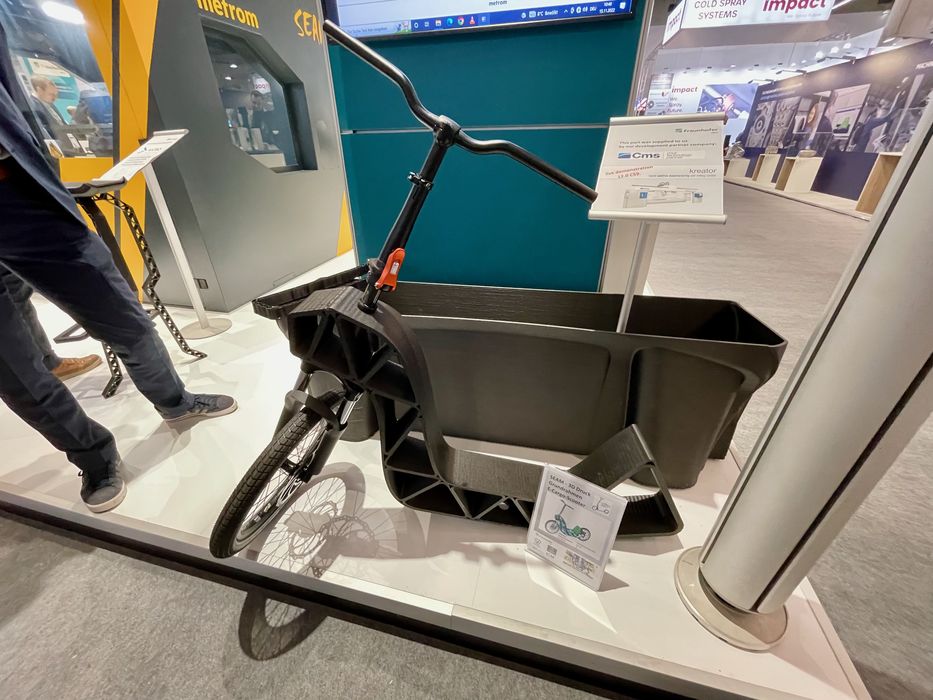
SEAM is an interesting additive technology that could be quite useful for larger, complex 3D prints. The technology allows for precision 3D printing but at the same time maintains the lower cost of pellet material.
Via METROM