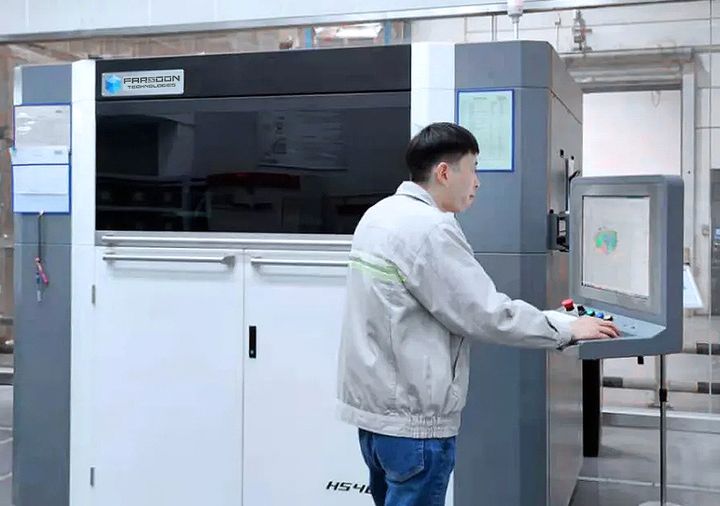
I’m reading a case study from Farsoon and it showed a not-so-direct route leading to additive manufacturing for production applications.
The long-term goal of many 3D printer manufacturers is to get their equipment involved in actual production manufacturing, rather than prototyping use. The reason for this is clear: there’s a lot more manufacturing taking place than prototyping.
However, there are significant challenges along the way: equipment may not fit well into today’s advanced digital manufacturing environments; part quality needs to be sufficient to meet regulatory standards; production time and expense need to fit into the profit envelope; etc.
You get the idea. It is, at first glance, a big hill to climb if your intent is to use 3D printing for production use. Meanwhile, 3D printing is widely accepted as the de facto standard for rapid prototyping or for one-use parts.
That’s the scenario facing 3D printer manufacturers who dream of bigger sales to the manufacturing world. Many have undertaken sophisticated programs to make industries aware of the possibilities from the technology. Some have been mildly successful. Some have not.
But in reading Farsoon’s story, another route became apparent.
In their case study they examined the situation at MANN+HUMMEL Shanghai, a producer of advanced filtration products. One of their major customer segments is the automotive industry.
MANN+HUMMEL observed their clients have been changing. Due to increased competition and market evolution, the time requirements for vehicle development has shortened considerably. While years ago the start-to-finish duration of a new automobile project tended to be around 36 months, that’s now changed to only 18 months.
The auto manufacturers had to speed things up, and that, of course, means all of their suppliers also had to speed up. That meant MANN+HUMMEL had to somehow change their processes to increase product development speed.
They did so by obtaining a Farsoon polymer SLS machine, a model 403P, in 2019. This enabled the company to dramatically shorten their product development lifecycle because prototypes could be made immediately. Otherwise, they’d be waiting for industrial molds for weeks. This shortened the company’s design-to-product cycle significantly.
That’s a good thing.
However, the placement of a machine for prototyping purposes does something else: it exposes the company to the concepts of additive manufacturing.
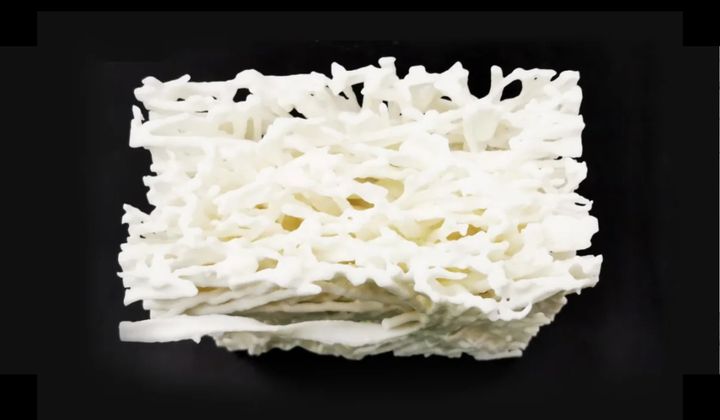
But then something interesting happens. MANN+HUMMEL obtained customer requests for parts that were highly complex. One of these requests resulted in the filtration media structure above. These could be made using conventional approaches, but that would be expensive and time-consuming.
However, by having a 3D printer onsite with now-experienced staff, the question could be asked, “hold on, could that 3D printer make this?”
Of course it could. And so it seems that MANN+HUMMEL is now making many production parts using 3D printing. Wang Huaigu, MANN+HUMMEL Shanghai’s Testing & Prototyping Manager, said:
“Thanks to the high quality parts produced with Farsoon 403P, we are able to further implement additive manufacturing in our business sector of end-use production. Functional parts with complex geometries now are able to be produced with simplified manufacturing process and increase the structural integrity by combining multiple parts to only one. The high resolution, size-accuracy and optimal mechanical performance of the build parts requires much less post-processing before delivered to customer. As of today, more than 30% of our SLS parts are produced for end-use applications – and the number is still growing.”
This is a very interesting scenario, as it suggests some 3D printer manufacturers might be going about this wrongly. Maybe all it takes is to place machines in a business for any purpose, perhaps rapid prototyping, and then let the business discover how it can best be used when a challenging request arrives.
Perhaps 3D printer manufacturers should prioritize getting equipment onsite in customer premises first, and then stand ready to educate, explain and assist when the interesting applications eventually arrive.
After all, it’s about the results, not the technology.
Via Farsoon