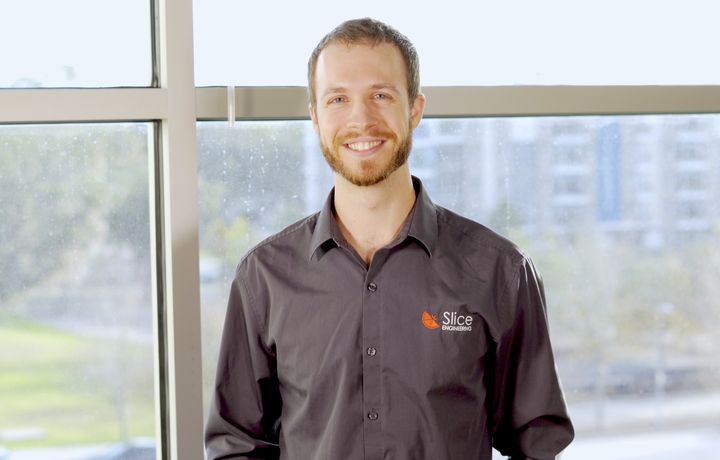
I had a chat with Slice Engineering’s Daniel Barousse.
You may not have heard of Florida-based Slice Engineering, but you likely will in the future. They, like many 3D printing startups, were born from a gap in the market, one that they are filling with some innovative products.
No, they don’t make 3D printers, but they do make components — specifically hot ends. Some of them are likely on 3D printing equipment you may own and not even realize it.
It was in 2016 that the two founders, Daniel Barousse and Chris Montgomery, were working at a medical device manufacturer. As part of their roles at that company, Montgomery would design new components, and Barousse would help tweak them for proper production. Thus the two would often work together.
One day they were faced with the production of a particular medical device that would be subject to class five sterilization, and they thought, “Let’s try this on a 3D printer — we can print it in PEEK. How hard can it be?”
They quickly realized that their inexpensive desktop 3D printer could not print high-temperature materials, and so they scoured the market for components they could use to modify their machine to do the job. After reaching out to all the usual suspects, they realized there was no option.
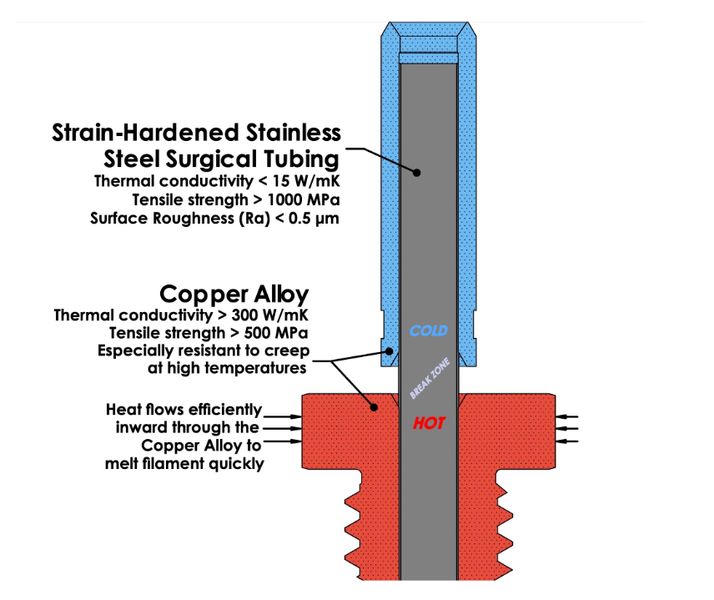
Being designers, Montgomery and Barousse simply created their own product, which turned out to be the now-famous Mosquito hot end. The Mosquito was quite effective due to a bimetallic design: two zones made from highly heat-conductive copper were separated by a less-conductive steel zone in the heatbreak. This unique combination proved extremely effective at thermal management and allowed higher-temperature materials to be 3D printed.
One of their first clients was STACKER, who used this new hot end when they launched one of their multi-head devices on Kickstarter.
Mosquito Hot End
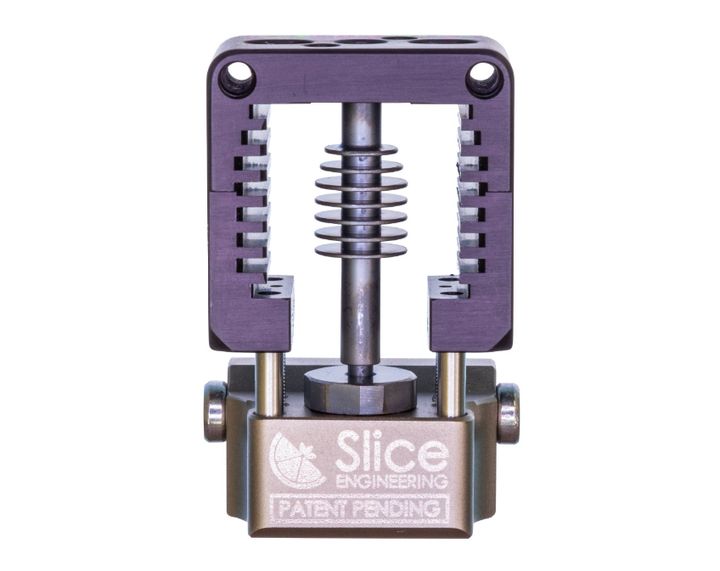
Two two founders then officially launched the Mosquito at the Midwest RepRap Festival in 2018. Barousse said they brought 35 prototype units with them, and they were entirely sold out by 10AM on the first day of the festival.
At that point, they decided they really had a market for this type of equipment.
Since then they’ve grown significantly. They’ve made deals with multiple resellers and have been working with OEMs as a component supplier. They’re currently working with LulzBot, HAGE, and others.
Last year the two founders finally quit their day jobs to focus full-time on Slice Engineering, and that move appears successful, as they now boast a staff of seven. They’re shipping product to 29 different countries, and have a global presence due to a growing network of resellers.
They’ve also partnered with other component suppliers, one of which is Bondtech, who produce extruders. Recently the pair announced a combo product for upgrading Creality desktop 3D printers.
I’ve also learned that Slice Engineering’s water-cooled Mosquito hot end is being used in the new Smart International Macro series of 3D printers. This demonstrates that Slice Engineering’s products are not merely for desktop equipment, but are also quite viable for industrial equipment.
Copperhead Hot End
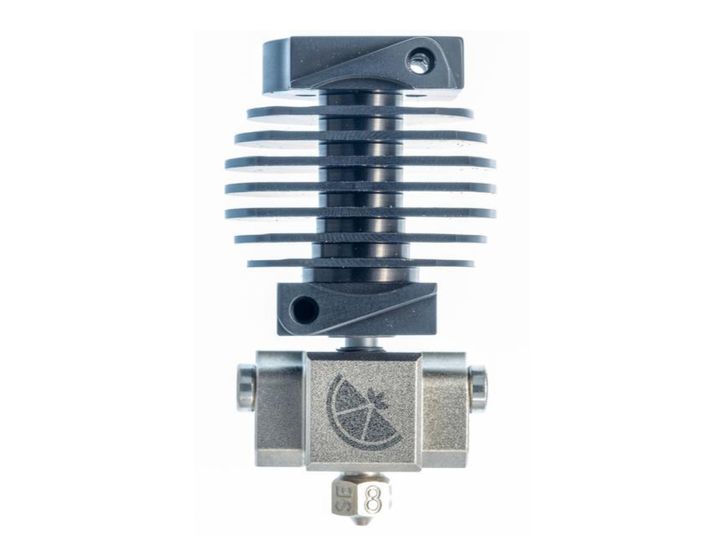
One of their most recent products is the Copperhead line of hot ends. Barousse explained they wanted to hit the market with an option that’s in-between the common steel hot ends seen everywhere and the more expensive and powerful Mosquito line. The Copperhead line includes copper nozzles lined with carbide, which makes them somewhat abrasion-resistant. They’re not quite as strong as true hardened nozzles, but it’s a step in-between. True to form, the Copperhead line’s price point is also in-between.
In my discussion with Barousse, we certainly spoke of the company’s recent new product, Plastic Repellent Paint. I thought this product was quite unusual; while it is something hot end operators might use, it is far from the expertise of Slice Engineering: it’s paint, not hardware!
Barousse explained that the company is now branching out into other related areas. Their philosophy is to ensure high-performance 3D printing has the components necessary for success, and if paint is something that meets that need, then they’ll do it.
However, it seems they brought in external expertise, in this case chemical expertise, to develop the paint. It seems that with the success of the paint, Slice Engineering may be considering additional chemical products in the future.
I asked Barousse what type of new product might they be working on, speculating that it could be a specialized hot end designed for large-format 3D printers that often suffer from extraordinarily lengthy print times. Barousse wouldn’t say much, but admitted there might be “high flow things” coming.
For high-performance hot ends, you might want to check out Slice Engineering’s offerings.