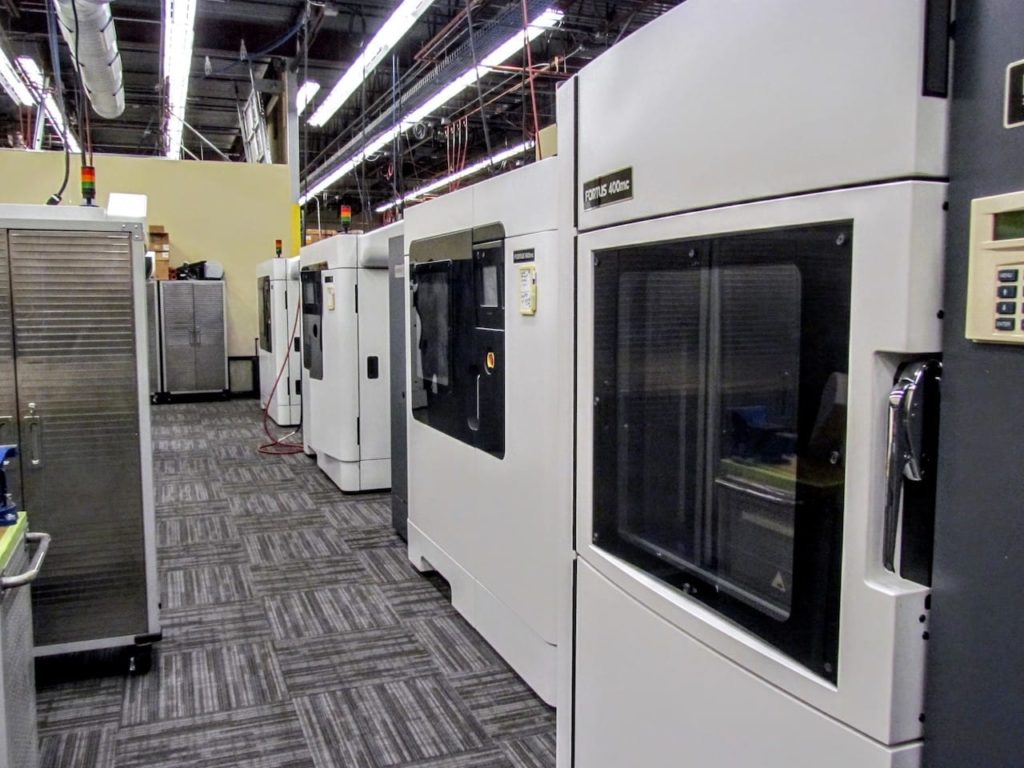
A long-term trend has transformed today’s 3D print services business into something quite different.
Years ago when 3D printers were devices used only for rough prototyping and then only by a select few people, 3D print services were quite different.
Then the idea was to purchase a machine or three and try to keep them busy 3D printing customer requests. Usually this meant emailing a 3D model in STL format to the service, whereupon a tech would manually inspect the file for printability. Eventually the print would take place and results would be shipped to the requestor.
Over time this type of operation broadened its capability by adding more and better machines, and especially supercharging their public interface. Eventually 3D models would be automatically checked for printability, reducing the labor required to handle prints.
At this time the major 3D printer manufacturers would operate their own 3D print services. This was a way to allow prospective buyers to test the technology before making a purchase, and in some cases to handle low volumes until they rose and justified purchase of equipment.
Such centers also served as excellent platforms for showing off equipment to buyers new to the technology.
These independent and manufacturer-owned facilities still exist, but there seems to be a change washing over them.
The independent operations began the transformation by adding additional making technologies to the mix. Instead of just offering 3D print services, they might also perform laser cutting or CNC milling.
Why add these “foreign” technologies? It was simply because of customer requests. It turns out that clients weren’t specifically interested in 3D printing, but — surprise — were more interested in making the parts they required, using whatever technologies were necessary. In many cases this meant not just 3D printing, but other technologies.
It’s not surprising, when you think about it. Customers would arrive with an idea for a part but not necessarily knowing which technology was required to make it. After seeing many clients walk away to, say, a laser cutting service, you can understand why they added these technologies to their service.
But adding technologies changes things. These operations were not just 3D print services, but instead were becoming general-purpose manufacturing services. Once you add one additional technology, it’s easy to add even more.
That’s very different from the original, plain 3D print services.
Even the 3D printer manufacturer-owned operations began to incorporate other technologies, and even equipment from their competitors. This is because there really isn’t a business for 3D print services.
The business is instead making parts and now most realize this.
So we see the technologies in 3D print services, er, I mean manufacturing services, blurring. They’re now becoming an optimized collection of making gear that’s able to handle as many types of incoming part requests as possible.
This trend has even leaked into the interior of 3D printer manufacturers themselves, as we now see several taking steps to rapidly diversify their technological capabilities.
In the past the equation looked something like this:
- 3D Systems: SLA and SLS equipment
- Stratasys: FDM and PolyJet
- EOS: PBF
Now that picture is changing rapidly, with Stratasys selling SLA equipment and 3D Systems developing FDM-style equipment. Even newcomer Desktop Metal sells plastic and resin equipment. There’s no boundaries these days, and today’s “equation” would be a rather large table with plenty of overlaps.
It’s a blurry world in 3D printing, and it’s going to get a lot more blurry as time passes.