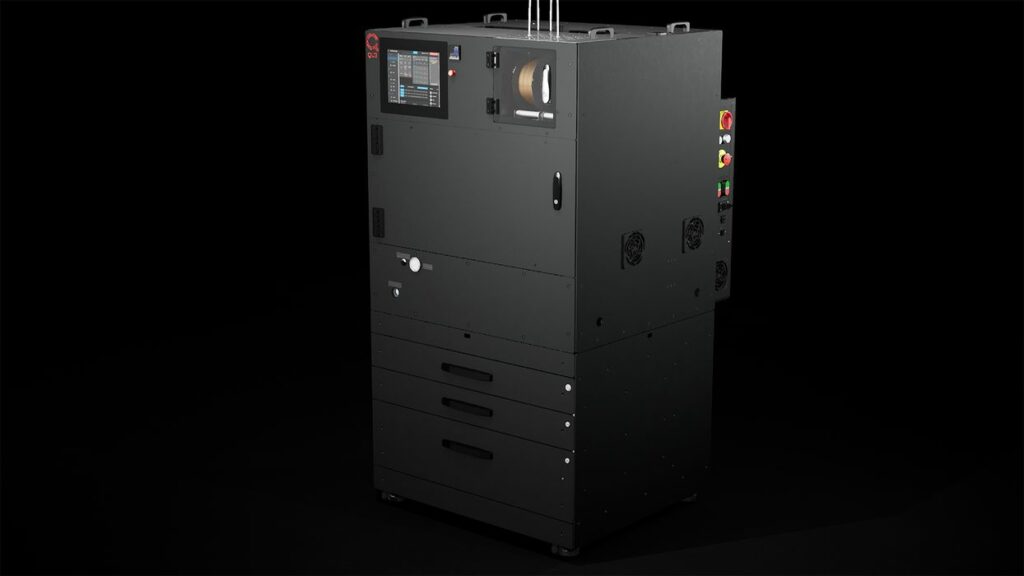
QUALUP SAS introduced their new high temperature 3D printer, the Qu3-HT v2022.
If you haven’t heard of QUALUP SAS, they are actually one of the older companies in the space, having been founded in 2004. In 2011 they decided to move into 3D printing, and by 2013 had launched their first device on the market.
The France-based company has provided a number of innovations over the years to their equipment, some of which are likely the first instances of the innovation in the industry. For example, they introduced a then-rare all-metal hot end in 2013, and offered one of the first enclosed and heated chambers from the group of companies that emerged after patents expired in 2009.
Their latest device, the Qu3-HT v2022 includes some notable innovations itself.
Qu3-HT Specifications
The high temperature device has specifications suitable for professional use:
- FFF style device
- 300 x 250 x 300 mm build chamber
- Hot end temperatures from 300-500C
- Bed temperatures from 30 to 250C
- Chamber temperature from 30 to 270C
- Annealing heat cycle available at print completion
- Wide range of possible materials, including PEEK, PEKK, PPSU, PEI/ULTEM and more
- Carbon fiber reinforced materials possible
- Isolated electronics and motors from the heated chamber for longer machine life
- Liquid cooled print heads
- Multiple print surfaces available to match the materials being printed, inclusion PEEK, PEI, Metals, Ceramic
- Easily removable plate for print removal
- Interesting separate workstation for print head maintenance, which allows heating outside the chamber
- Optional FLIR infrared optical system to monitor thermal conditions during printing
That’s an impressive list of features, but there’s more to the newest printer version.
Qu3-HT Filament Volume Compensation System
The main new feature of the latest Qu3-HT machine includes a system to automatically compensate for variations in the filament.
The problem being solved is related to the inconsistency of filament production. Normally, FFF 3D printers assume (incorrectly) that the incoming filament is of a consistent diameter. Specifically, the flow calculations make the extruder motor turn at a rate to extrude a certain amount of polymer — but only if the volume of the filament is consistent.
The typical approach for solving the problem is to obtain filament that is expertly made to be within specific small tolerances. “Good” filament these days means the diameter is perhaps within +/-0.05mm of the stated diameter. Really good filament is within +/-0.02mm. Of course, there are much worse filament products that we won’t mention.
While those might be “good” filaments, they are still not consistent. Even 0.02mm is enough to slightly alter the volume of material coming out of the nozzle. QUALUP SAS said:
“A simple percentage calculation shows that between 1.80 and 1.70mm (1.75 +/- 0.05mm) the volume variation is 12%. Between 1.85 and 1.65mm (1.75 +/- 0.10mm) the volume variation is 24%.”
These variations could affect the resulting print by exhibiting “blobs” or gaps. The gaps are actually worse, because they effectively weaken the part.
QUALUP SAS decided to fix this problem through a real time monitoring and adjustment system.
How does it work? The system has a means to measure the diameter of incoming filament as it enters the print head. The diameter is measured in two perpendicular directions, allowing the software to quickly calculate the ovality of the filament, and thus the area. This can then be compared to the target area of a standard filament to determine the amount of divergence.
Once it’s known how far off the filament happens to be at that instant, it’s an easy matter to slightly speed up or slow down the extruder motor to compensate. The result is that the flow rate is actually true on the Qu3-HT, rather than just being “close” in other FFF 3D printers.
The consistent flow rate should make it possible to 3D print parts with higher quality and superior visual appearance and surface texture.
This is an extremely interesting development that as far as I know is available only on this 3D printer. It’s one of those features you wish was present on every 3D printer.
Maybe someday it will.
Via QUALUP SAS