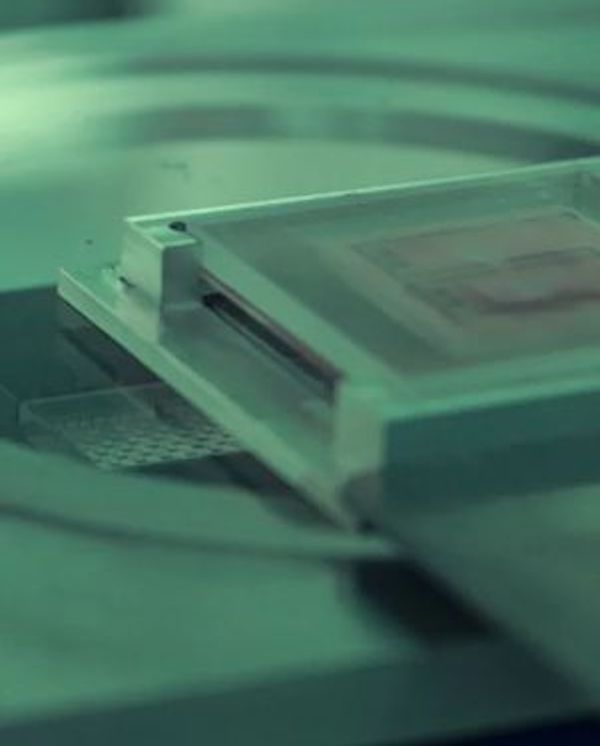
A Bay-area startup hopes to 3D print batteries using a new hybrid process.
3D printed batteries have long been a target application for companies. In order to increase the capacity of a battery, one would typically have to dramatically increase the surface area on which an electric charge could be stored.
With conventional approaches, foam-like strategies attempt to maximize this surface area. However, 3D printing offers the possibility of purposely designing complex structures that would be the most efficient in providing extra surface area.
Several companies have embarked on a 3D printed battery journey, but none have yet to surface with truly practical products at the right manufacturing cost.
There seems to be a new entry on that list now, with Bay area-based Sakuu.
Sakuu 3D Printing
There’s not much publicly available information about the company, other than what’s posted on their website and a few stray mentions on the Internet. However, I did some sleuthing and found out the following:
- The company was founded in 2016, and currently has twenty-something staff at their Santa Clara, California HQ
- They’ve raised over US$23M from investors, with the most recent raise being US$14M this past January
- One of their investors is Musashi Seimitsu, a manufacturer of transportation equipment
- They own at several patents, one of which is US-20200298477, which describes a 3D printing process, and US-20190375159, which describes a multi-material 3D printing process
It may be that Musashi Seimitsu is interested in the potential use of 3D printed batteries in their vehicular products.
What else do we know? Their site explains, briefly, their mysterious 3D printing process:
“Our unique AM platform can lay down multiple materials, using multiple processes, in the same layer. The result: raw materials in, fully-functioning devices out. Two steps where previously over a hundred steps were needed. Our platform is nothing less than an industrial renaissance.”
One report from 3D-Grenzenlos Magazin suggests they are using a carrier material, PoraLyte, onto which “different materials are sprayed”.
This sounds like a binder jet process, in which a powder (PoraLyte) receives droplets of different liquid materials. In fact, their home page has an animation of vertically-moving droplets, which might hint at the nature of their process.
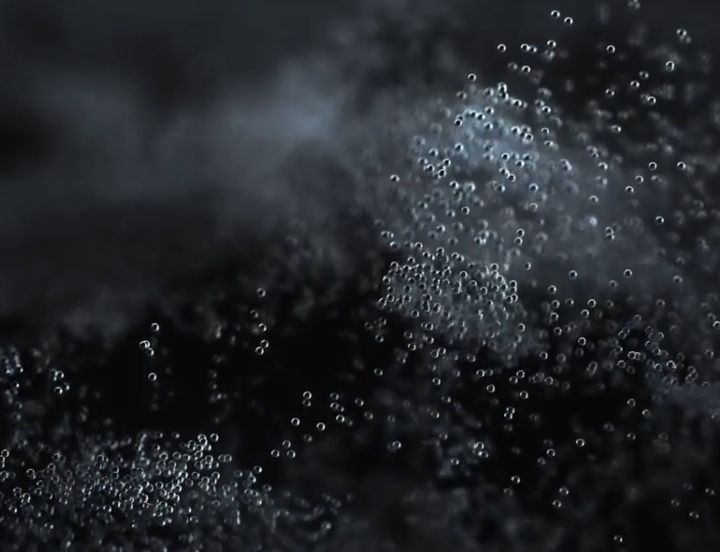
Most binder jet systems involve a base powder and a single jetted fluid material, typically one that binds the powder particles together, hence the name of the process. However, it could be that Sakuu has a fluid deposition system that involves multiple and different liquid materials.
HP and XJET have somewhat similar 3D printing processes, but they involve a heating process after printing to finalize the prints. It’s unclear whether Sakuu requires this step, but it would not be surprising if they do.
PoraLyte Implications
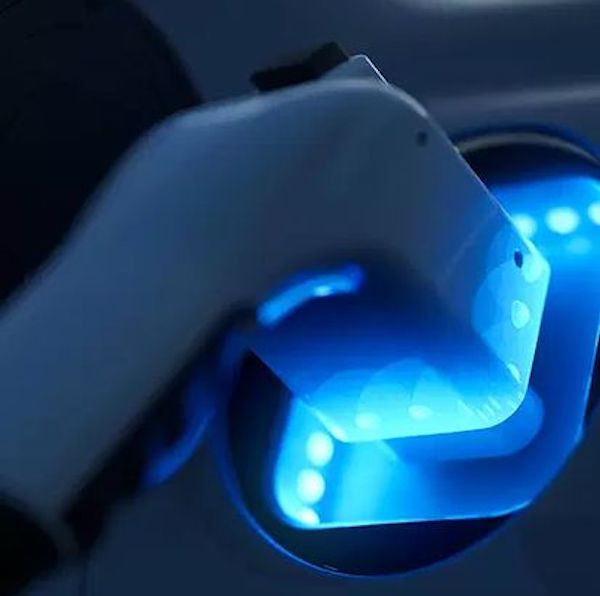
The PoraLyte material could be the key to this technology, and let me explain why I believe so.
Sakuu has been awarded a patent for their 3D printed “KeraCel” solid-state battery (SSB). This battery is said to “have the same capacity as existing lithium-ion batteries yet will be half the size and almost a third lighter.” Further, it can be manufactured at “blazing speeds”.
I suspect that the PoraLyte carrier material is composed of small particles with massively complex surfaces. These dense surfaces would be the key to the energy capacity of the KeraCel SSBs.
The carrier material would be electrically activated by selective deposition of conductive and non-conductive fluids that would create the necessary electric paths.
That appears to be a feasible approach for production of 3D printed SSBs, and in fact could be quite rapid. Remember that batteries are typically not large, and this type of powder process could be scaled up to fairly large build volumes. The powder process also permits “3D” printing where the entire build volume is stacked to the top with prints supported by unused powder.
Sakuu Applications
Based on the above, I suspect that the Sakuu process is likely to be highly specialized for battery production and a few other specialized applications.
Sakuu does state the possibility of “3D printing your own pathogen detector”, which again could be an application where the porous nature of the PoraLyte could trap microbes that could be detected by appropriate embedded chemicals.
It may not be as appropriate for other general purpose uses. However, my guesses can always be wrong.
I’ll be watching Sakuu for further developments.
Via Sakuu and 3D-Grenzenlos Magazin (German) (Hat tip to Benjamin)