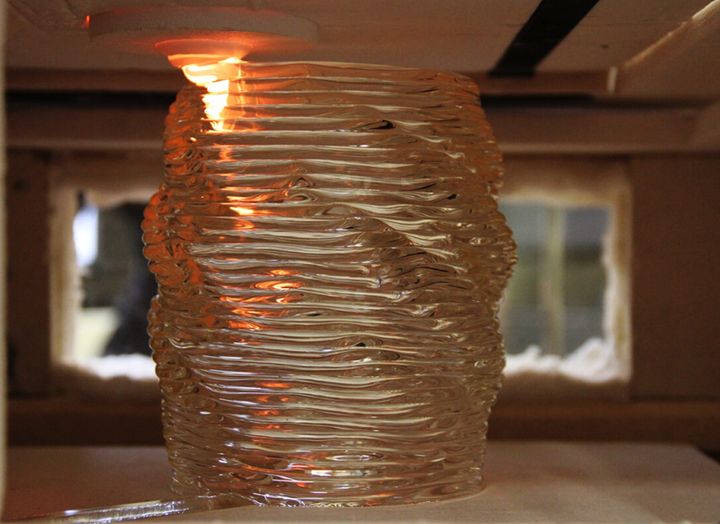
There’s a design studio that focuses on use of 3D printed molten glass.
There are plenty of unusual materials that people are 3D printing these days, but one we don’t often hear about is glass. Yes, that same transparent material we see and touch everyday.
It turns out it’s an incredibly challenging material to 3D print, but in spite of that there is a design studio that focuses on 3D printing of molten glass. Lios Design was founded by former MIT students, Daniel Lizardo and Michael Stern, who originally developed molten glass 3D printing as a research project way back in 2015. Our report on glass 3D printing, or “G3DP” as they call it, describes the process.
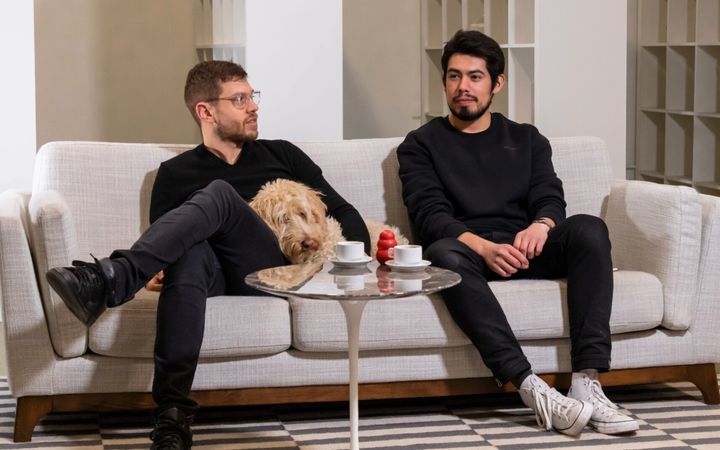
But as a quick catch-up, glass 3D printing requires very extreme temperatures, perhaps the highest for any type of 3D printing done today. G3DP extrudes molten glass at a scorching 1000C into a build chamber that’s heated to 500C to avoid cracking the glass as it cools.
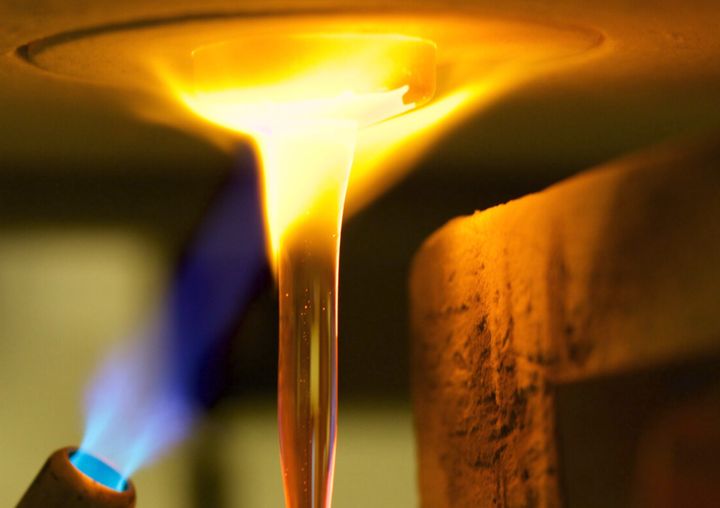
And by “extrusion”, I mean “dripping”. The G3DP process does not involve any mechanism to push the glass flow forward. Instead it uses gravity!
The G3DP printer holds up to 50lbs (23kg) of glass input material. This is heated to the required extreme temperatures, whereupon it flows out the bottom through a ceramic nozzle.
As you might suspect, the flow rate slows as the amount of material is used up. To counteract this effect, the G3DP printer’s material reservoir is a very wide vat that minimizes the inconsistencies of gravity. Perhaps in the future they may add a means of controlling the flow.
There’s an implication of this extrusion method: You really must use continuous extrusion without stopping, as they control the process via temperature only. This does constrain the geometry of the 3D models produced somewhat.

While the nozzle remains stationary, the build plate is moved in X, Y and Z axes – as well as rotating. The rotation movement was added to help counteract the unfortunate hysteresis properties of glass: if you change the direction, the flow doesn’t immediately raact like it would for a thermoplastic extrusion. By rotating the build plate they are able to minimize this effect through some sneaky GCODE motions.
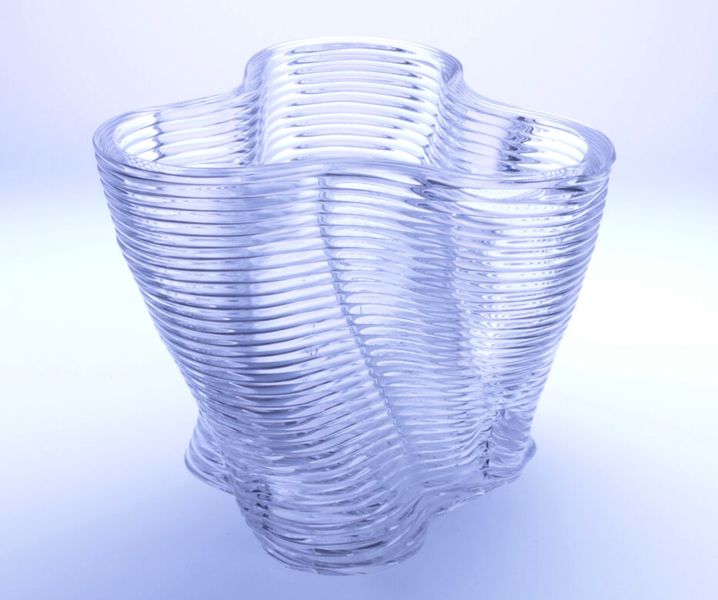
In a Reddit post, Lizardo describes this unusual extrusion process:
“It is kind of a crazy vase mode. There are odd material behaviors because of how viscous and elastic it is. Overhangs and minimum radius are dynamic and a lot depends on path length.
The feedstock is a crucible of fully molten glass at ~1000C, gravity fed through a ceramic nozzle, the tip of which is in the ceiling of the build chamber, which is heated to ~500C to prevent the material from going below its annealing temperature.”
One interesting property of these glass 3D prints is that they are fully isotropic: the layers fully bond with each other, making the resulting prints impervious to leakage. However, the process does have issues making tops and bottoms, so that does constrain the usage.
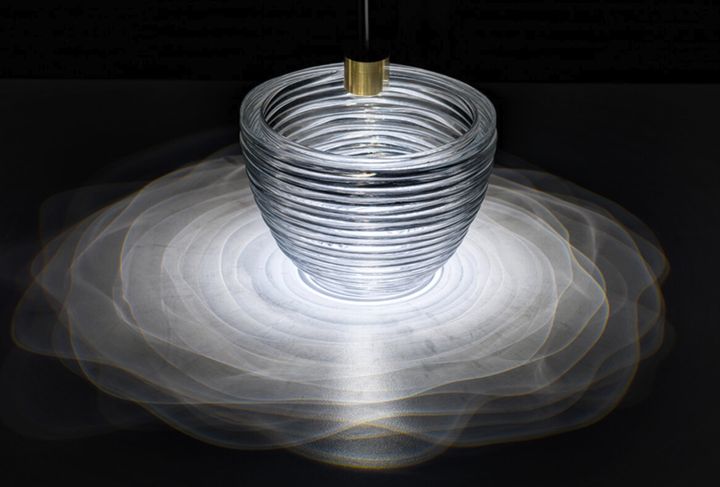
So far the technology has mostly been used to produce lighting designs and similar applications, and the Lios Design website has plenty of images of all kinds of experiments and products they’ve produced in the past. I get the impression they may be looking for new types of applications, hence the need for this story.
If you have a need for digitally-designed glass structures, Lios Design may be able to help you out.
Via Reddit and Lios Design