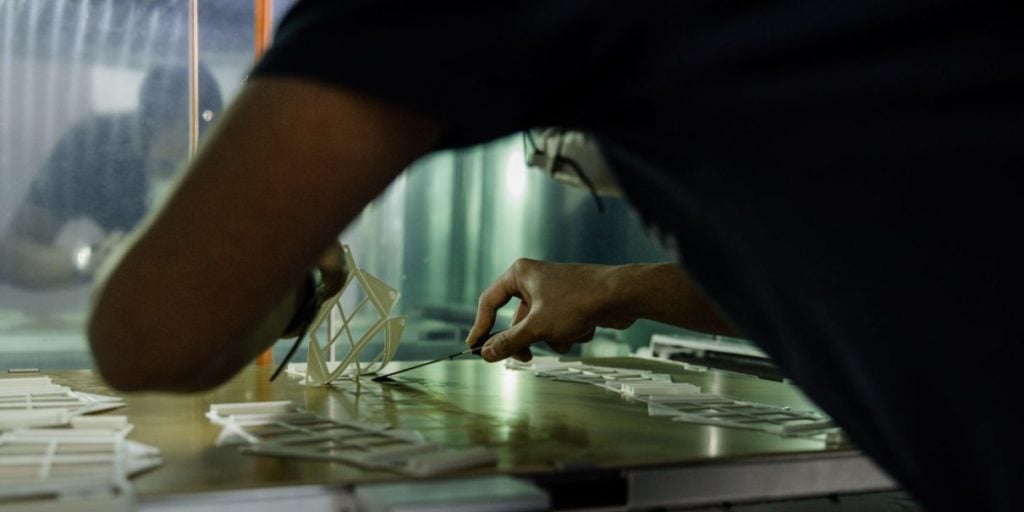
A recent survey across manufacturers supports the need for major upskilling focus to scale up industrial additive manufacturing.
Essentium, known best for its HSE additive manufacturing platform, also has another vital offering for the 3D printing industry: knowledge. The Texas-based company often orchestrates independent global research undertakings to dig into “the current and future use of industrial 3D printing.”
We’ve previously seen such efforts yield interesting results regarding applications in additive manufacturing, use of and challenges with the adoption and use of 3D printing in manufacturing situations, and the demand for open material ecosystems.
Additive Manufacturing Education, Skills, & Training
Today, survey results are focused on a vital area for growth in additive manufacturing: education, skills, and training.
Among the key findings from the survey results are:
- 28% of manufacturers reported their personnel lacked AM skills
- Among manufacturing executives, 90% agree about the potential of industrial-scale 3D printing to save billions in manufacturing costs, 84% agree about driving competitive advantage, adn 85% agree about the economic advantage
Keying in on that top need for personnel skills, Essentium’s survey found further areas for improvement across businesses bringing additive manufacturing into the fold.
Top organizational changes needed are:
- 55% say designer expertise
- 44% say production team mindset shift
- 38% say evolution of procurement strategies
- 29% say finance teams understanding cost and value implications of AM
- 26% say procurement teams re-education about buying 3D printing materials rather than focusing on the assets of components
Essentium is keen to provide not only a survey examining these aspects, but to help drive the solutions. As CEO Blake Teipel, PhD, explains in the survey announcement:
“Realizing the true value of industrial-scale additive manufacturing is highly dependent on a skilled manufacturing workforce that has the expertise to hone, advance, and support AM processes. We are supporting customers, partners, and universities as they respond to this urgent industrial need for an AM-ready workforce primed to transform the world of manufacturing and the products it creates for both competitive and economic advantage.”
Upskilling in AM
As impressive and innovative as additive manufacturing technologies are, we all have to face a foundational truth: they require people to make them work.
These people are many:
- Designers to create the parts
- Technicians to run the machines and the post-processing operations
- Quality control, from standards development to final part inspection
- Management willing to invest in a “new” technology suite
- Customers willing to invest in “new” solutions
- Companies developing software, hardware, and materials specifically optimized for additive manufacturing
- Researchers and inventors innovating the next generations of AM processes and technologies
From ideation to investment, it’s vital that more people understand the value proposition of additive manufacturing. From design to production, it’s critical that more people become qualified to actually create parts using these new technologies. From standards to media, it’s necessary that mainstream acceptance picks up in an informed way to broaden the realizable reach of additive manufacturing.
Each of these areas, from the technical to the managerial, requires education and training.
The 3D printing industry has been gaining momentum for years now as a serious manufacturing sector. Over the last year and a half or so, the global pandemic and other supply chain issues have highlighted the importance and readiness of decentralized production solutions incorporating additive manufacturing.
Even in the face of economic disruption, the AM sector has continued to grow — and is indeed rife with job opportunities now. The caveat: many of these job openings are for qualified, trained individuals, and there simply aren’t enough of those to fill every current vacancy.
There’s no one or simple solution to building up the AM workforce in the immediate. But highlighting the need for upskilling, as well as the growing awareness in manufacturing through surveys like Essentium’s, is an important start. The next step? Doing something about it. Hopefully we’ll only see educational, apprenticeship, vocational, and other training opportunities continue to develop with wider accessibility for more populations to build their skills and find their next careers in additive manufacturing as it scales.
Via Essentium