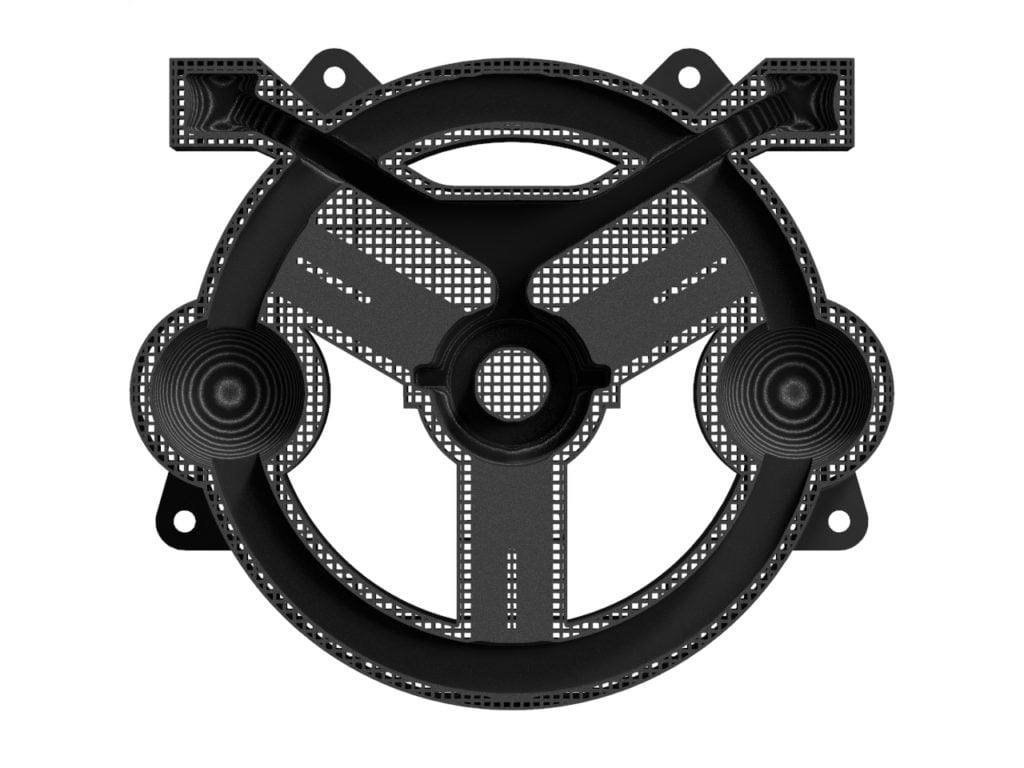
Stratasys and nTopology execs share a look at their new collaboration, starting with an impressive FDM Assembly Fixture Generator.
Design for additive manufacturing (DfAM) is a demanding discipline. It’s also one where expertise is acquired only after a steep learning curve. Additive manufacturing can’t live up to its full potential without well-executed digital designs. Anything that can make that workflow easier for users is a boon — and, really, necessary for adoption to continue to accelerate in real-world environments.
The recent announcement of a relationship between hardware leader Stratasys and software leader nTopology, then, is an exciting one in its own right. But what’s happening and what does it mean? I went to the sources for a better look.
Stratasys x nTopology
Brad Rothenberg, CEO of nTopology, and Pat Carey, Senior Vice President of Products and Solutions at Stratasys, offer a look at their companies’ collaborative efforts.
The companies will be developing accessible DfAM workflows that will be customizable to meet users’ needs. These new workflows are solutions built to solve actual issues. So they started with one of the biggest applications for 3D printing today: jigs and fixtures.
The announcement of this workflow explains:
“The FDM Assembly Fixture Generator, which is the first of several planned DfAM workflows, is designed to improve efficiency and increase productivity on the factory floor. The FDM Assembly Fixture Generator automates the design of jigs and fixtures and enables engineers to quickly turn a part file into a ready-to-print fixture with a simple drag-and-drop. It’s available now via nTop Platform.”
Speaking with Rothenberg and Carey offered a bit more background on the collaboration. It started, Rothenberg explained, similarly to how any of nTopology’s collaborative efforts with machine vendors start:
“We collaborate with all machine vendors; we’re hardware-agnostic. We think the combination of advanced software and advanced hardware will make the industry better,” he told me. “Stratasys has one of the best teams of application engineers I’ve ever met. They’ve used nTop and have identified issues customers face. So we’ve built the idea for generating jigs and fixtures in a more automated way. We thought that would have a lot of value for the industry and wanted to develop it and release it into the industry.”
The workflow, which Rothenberg adds is “pretty easy to use,” allows for plenty of tweaking. Parameters can be set, it can be tuned to the material in use on a specific machine — “most of it now is using a carbon-filled nylon,” he says — and then it generates a fractal infill pattern.
“Once we identified the problem and had a rough prototype of the workflow, we turned it around in less than two months,” Rothenberg said of the genesis of this release.
That fast turnaround is significant not only for developing and releasing a helpful tool to the industry, but it marks a new sort of workflow within Stratasys itself.
“We’ve identified a number of key partners we think will help us grow the industry,” Carey explained. “It’s a change for Stratasys. We’ve been focused internally, but now we’re looking external. We’ve been talking to nTopology for a year now. We’ve said here’s a list, let’s talk about it, let’s prioritize. We’re announcing a partnership first and our first collaboration, and we have more collaborations coming.”
FDM Assembly Fixture Generator
Working together, the teams focused on a major application for 3D printing today: jigs and fixtures.
Stratasys’ FDM 3D printers see significant use at significant companies for creating these parts. Companies like Boom Supersonic, Lockheed Martin, and Penske in demanding markets like aerospace and racing require significant tooling to make their advanced products come to life. Jigs and fixtures used in their production lines may each take two to three hours to create. That may not seem like a hefty amount of time for a custom 3D printed tool — until you multiply it by thousands. Boom, for instance, has announced use of a thousand fixtures.
Boom explained of some of its 3D printing for the XB-1 supersonic demonstrator:
“During the course of XB-1’s build, the team harnessed the F900 and 450mc’s capabilities to print more than 550 drill blocks. The blocks supported the careful assembly of the titanium fuselage along with other printed jigs, including those for the cockpit bulkhead.
The team used metrology to drill holes with the blocks, which resulted in greater accuracy. And with greater accuracy, the team mitigated potential damage to the aircraft.
By using 3D-printed drill blocks, the team kept the build on-schedule while also mitigating any potential damage to the titanium aft fuselage.
Without 3D printing, lead times for drill blocks would have been in the neighborhood of weeks, not to mention tens of thousands of dollars to fabricate out of aluminum. With in-house 3D printing, those same blocks took only a few days to print at a lower cost.”
Examining the sheer scale of tooling made allows for an understanding of how enhancing the jig-and-fixture-creation process might have a scale impact on operations:
“If they took three hours each and we can now make that three seconds each, you can imagine the savings,” Carey said of that use case.
The “number one complaint” of their customers’ 3D printing experience, he added, has been tooling. So focusing there is immediately helpful to add value.
“This workflow automates the grunt work that goes into designs like this, so engineers can focus on the actual engineering problems at hand,” Rothenberg said.
The automation is a huge benefit, but the workflow also allows for customized tweaking, which he noted as a further benefit. Generating holds, improving fractal infill, switching from PEKK to ULTEM; “It’s an open workflow, not just click in the interface and that’s it,” he added.
With this workflow, iterations can come along faster, improving designs faster.
“The biggest barrier to growth in the industry is skills,” Carey said. “We’re bound with these old toolsets that are holding us back. This workflow enables better tooling, and the more tooling we get on the factory floor, the more people are exposed to additive.”
Rothenberg agreed, adding:
“If one of your limitations is tooling and you have to wait hours, days, weeks for tooling, it’s a change to now be in a position where you can design ten different options for a part, figure it out, and fixture it quickly. Now you’re in a position where you can produce a higher-performance part right on the line. There are a ton of secondary benefits here.”
There’s more to come from this collaboration, and it sounds like we may not have long to wait to hear next steps. The teams are looking “anywhere where design is a bottleneck,” Rothenberg noted.
“There are problems specific to FDM, think thin-walled parts or support structures, that we can address and significantly improve. These are areas where Stratasys application engineers have really expert knowledge,” he said.
The collaboration will also move outside FDM, expanding to other Stratasys technologies.
For now, though, this first introduction is a huge step forward. Next week, the companies are offering a training workshop for the FDM Fixture Generator on Thursday, November 19th. The companies explain that topics will cover:
- Session 1: nTop Platform basics
- Session 2: Intro to Custom Blocks
- Session 3: Jigs & fixtures design walkthrough
- Session 4: Jigs & fixtures extensions
And, they add:
“P.S. All eligible participants will receive a free trial license of nTop Platform.”