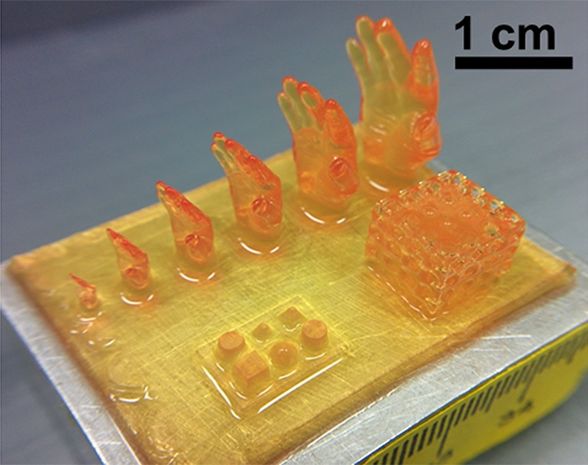
Charles R. Goulding and Arianna Coger investigate FLOAT, a new bioprinting approach.
Organ 3D printing is being increasingly researched by multiple organizations trying to find ways to make it more viable.
Several universities have previously used FDA grants to explore the potential of 3D printing to develop biological products. The University at Buffalo (UB) has recently developed a method that would make 3D printing organs less time-consuming, reducing the time it would take to print a human hand model from 6 hours to 19 minutes. An associate professor from UB, Ruogang Zhao, states, “The technology we’ve developed is 10-50 times faster than the industry standard, and it works with large sample sizes that have been very difficult to achieve previously.”
The primary authors of the UB study are Nanditha Anandakrishnan, who is currently a postdoc researcher, and Hang Ye, a research scientist currently working at the 3D printing company SprintRay Inc. Other co-authors are from the UB Department of Biomedical Engineering, the VA Western New York Healthcare System, the Department of Cell Stress Biology at Roswell Park Comprehensive Cancer Center, and the Department of Biomedical and Chemical Engineering at Syracuse University.
Stages of printing the human hand model. (Source: BioRxiv)
The researchers were able to accomplish this 3D printing using a technique known as fast hydrogel projection stereolithography technology, abbreviated as FLOAT. Hydrogel stereolithography typically uses light to photochemically shape hydrogel layers and form a structure. The FLOAT technique involves precise control of the photopolymerization condition and works well because it “significantly reduces part deformation and cellular injuries caused by the prolonged exposure to the environmental stresses you commonly see in conventional 3D printing methods,” according to Chi Zhou, another UB associate professor.
The researchers of UB say that their technique will be particularly useful for printing cells with embedded blood vessel networks. Although they are currently only able to produce centimeter-sized models, the continued development of this technology will allow greater improvements in the future.
New York State has a new life science startup cash rebate program of up to US$1.5M that could be of great assistance commercializing this technology. Federal tax incentives, such as the Research and Development (R&D) Tax Credit, are available for companies that engage in 3D printing activities.
The Research & Development Tax Credit
Whether it’s used for creating and testing prototypes or for final production, 3D printing is a great indicator that R&D Credit eligible activities are taking place. Companies implementing this technology at any point should consider taking advantage of R&D Tax Credits.
Enacted in 1981, the now permanent Federal Research and Development Tax Credit allows a credit that typically ranges from 4%-7% of eligible spending for new and improved products and processes. Qualified research must meet the following four criteria:
- Must be technological in nature
- Must be a component of the taxpayer’s business
- Must represent R&D in the experimental sense and generally includes all such costs related to the development or improvement of a product or process
- Must eliminate uncertainty through a process of experimentation that considers one or more alternatives
Eligible costs include US employee wages, cost of supplies consumed in the R&D process, cost of pre-production testing, US contract research expenses, and certain costs associated with developing a patent.
On December 18, 2015, President Obama signed the PATH Act, making the R&D Tax Credit permanent. Since 2016, the R&D credit has been used to offset Alternative Minimum Tax (AMT) for companies with revenue below $50MM and, startup businesses can obtain up to $250,000 per year in payroll tax cash rebates.
Conclusion
As the technology for 3D printing organs continues to be improved, it will become easier to model diseases realistically and develop treatments without needing as much animal testing. Within the next couple of years, it might even become possible to 3D print fully functional human organs to solve the organ transplant shortage and help humans live longer.